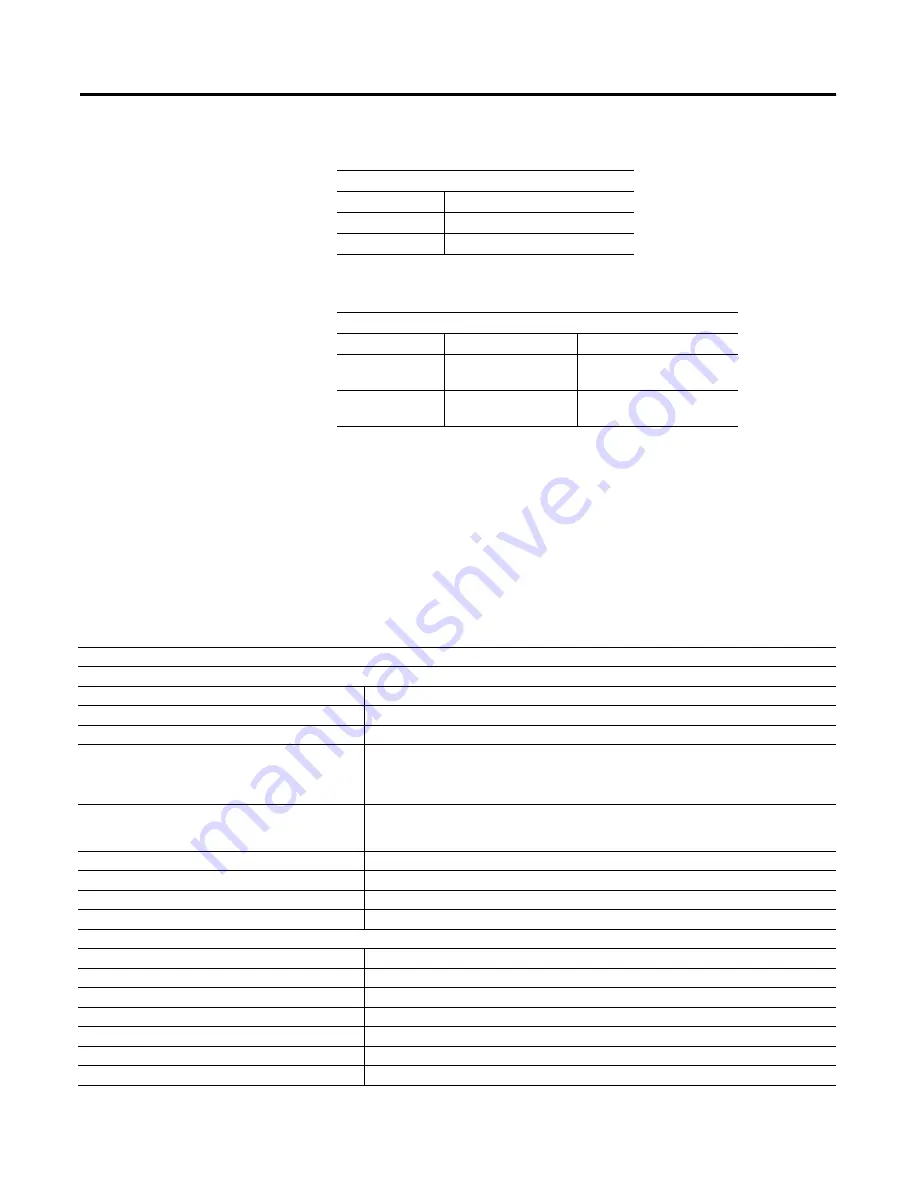
Publication 1732D-IN001B-EN-E - May 2004
DeviceNet 1732 ArmorBlock I/O, Series A
13
The following table describes the auxiliary power indicator.
The following table describes individual I/O status indicators.
This product has been tested at an Open DeviceNet Vendor
Association, Inc. (ODVA) authorized independent test laboratory and
found to comply with ODVA Conformance Test. Please contact the
ODVA website (http://www.odva.org) for listing of products tested by
ODVA independent test labs for further details.
Specifications
Following are specifications for the 1732 ArmorBlock I/O modules.
Auxiliary Power
Indication
Status
None
No Auxiliary Power
Solid Green
Auxiliary Power Present
I/O Status Indicators
Function
Point Indicator
Condition
Outputs
None
Yellow
Output not energized
Output energized
Inputs
None
Yellow
No valid input
Valid input
DeviceNet 1732 ArmorBlock I/O Series A
Input Specifications
Inputs
61131-2 Type 3 Compatible
Sensor Source Current, Maximum (per input)
50mA
Sensor Source Current, Maximum (per module)
400mA
Sensor Source Voltage
(auxiliary power=12-30V dc)
Maximum
Minimum
30V
11V
On-state Voltage
Maximum
Minimum
30V dc
11V dc
On-state Current, Maximum
5mA
Off-state Voltage, Maximum
5V dc
Off-state Current, Maximum
1.5mA
Input Delay Time - ON to OFF and OFF to ON, Maximum
0-16000
µ
s
Output Specifications
Outputs
61131-2 Compatible
Off-state Peak Blocking Voltage, Minimum
30V
On-state Voltage Drop, Maximum
0.5V
On-state Current, Maximum
0.5A
Off-state Leakage, Maximum
50
µ
A
Module Current, Maximum (all outputs)
4.0A
Surge Current for 10ms, repeatable every 2s, Maximum
1.2A