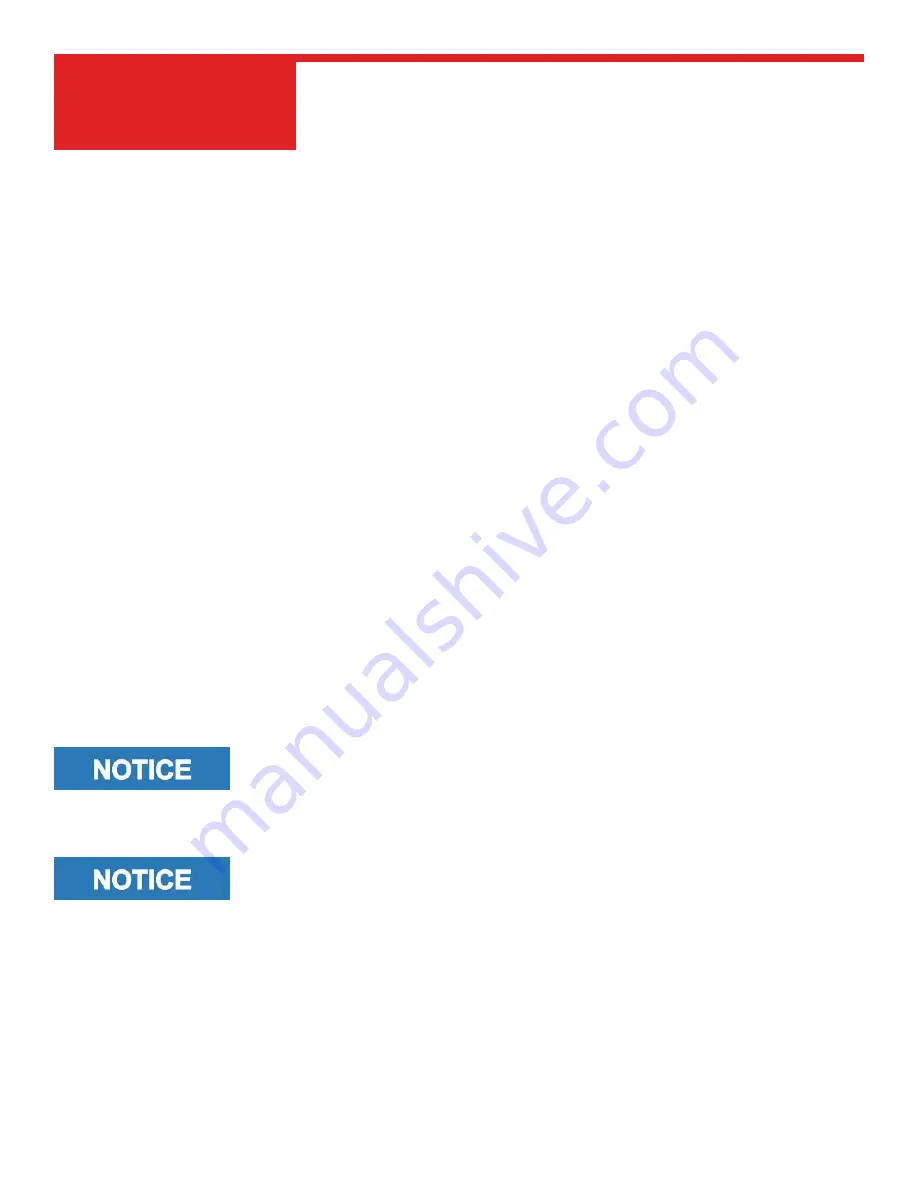
057625 - 10/2012
SECTION 2
OPERATIONS
Page 2-2
2.1 General Information
The RS Series Roller Screeds are self-propelled and are hydraulically driven and require only one op-
erator, two laborers and two concrete placers. The screed is expandable from 14 ft. (4.26 m) to 34 ft.
(10.36 m).
Before shipment, this Roller Screed was tested at the factory. If there are any problems with the screed,
please contact the nearest AEC service center.
