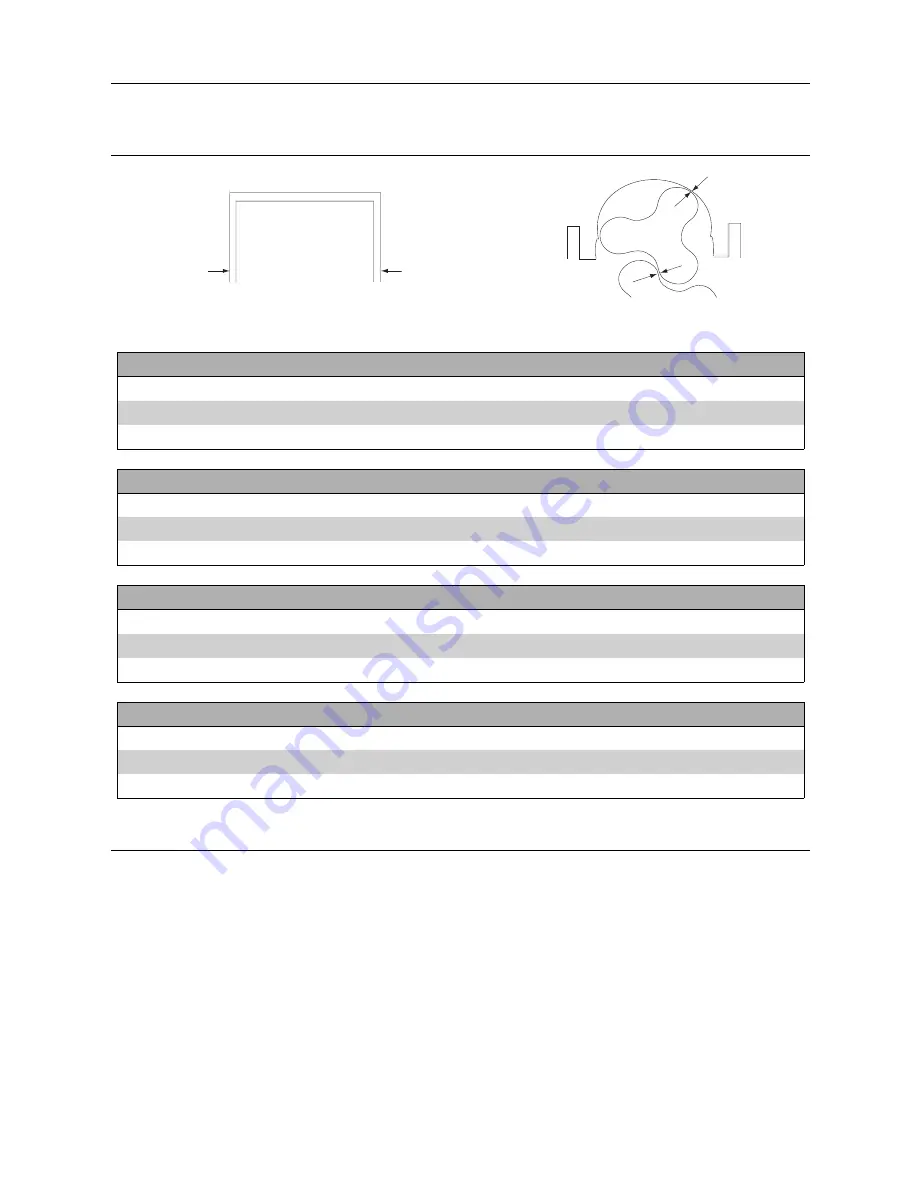
6 Technical data
Radial Clearance
Front Clearance
Rotor Length
Back Clearance
Mesh Clearance
Minimum mesh clearance at any mesh position. All dimensions in millimeters
SRU6/260/LS (HS) TRILOBE and BILOBE ST.STL. ROTORS
10 BAR
Temperature
Rotor
Front
Back
Rotor
Radial
Min. MESH*
o
C
Length
Clearance
Clearance
Diameter
Clearance
TRILOBE
BILOBE 70
o
C
84.34
(min.)
0.25
201.27
(min.)
70
o
C
84.31
0.24
0.20
201.22
0.40
0.30
0.39
84.19
(min.)
0.25
201.13
(min.)
130
o
C
84.16
0.39
0.20
201.08
0.47
0.30
0.39
84.01
(min.)
0.25
200.97
(min.)
200
o
C
83.98
0.57
0.20
200.92
0.55
0.30
0.39
SRU6/260/LD (HD) TRILOBE and BILOBE ST.STL. ROTORS
20 BAR
Temperature
Rotor
Front
Back
Rotor
Radial
Min. MESH*
o
C
Length
Clearance
Clearance
Diameter
Clearance
TRILOBE
BILOBE 70
o
C
84.08
(min.)
0.35
200.67
(min.)
70
o
C
84.05
0.40
0.30
200.62
0.70
0.35
0.80
84.03
(min.)
0.35
200.53
(min.)
130
o
C
84.00
0.45
0.30
200.48
0.77
0.35
0.80
83.97
(min.)
0.35
200.37
(min.)
200
o
C
83.94
0.51
0.30
200.32
0.85
0.35
0.80
SRU6/353/LS (HS) TRILOBE and BILOBE ST.STL. ROTORS
7 BAR
Temperature
Rotor
Front
Back
Rotor
Radial
Min. MESH*
o
C
Length
Clearance
Clearance
Diameter
Clearance
TRILOBE
BILOBE 70
o
C
113.68
(min.)
0.25
201.11
(min.)
70
o
C
113.65
0.40
0.20
201.06
0.48
0.35
0.40
113.50
(min.)
0.25
200.91
(min.)
130
o
C
113.47
0.58
0.20
200.86
0.58
0.35
0.40
113.30
(min.)
0.25
200.67
(min.)
200
o
C
113.27
0.78
0.20
200.62
0.70
0.35
0.40
SRU6/353/LD (HD) TRILOBE and BILOBE ST.STL. ROTORS
15 BAR
Temperature
Rotor
Front
Back
Rotor
Radial
Min. MESH*
o
C
Length
Clearance
Clearance
Diameter
Clearance
TRILOBE
BILOBE 70
o
C
113.23
(min.)
0.45
200.47
(min.)
70
o
C
113.20
0.65
0.40
200.42
0.80
0.40
0.55
113.17
(min.)
0.45
200.27
(min.)
130
o
C
113.14
0.71
0.40
200.22
0.90
0.40
0.55
113.11
(min.)
0.45
200.03
(min.)
200
o
C
113.08
0.77
0.40
199.98
1.02
0.40
0.55
43