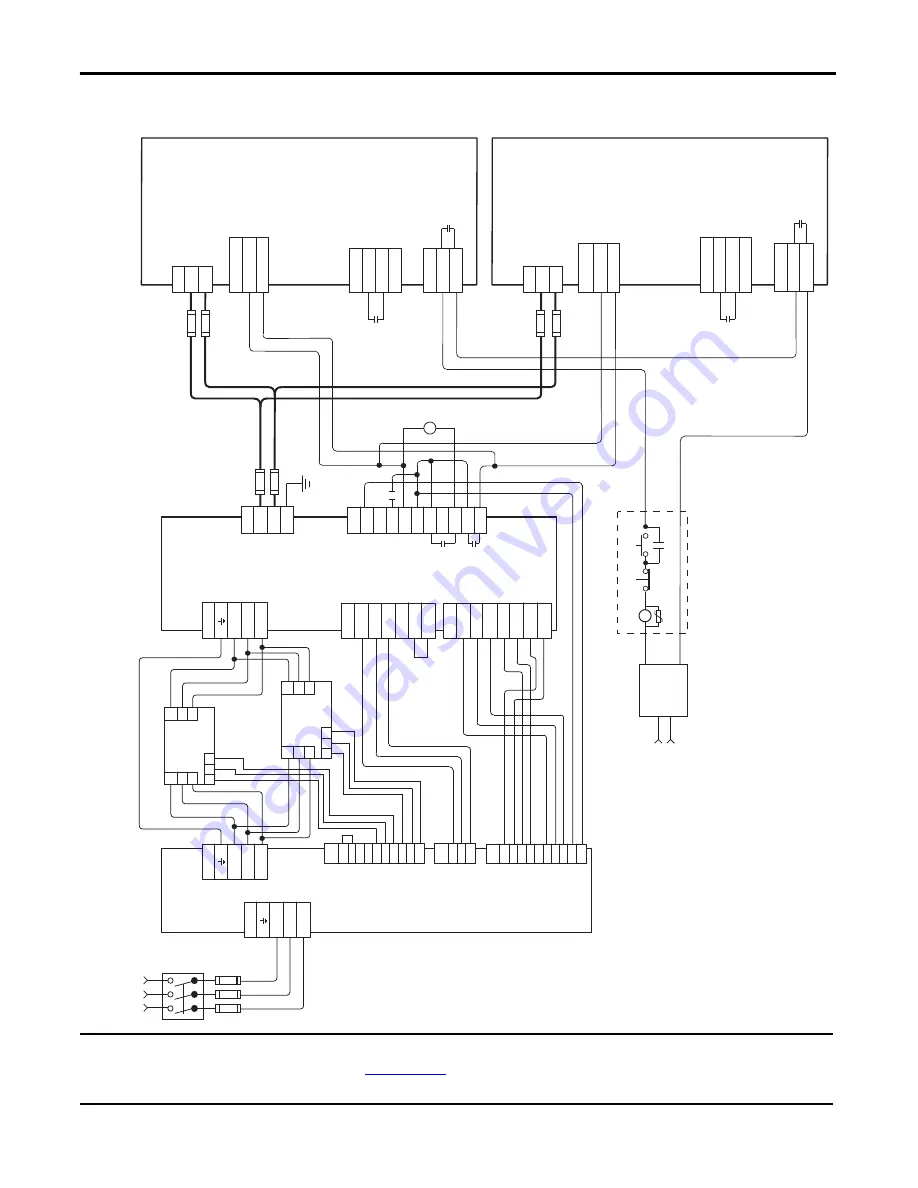
170
Rockwell Automation Publication 2099-UM001D-EN-P - December 2012
Appendix B
Interconnect Diagrams
Figure 79 - 8720MC-RPS190BM Regenerative Power Supply to Multiple Kinetix 7000 Drives
IMPORTANT
This configuration requires the power regenerative mode settings as described in the 8720MC Regenerative Power Supply
Installation Manual, publication
, and setting of the power tab in RSLogix 5000 software is set to the
appropriate bus regulator catalog number. Common mode capacitors should be disconnected on DC common bus drives.
L1
L2
L3
TB1
TB1
DC+
DC-
L1
L2
L3
TB1
L4
L5
L6
TB1
L1 AUX
L2 AUX
L3 AUX
PR1
PR2
PR3
TB2
MC
RST
PWR
0V
24V
COM
IP
RDY
FR
FR
TB3
Fault Relay Contact
L1
L2
L3
L4
L5
L6
RED
BLK
YLW
Fan 2
CN1
A1 A2 A3 A4 A5 B1 B2 B3 B4 B5
CN2
A1 A2 A3 A4 A5 B1 B2 B3 B4 B5
CN4
1 2 3
+24V3
0V3
SENS
+24V2
0V2
MC1
TB4
MC2
R1 S1 T1
MC1 MC2
+24V2
0V2 NC
+24V3
0V3
SENS-out
+24V
MC
RED
WHT
BLU
RED
BLK
YLW
GND
*Circuit Breaker See N\ote 2
*Inp
ut
Fusing See Note 2
Regenerative Power Supply
8720MC-RPS190BM
DC Bus
Connections
120V/240V AC
or
24V DC
Line Reactor
872
0MC
-LR1
0-1
00B
EMC Line F
ilter
87
20
MC-
EF1
90-
VB
* Ind
icates U
ser Su
ppl
ied
Com
pon
en
t
*S
ingl
e-pha
se
AC Line Filter
*T
hr
ee
-p
ha
se
In
put
(+10/-15%) 380V AC RMS, 50 Hz or 460V AC RMS, 60 Hz See Note 1
L1
L2
L3
L4
L5
L6
Fan 3
Line Reactor
872
0MC
-LR1
0-1
00B
*DC Line Fuses
2
8
7
2
8
7
DC+
DC-
TB
24V DC
ENABLE
24V COM
IOD - Axis 1
GPR2+
GPR2-
GPR - Axis 1
REGEN COM
REGEN OK
GPIO - Axis 1
DC+
DC-
TB
GPR2+
GPR2-
GPR - Axis
n
REGEN COM
REGEN OK
GPIO - Axis
n
24V DC
ENABLE
24V COM
IOD - Axis
n
1
1
CR2* See
Note 11
CR2* See
Note 11
Con
trol
Stop String See Notes 6 and 8
DC Bus Connections
Power Co
nn
ections
DC Bus Connections
Power Co
nn
ections
Kinet
ix 7000
Drive
2099
-BM
xx
-S
* DC Line
Fuses
(see table in Appendix A)
* DC Line
Fuses
(see table in Appendix A)
Ad
ditional connecti
ons required,
but
not
shown in this diagram: 1. +24V DC Control Power 2. Motor Feedback, Brake (if used), and Power 3. Drive I/O and Communications
Con
trol
Stop String See Notes 6 and 8
Kinet
ix 7000
Drive
2099
-BM
xx
-S
5
6
5
6
STOP*
START (RPS On)*
CR1*
CR1*
RPS S
top
-Sta
rt St
ring
*
CR1*
CR2*