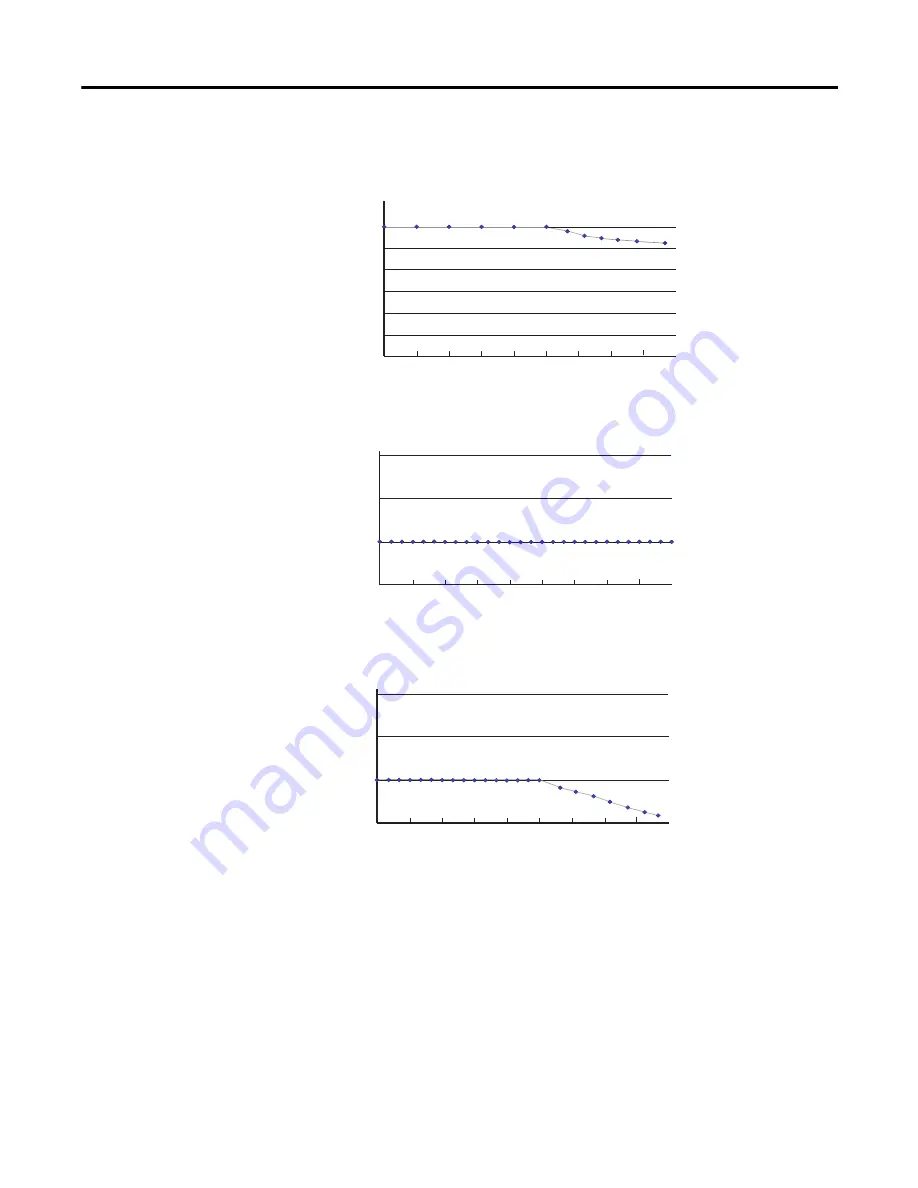
Rockwell Automation Publication 2080-UM004C-EN-E - March 2015
71
Specifications
Appendix
A
Maximum output voltage – 24V DC operation
Maximum output currrent per point – 5V DC operation
Maximum output current per point – 24V DC operation
-20
-10
0
10
20
30
40
50
60
70
0
5
10
15
20
25
30
35
Vo
lts
(DC
)
Ambient Temperature (°C)
Voltage Derating Based on Temperature
26.4V DC @ 65 °C
-20
-10
0
10
20
30
40
50
60
70
0
0.5
1
1.5
Cur
rent per poin
ts
(A)
Ambient Temperature (°C)
Current Derating Based on Temperature
-20
-10
0
10
20
30
40
50
60
70
0
0.5
1
1.5
Curre
nt p
er p
oint
s
(A)
Ambient temperature (°C)
Current derating based on temperature