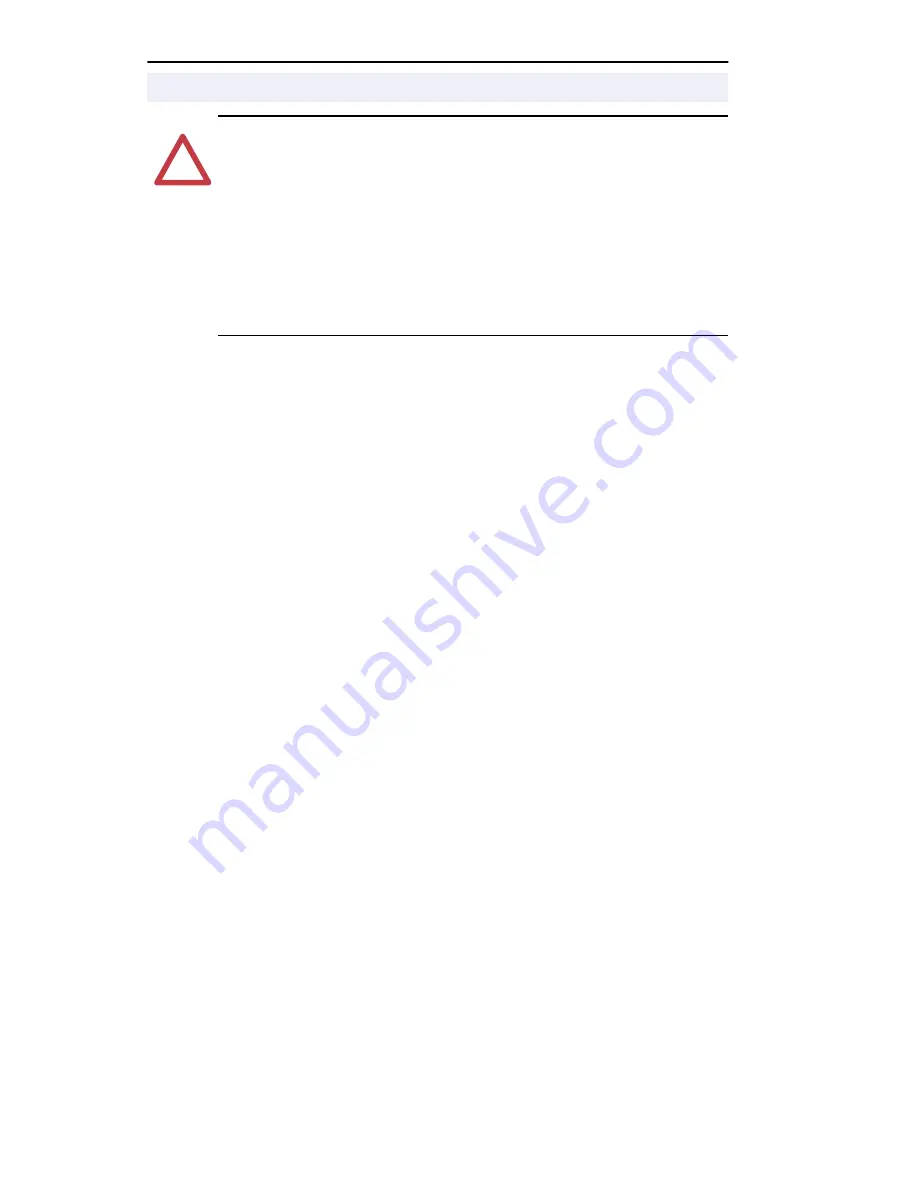
English-6
Before Applying Power to the Drive
❏
1.
Confirm that all inputs are connected to the correct terminals and are
secure.
❏
2.
Verify that AC line power at the disconnect device is within the rated
value of the drive.
❏
3.
Verify that any digital control power is 24 volts.
❏
4.
Verify that the Sink (SNK)/Source (SRC) Setup DIP Switch is set to
match your control wiring scheme. See page 5 for location.
Important:
The default control scheme is Source (SRC). The Stop
terminal is jumpered (I/O Terminals 01 and 11) to allow
starting from the keypad. If the control scheme is changed
to Sink (SNK), the jumper must be removed from I/O
Terminals 01 and 11 and installed between I/O Terminals
01 and 04.
❏
5.
Verify that the Stop input is present or the drive will not start.
Important:
If I/O Terminal 01 is used as a stop input, the jumper
between I/O Terminals 01 and 11 must be removed.
Applying Power to the Drive
❏
6.
Apply AC power and control voltages to the drive.
❏
7.
Familiarize yourself with the integral keypad features (see next page)
before setting any Program Group parameters.
Start, Stop, Direction and Speed Control
Factory default parameter values allow the drive to be controlled from
the integral keypad. No programming is required to start, stop, change
direction and control speed directly from the integral keypad.
Important:
To disable reverse operation, see A095 [Reverse Disable].
If a fault appears on power up, refer to page 11 for an explanation of the
fault code. For complete troubleshooting information, refer to the
PowerFlex 4
User Manual
on the CD supplied with the drive.
Prepare For Drive Start-Up
!
ATTENTION:
Power must be applied to the drive to perform the
following start-up procedures. Some of the voltages present are at
incoming line potential. To avoid electric shock hazard or damage to
equipment, only qualified service personnel should perform the
following procedure. Thoroughly read and understand the procedure
before beginning. If an event does not occur while performing this
procedure,
Do Not Proceed
.
Remove All Power
including user
supplied control voltages. User supplied voltages may exist even when
main AC power is not applied to the drive. Correct the malfunction
before continuing.
All manuals and user guides at all-guides.com
all-guides.com