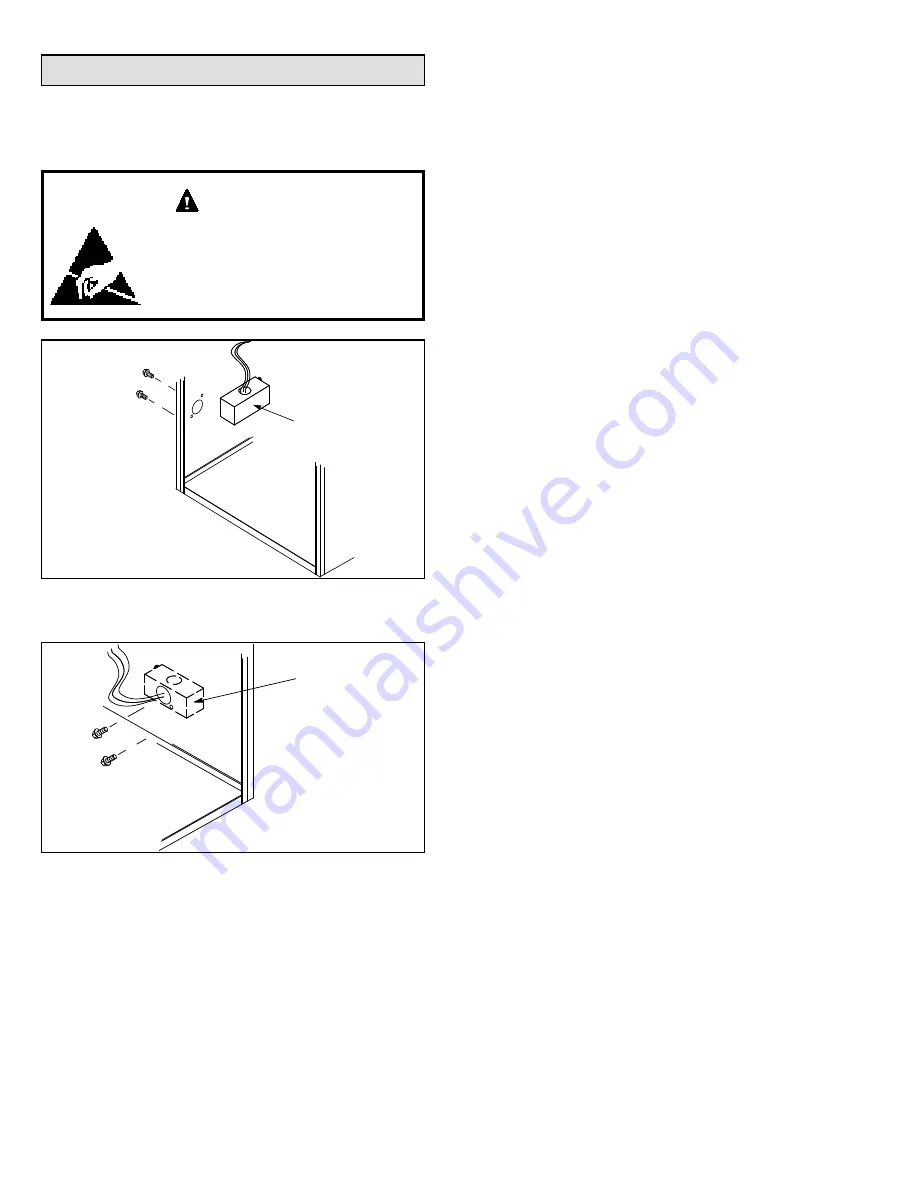
507769-04
Page 34 of 53
Issue 1927
Electrical
ELECTROSTATIC DISCHARGE (ESD)
Precautions and Procedures
Electrostatic discharge can affect
electronic
components.
Take
precautions to neutralize electrostatic
charge by touching your hand and tools
to metal prior to handling the control.
CAUTION
Figure 53.
Interior Make-Up Box
(Factory - Installed Left Side)
MAKE−UP
BOX INSIDE
CABINET
Left side
Figure 54.
Exterior Make-Up Box
(Field Provided Right Side)
MAKE−UP
BOX
OUTSIDE
CABINET
Right Side
The unit is equipped with a field makeup box on the left
hand side of the cabinet. A field-provided make-up box can
be installed on the exterior of the right side of the furnace
to facilitate installation. Seal unused openings on left side
with plugs removed from right side. Secure the excess wire
to the existing harness to protect it from damage.
Refer to Figure 56 for field wiring and Figure 57 for
schematic wiring diagram and troubleshooting.
The power supply wiring must meet Class I restrictions.
Protected by either a fuse or circuit breaker, select circuit
protection and wire size according to unit nameplate.
NOTE:
Unit nameplate states maximum current draw.
Maximum Over-Current Protection allowed is 15 AMP.
Holes are on both sides of the furnace cabinet to facilitate
wiring.
Install a separate (properly sized) disconnect switch near
the furnace so that power can be turned off for servicing.
Before connecting the thermostat or the power wiring,
check to make sure the wires will be long enough for
servicing at a later date. Make sure that thermostat wire
is long enough to facilitate future removal of blower for
service.
Complete the wiring connections to the equipment. Use the
provided unit wiring diagram and the field wiring diagram
shown in Figure 56. Use 18 gauge wire or larger that is
suitable for Class II rating for thermostat connections.
Electrically ground the unit according to local codes or,
in the absence of local codes, according to the current
National Electric Code (ANSI/HFPA No. 70) for the USA
and current Canadian Electric Code Part 1 (CSA standard
C22.1) for Canada. A green ground wire is provided in the
field makeup box.
NOTE:
The gas furnace contains electronic components
that are polarity sensitive. Make sure that the furnace is
wired correctly and is properly grounded.
Accessory Terminals
One line voltage “ACC” 1/4” spade terminal is provided
on the furnace control board. Any accessory rated up to
one amp can be connected to this terminal with the neutral
leg of the circuit being connected to one of the provided
neutral terminals. If an accessory rated at greater than
one amp is connected to this terminal, it is necessary to
use an external relay. See Figure 58 for control board
configuration. This terminal is energized when the indoor
blower is operating.
One line voltage “120 HUM” 1/4” spade terminal is provided
on the furnace integrated control board. See Figure 58 for
integrated control configuration. This terminal is energized
in the heating mode when the combustion air inducer is
operating. Any humidifier rated up to one amp can be
connected to this terminal with the neutral leg of the circuit
being connected to one of the provided neutral terminals. If
a humidifier rated at greater than one amp is connected to
this terminal, it is necessary to use an external relay.
One 24V “H” 1/4” spade terminal is provided on the furnace
integrated control board. See Figure 58 for control board
configuration. The terminal is energized in the heating
Summary of Contents for 96G1DFE
Page 30: ...507769 04 Page 30 of 53 Issue 1927 Figure 50 Trap Drain Assembly Using 1 2 PVC or 3 4 PVC ...
Page 36: ...507769 04 Page 36 of 53 Issue 1927 Figure 57 Typical Wiring Diagram ...
Page 48: ...507769 04 Page 48 of 53 Issue 1927 Troubleshooting Heating Sequence of Operation ...
Page 49: ...507769 04 Page 49 of 53 Issue 1927 Troubleshooting Heating Sequence of Operation continued ...
Page 50: ...507769 04 Page 50 of 53 Issue 1927 Troubleshooting Cooling Sequence of Operation ...
Page 51: ...507769 04 Page 51 of 53 Issue 1927 Troubleshooting Continuous Fan Sequence of Operation ...