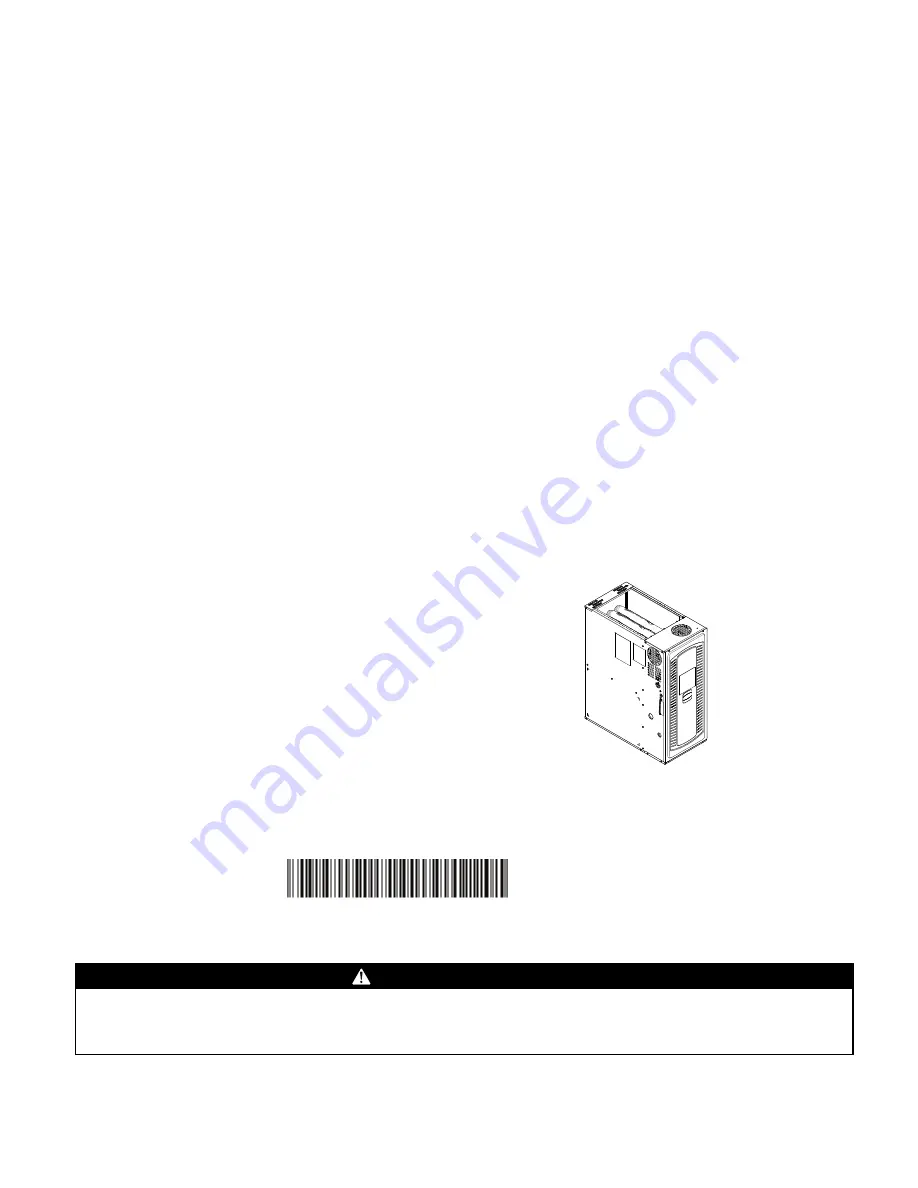
S
SA
AF
FE
ET
TY
Y W
WA
AR
RN
NIIN
NG
G
Only qualified personnel should install and service the equipment. The installation, starting up, and servicing of heating, ventilating, and air-conditioning
equipment can be hazardous and requires specific knowledge and training. Improperly installed, adjusted or altered equipment by an unqualified person
could result in death or serious injury. When working on the equipment, observe all precautions in the literature and on the tags, stickers, and labels that
are attached to the equipment.
May 2020
1
18
8--C
CE
E0
09
9D
D1
1--1
1E
E--E
EN
N
Upflow/Downflow/Horizontal Left/Right
Gas-Fired, Single Stage Induced Draft Furnaces with High
Efficiency Motor
U
Up
pffllo
ow
w,, D
Do
ow
wn
nffllo
ow
w,, H
Ho
orriizzo
on
ntta
all R
Riig
gh
htt//L
Le
efftt
Single Stage
S8B1A026M2PSAB
S8B1A040M3PSAB
S8B1B040M2PSAB
S8B1B060M3PSAB
S8B1B060M4PSAB
S8B1B080M4PSAB
S8B1C080M5PSAB
S8B1C100M5PSAB
S8B1D120M5PSAB
N
No
otte
e:: This installer’s Guide is used for multiple furnace families. Models
may have a “T” in the 12th digit designating they meet California less
than 40 ng/J (NOx) emissions requirements.
N
No
otte
e:: Graphics in this document are for
representation only. Actual model may
differ in appearance.
18-CE09D1-1E-EN
Installer’s Guide
Summary of Contents for S8B1A026M2PSAB
Page 12: ...12 18 CE09D1 1E EN Outline Drawings Table 2 14 5 Width Cabinet ...
Page 13: ...18 CE09D1 1E EN 13 Table 3 17 5 Width Cabinet O Ou ut tl li in ne e D Dr ra aw wi in ng gs s ...
Page 14: ...14 18 CE09D1 1E EN Table 4 21 Width Cabinet O Ou ut tl li in ne e D Dr ra aw wi in ng gs s ...
Page 15: ...18 CE09D1 1E EN 15 Table 5 24 5 Width Cabinet O Ou ut tl li in ne e D Dr ra aw wi in ng gs s ...
Page 57: ...18 CE09D1 1E EN 57 N No ot te es s ...
Page 58: ...58 18 CE09D1 1E EN N No ot te es s ...