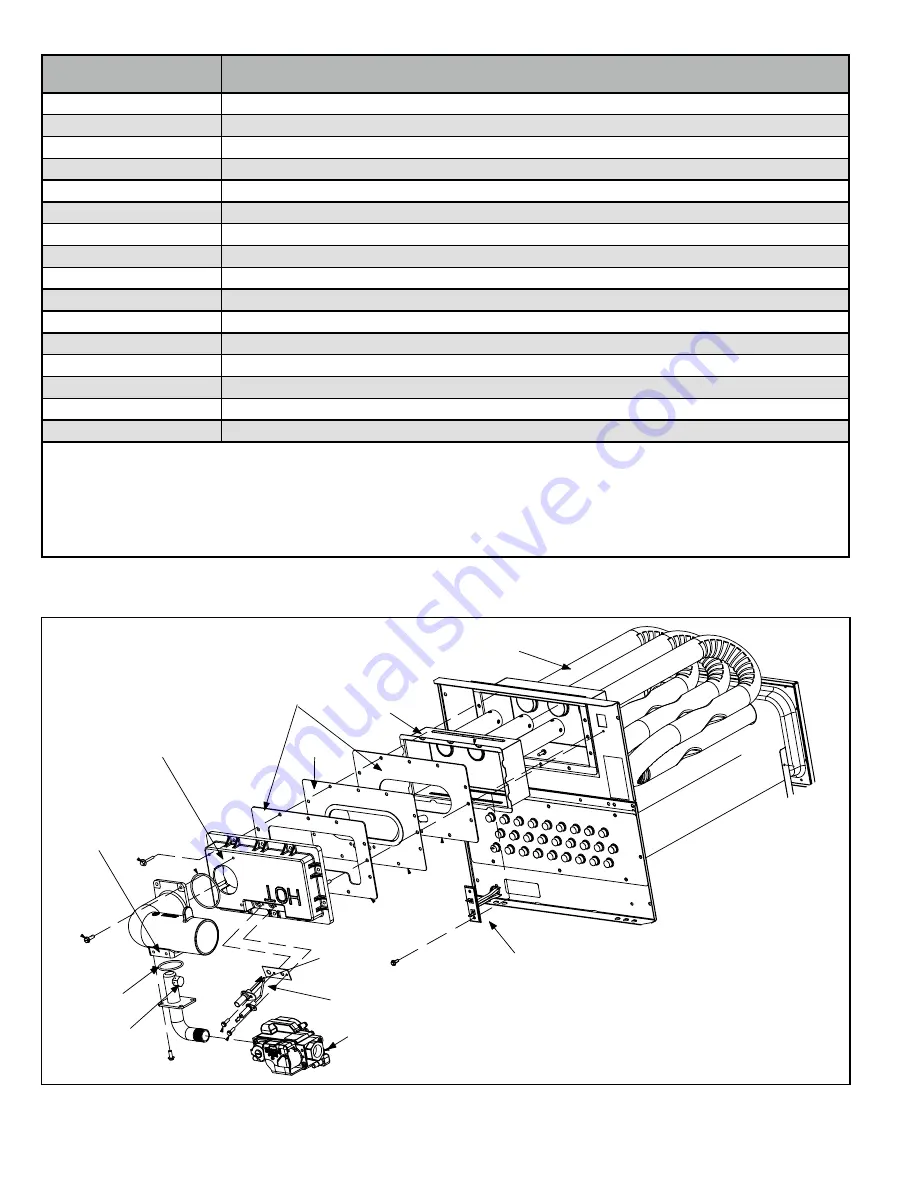
508034-02
Issue 2135
Page 8 of 49
Red LED Flash Code
2
Diagnostic Codes / Status of Furnace
Off
No power to control or board fault detected
On
Board fault detected
Heartbeat
1
Control powered - displayed during all modes of operation if no errors are detected
1 flash
Reverse line voltage polarity
2 flashes
Improper earth ground
3 flashes
Burner failed to light, or lost flame during heating demand
4 flashes
Low flame signal - check flame sensor
5 flashes
Watchguard - burner failed to light, exceeded maximum number or retries or recycles
6 flashes
Not used
7 flashes
Primary or secondary limit open or Watchguard mode - limit switch open longer than 3 minutes
8 flashes
Rollout switch open
9 flashes
Pressure switch failed to close of opened during heat demand
10 flashes
Watchguard - pressure switch opened 5 times during one heat demand
11 flashes
Pressure switch stuck closed prior to activation or combustion air inducer
12 flashes
Flame sensed without gas valve energized
13 flashes
Low line voltage
1
A “Heartbeat” is indicated by a “Slow Flash” - 1 sec on 1 sec off, repeating
2
Error codes are indicated by a “rapid flash” - the LED flashes X times at ½ second on ½ second off, remains off for 3 seconds then
repeats.
Last 10 error codes are stored in memory including when power is shut off to the unit. - To recall, press and release button, most
recent will be displayed first, LED off for 3 sec, then next error code is displayed, etc. To clear error codes, depress and hold button
longer than 5 seconds.
Table 4. Diagnostic Codes
Gas Valve
Primary Limit
Ignitor
Sensor
Gas Orifice
Air Orifice
Rollout Switch
(location)
Air Gas Plenum
Gaskets
Burner
Heat Exchanger
Burner Box
Figure 4. Heating Components