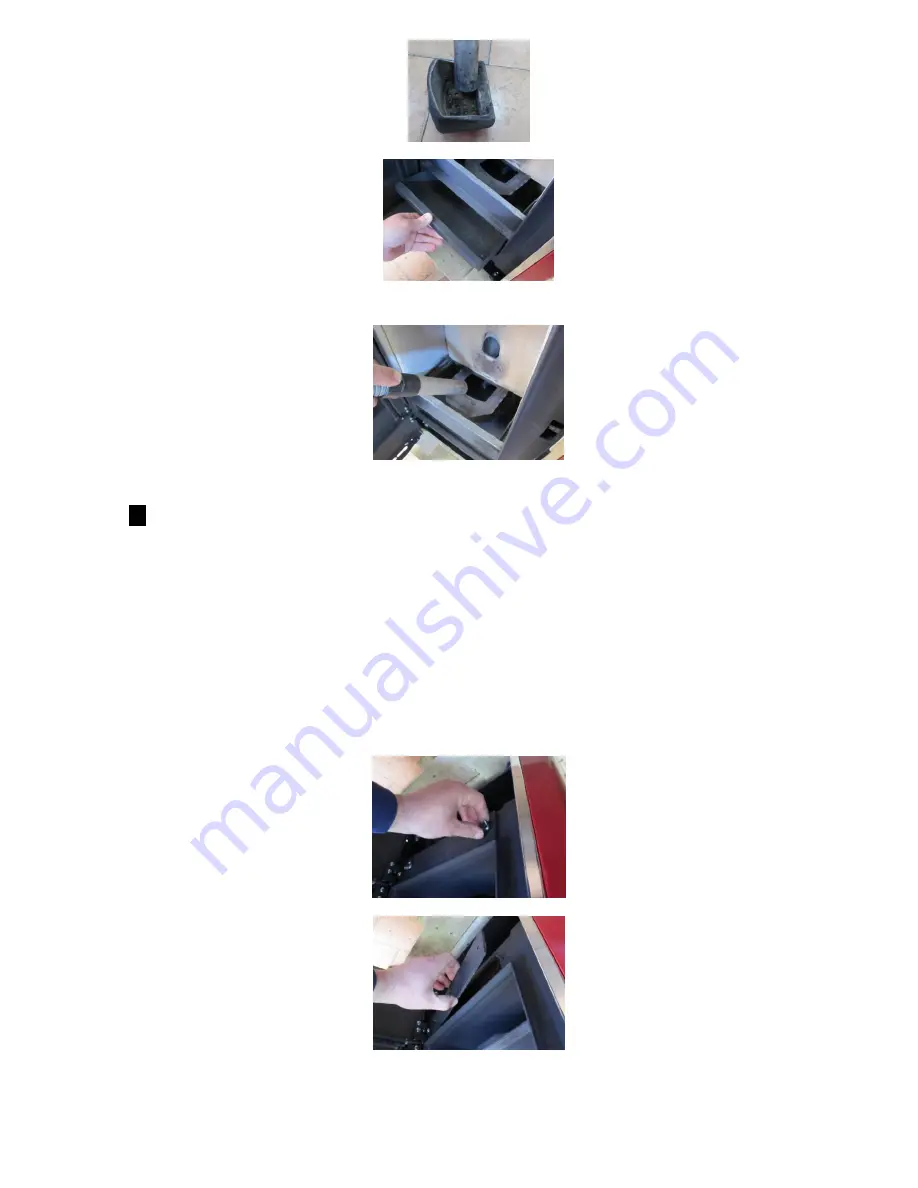
20
5.
Remove the ash tray by hand and empty it.
6.
Use a vacuum of sufficient power (1000-1300W) to remove all the ash accumulated in the combustion chamber,
the ash pan and the door.
After you've finished cleaning, re-assemble all the elements in the reverse order from the order in which you removed
them.
Special maintenance
Activities of special cleaning and maintenance (types 2 and 3) help the furnace to keep its heating and functional
characteristics for a longer time.
To ensure that the maintenance of the furnace is not in vain, it is necessary to maintain a system for extraction of
smoke just as thoroughly.
5.2.1
SPECIAL MAINTENANCE ACTIVITIES TYPE 2
In addition to maintenance activities Type 1, maintenance activities Type 2 must be carried out at about 350-400 hours,
or else after about 500~600 kg of fuel.
⚠
ATTENTION: Each cleaning activity has to be performed when the furnace is completely cold and disconnected from
the power supply (with the cable pulled out from the socket).
⚠
ATTENTION: Be sure that ash is completely cold before you start cleaning. Once you observe that ash is cold, you
may vacuum it with a vacuum cleaner.
The activities of periodic maintenance Type 2 shall be performed in accordance with the following procedure:
1.
Unscrew and remove the 4 M6 screws that hold the chamber cover for collecting of dust on the heat exchanger.
2.
Remove the cover from the dust chamber on the heat exchanger.
3.
Remove the soot with a shovel, and use the vacuum cleaner to pick up the remaining soot and ashes from the
dust chamber on the heat exchanger. To properly remove the soot and ash on CSA9 model, it is also necessary to remove