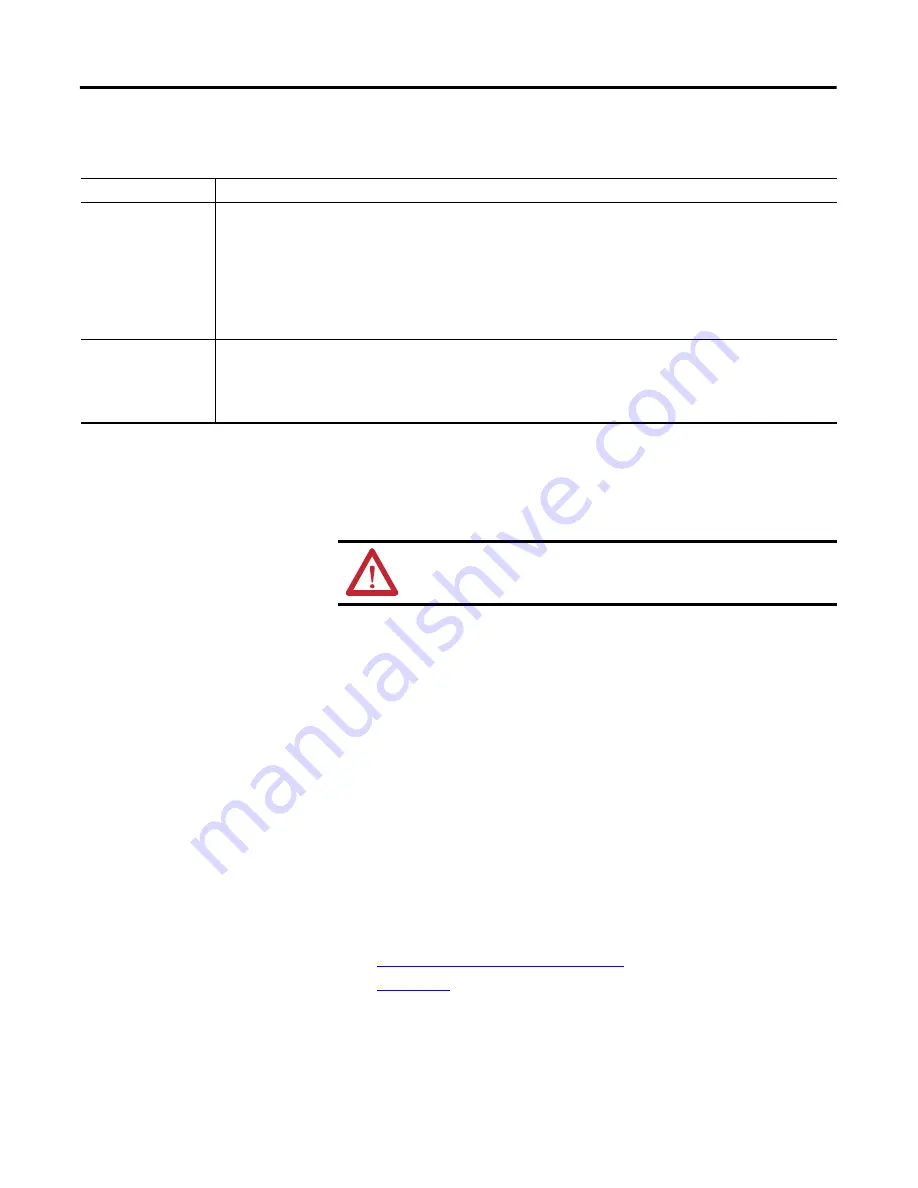
8
Rockwell Automation Publication 1756-PM004D-EN-P - September 2012
Chapter 1
Communicate with I/O Modules
Requested Packet Interval
The Logix5000 controller uses connections to transmit I/O data.
In Logix5000 controllers, I/O values update at a period that you configure via the
I/O configuration folder of the project. The values update asynchronous to the
execution of logic. At the specified interval, the controller updates a value
independently from the execution of logic.
·
Programs within a task access input and output data directly from
controller-scoped memory.
·
Logic within any task can modify controller-scoped data.
·
Data and I/O values are asynchronous and can change during the course of
a task’s execution.
·
An input value referenced at the beginning of a task’s execution can be
different when referenced later.
·
To prevent an input value from changing during a scan, copy the value to
another tag and use the data from there (buffer the values).
Communication Format
The communication format that you choose determines the data structure for the
tags that are associated with the module. Many I/O modules support different
formats. Each format uses a different data structure. The communication format
that you choose also determines:
·
Direct or Rack-Optimized Connection.
·
Term
Definition
Connection
A communication link between two devices, such as between a controller and an I/O module, PanelView terminal, or another controller.
Connections are allocations of resources that provide more reliable communications between devices than unconnected messages. The number of
connections that a single controller can have is limited.
You indirectly determine the number of connections the controller uses by configuring the controller to communicate with other devices in the
system. The following types of communication use connections:
·
I/O modules
·
produced and consumed tags
·
certain types of Message (MSG) instructions (not all types use a connection)
Requested packet interval
(RPI)
The RPI specifies the period at which data updates over a connection. For example, an input module sends data to a controller at the RPI that you
assign to the module.
·
Typically, you configure an RPI in milliseconds (ms). The range is 0.2 ms (200 microseconds)
…
750 ms.
·
If a ControlNet network connects the devices, the RPI reserves a slot in the stream of data flowing across the ControlNet network. The timing of
this slot may not coincide with the exact value of the RPI, but the control system guarantees that the data transfers at least as often as the RPI.
ATTENTION:
Make sure that data memory contains the appropriate values
throughout a task’s execution. You can duplicate or buffer data at the
beginning of the scan to provide reference values for your logic.
Summary of Contents for 1756-L65 ControlLogix 5565
Page 4: ...2 Rockwell Automation Publication 1756 PM004D EN P September 2012 Summary of Changes Notes...
Page 8: ...6 Rockwell Automation Publication 1756 PM004D EN P September 2012 Preface Notes...
Page 66: ...64 Rockwell Automation Publication 1756 PM004D EN P September 2012 Chapter 3 Force I O Notes...
Page 88: ...86 Rockwell Automation Publication 1756 PM004D EN P September 2012 Index...
Page 89: ......