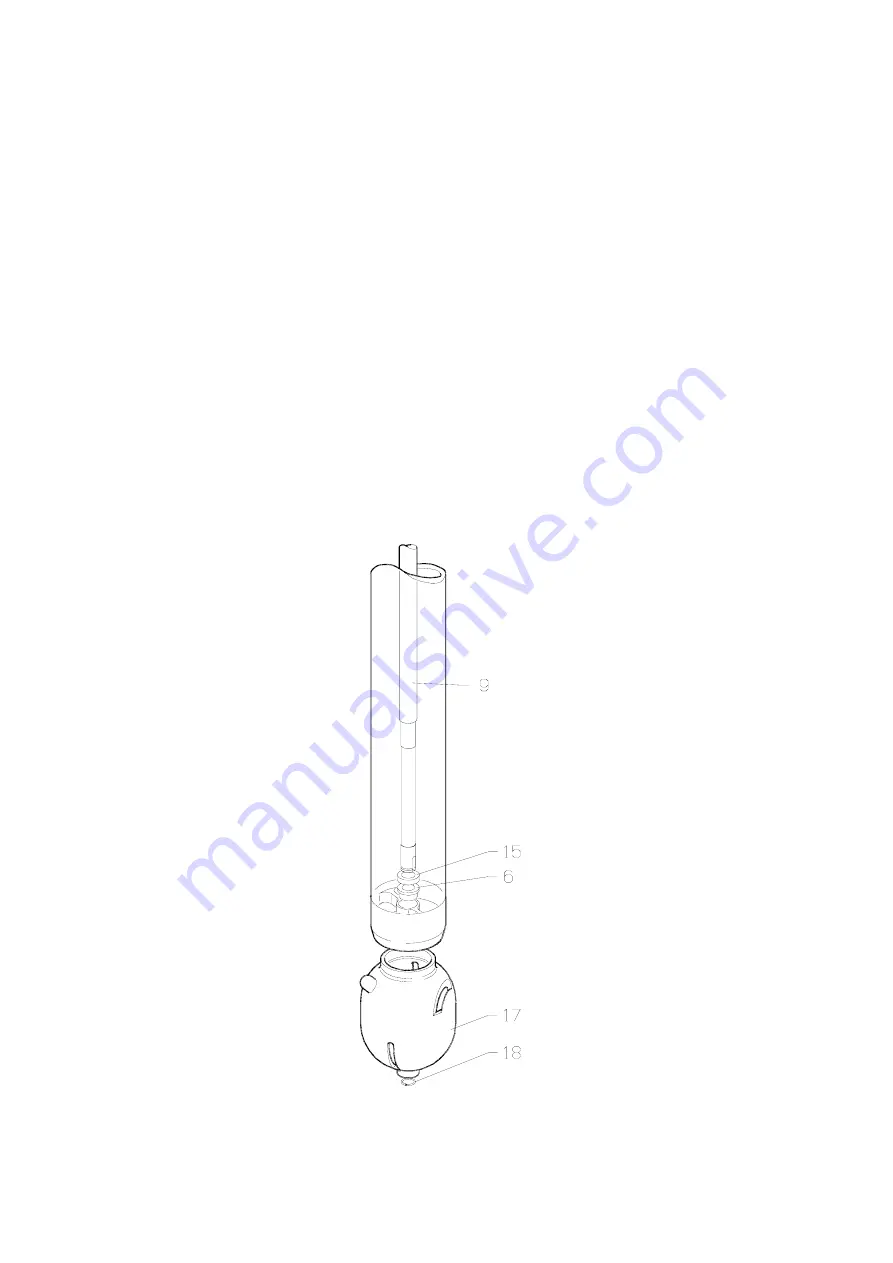
Maintenance and repair
(continued)
Cleaner Head Assembly
Disassembly:
It is necessary to disconnect the cleaner from any piping etc. and dismount it from the tank. Place the
machine on a level surface.
1.
Dismount the Clamp ring, Inlet connection and Gasket (Pos. 20, 19 and 21).
2. Push up the Cleaner head (Pos. 17) and remove the Lock ring (Pos. 18). If necessary hold Drive
shaft (Pos. 9) in position when pushing up Cleaner head.
3.
Pull off Cleaner head.
Reassembly:
Reassembly is carried out in the opposite order.
Page 12
Instruction Manual Toftejorg SaniMega
IM-TE91A590-EN1
ï
Return to menu