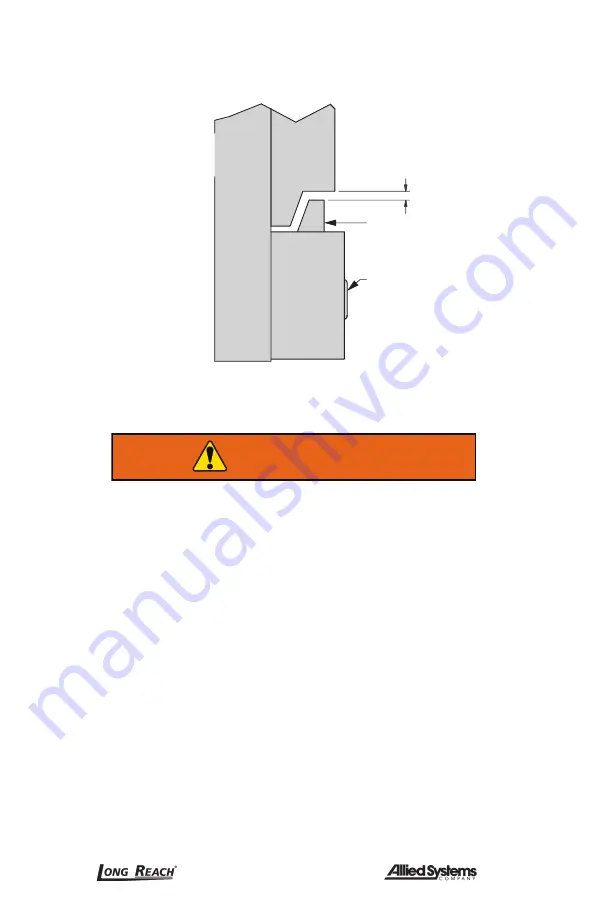
45-009 REV. 8/20
21
4.2.2 Installations with Quick Hooks
1. Follow steps 1-5 under bolt-on hooks.
Maximum
Clearance
3/32"
Quick
Hook
Attachment
Frame
Slide
Button
Truck
Mast
Figure 4-7, Quick hook inspection
2.
Raise the slide plate until the button clicks into place.
WARNING
The attachment could fall off the truck if the quick hook
is not properly installed.
Slide plate must click into place. If the slide plate does
not click into place because the truck carriage prevents
the slide plate from being raised up high enough, install
shims between the attachment and the body of the quick
hooks.
4.2.3 Installations with Sideshift
1.
Center the truck behind the attachment and drive toward it with the mast tilted
forward about 4 degrees.
2.
Place the midplate onto the ITA bar. Make sure it is seated all the way down on the
bar. Make sure the locking lug is in the notch closest to the center of the truck's
carriage.
3.
Slowly raise the truck carriage completely to engage the top hooks with the truck carriage.
Tilt carriage back until the unit is against the carriage bottom fork bar (0 degrees).