The purpose of the roller screed is to strike off the surface of the concrete at a specified grade. The
drive rollers on the screed ride on steel tube rails or forms, allowing the paving tube to work the con-
crete to the desired grade.
The strike tube rotation should always push the concrete forward into areas that have not yet received
the concrete. Depending on the slump of the concrete, several passes might be required for the right
strike off grade.
Some of the applications the screed can be used for are: suspended slabs, slabs on grade, tilt-up
panels, roads, post-tension slabs, bridges, elevated decks, runways, highway rehabilitation and white
topping.
A precision straightening process insure that the paving tube precisely levels the concrete surface to
grade. AEC’s advanced paving tube design leaves aggregate at the surface for harder, longer wearing
slabs and can strike off concrete with slumps as low as 1-inch (2.54 cm.).
Paving tubes are available in various lengths. Paving tubes are a critical component of the roller screed.
If the paving tubes are damaged, it is possible they will not turn true (rotate correctly). Replace them
accordingly.
Read all instructions carefully before operating the Roller Screed. Improper setup, use or maintenance
of the equipment could result in personnel injury or damage to the equipment.
Care should be taken to store reserved (not used) paving tubes on a fully supported level surface.
NEVER
lift the screed from the paving tubes.
Summary of Contents for RS844
Page 1: ...OPERATIONS PARTS MANUAL RS844 057625 10 2012 Roller Screed ...
Page 15: ...057625 10 2012 SECTION 1 SAFETY Page 1 1 Section 1 SAFETY ...
Page 16: ...057625 10 2012 SECTION 1 SAFETY Page 1 2 State Regulations Proposition 65 Warning ...
Page 17: ...057625 10 2012 SECTION 1 SAFETY Page 1 3 Federal Regulations Respiratory Hazards ...
Page 27: ...057625 10 2012 SECTION 2 OPERATIONS Page 2 1 Section 2 OPERATIONS ...
Page 39: ...057625 10 2012 SECTION 3 SERVICE Page 3 1 Section 3 SERVICE ...
Page 48: ...057625 10 2012 SECTION 3 SERVICE Page 3 10 Notes ...
Page 49: ...057625 10 2012 SECTION 4 PARTS Page 4 1 Section 4 PARTS ...
Page 56: ...057625 10 2012 SECTION 4 PARTS Page 4 8 Center Auger Bearing Housing Illustration 1 2 4 3 6 5 ...
Page 70: ...057625 10 2012 SECTION 4 PARTS Page 4 22 Drive Tube Assembly Illustration 3 7 1 2 4 5 6 8 ...
Page 72: ...057625 10 2012 SECTION 4 PARTS Page 4 24 Drive Tube Scraper Assembly Illustration 4 5 3 2 1 ...
Page 78: ...057625 10 2012 SECTION 4 PARTS Page 4 30 Power Jack Assembly cont d Illustration 5 2 1 4 3 ...
Page 88: ...057625 10 2012 SECTION 4 PARTS Page 4 40 Fuel Filter Replacement PART 70000 43081 PART 043920 ...
Page 89: ...057625 10 2012 SECTION 4 PARTS Page 4 41 Oil Filter Replacement PART 16271 32090 ...
Page 105: ...057625 10 2012 SECTION 4 PARTS Page 4 57 Spray System Schematic ...
Page 123: ...057625 10 2012 SECTION 4 PARTS Page 4 75 Hydraulic Hose Matrix Parts List ...
Page 124: ...057625 10 2012 SECTION 4 PARTS Page 4 76 Engine Electrical Schematic Illustration ...
Page 125: ...057625 10 2012 SECTION 4 PARTS Page 4 77 Engine Electrical Schematic Illustration ...
Page 126: ...057625 10 2012 SECTION 4 PARTS Page 4 78 Machine Electrical Schematic Illustration ...
Page 127: ...057625 10 2012 SECTION 4 PARTS Page 4 79 Machine Electrical Schematic Illustration ...