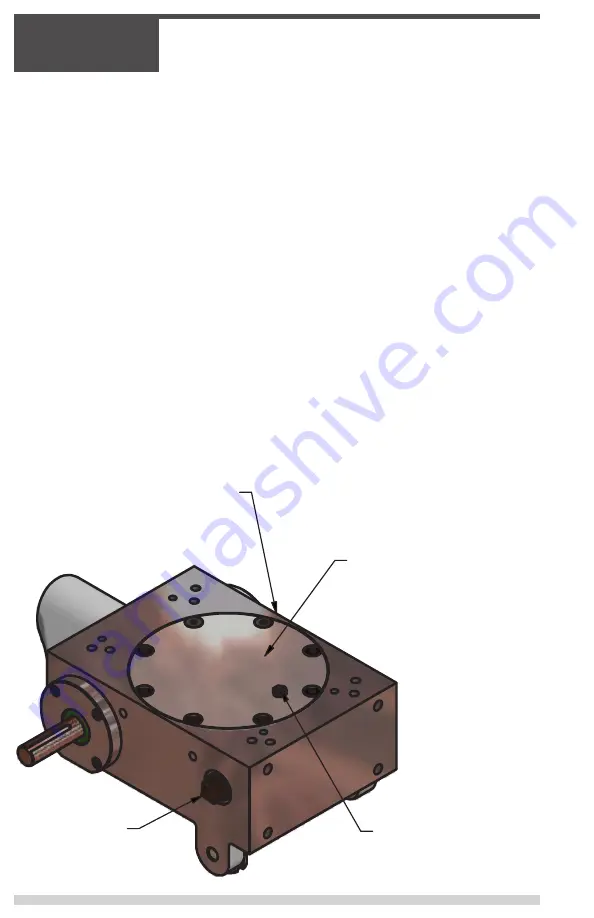
SECTION 3
SERVICE
068521
Page 36
Trowel Gearbox
GEARBOX (015202)
FILL PLUG
FILL PLUG LOCATION
TOP COVER
RELIEF VALVE
Trowel Gearbox Maintenance
Check Oil levels in the gearbox daily (every 8 hours) Add oil if oil level is
below the check sight glass.
1. To add oil, tilt gearbox to the side and remove the fill plug. Add oil
through hole opening. Replace fill plug after proper level has been
achieved. Fill so that there is oil 1/2 way in the sight glass. Use Allen
Oil only.
Summary of Contents for 068344
Page 5: ...068521 Page 5 GENERAL INFORMATION ...
Page 11: ...068521 Page 11 SECTION 1 SAFETY SECTION 1 SAFETY ...
Page 24: ...SECTION 2 OPERATION 068521 Page 24 SECTION 2 OPERATION ...
Page 29: ...068521 Page 29 SECTION 2 OPERATION PAGE LEFT BLANK INTENTIONALLY ...
Page 31: ...068521 Page 31 SECTION 2 OPERATION Trowel Controls 1 5 8 2 3 6 10 12 9 13 15 14 4 11 ...
Page 34: ...SECTION 3 SERVICE 068521 Page 34 SECTION 3 SERVICE ...
Page 39: ...068521 Page 39 SECTION 4 ACCESSORIES SECTION 4 ACCESSORIES ...
Page 40: ...SECTION 4 ACCESSORIES 068521 Page 40 Accessories ...