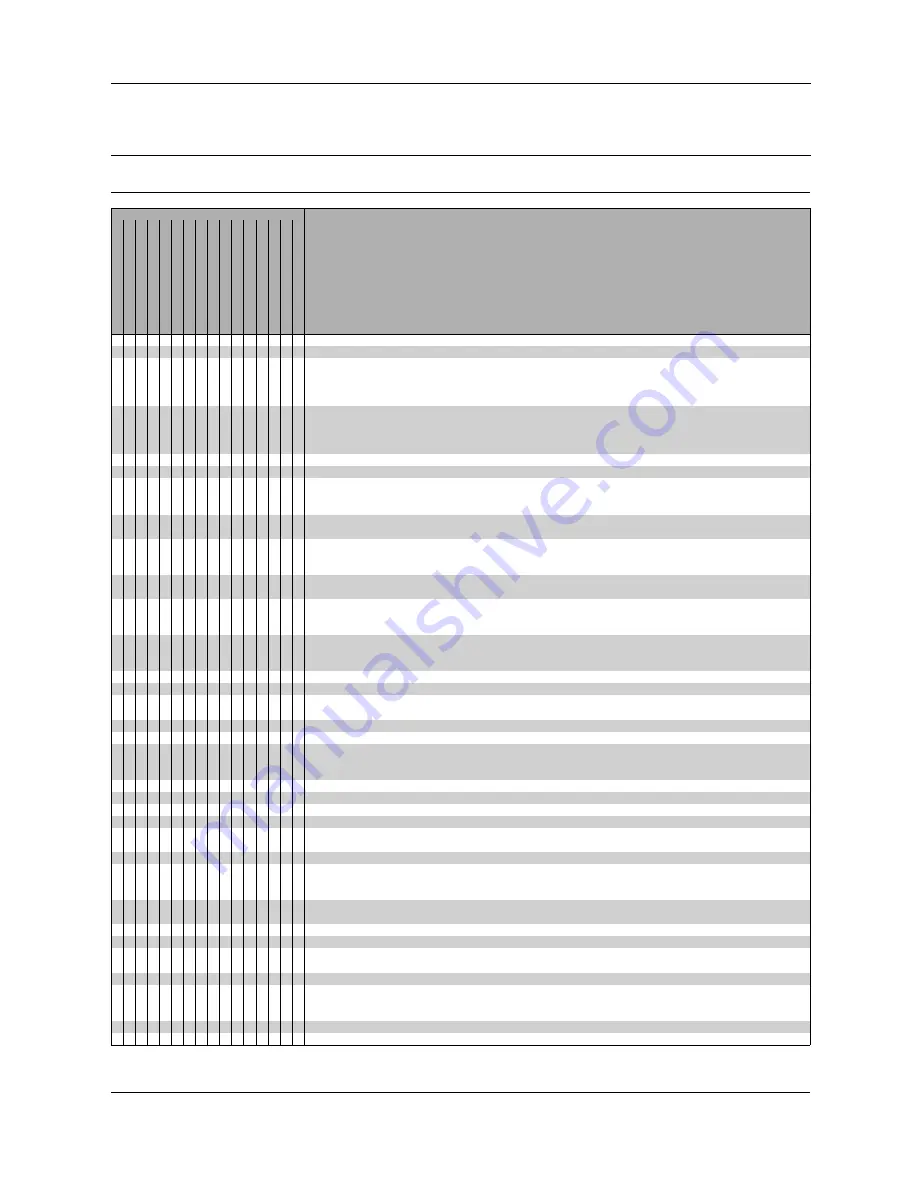
5 Maintenance
5.8
Troubleshooting
Problem
No flo
w
Under capacity
Irr
egular di
s
charge
Lo
w
di
s
charge pr
e
ss
ur
e
Pump
w
ill not prime
Prime lo
s
t after
s
tarting
Pump
s
tall
s
w
hen
s
tarting
Pump overheat
s
Motor overheat
s
E
x
ce
ss
ive po
w
er ab
s
orbed
Noi
s
e and vibration
Pump element
w
ear
S
yphoning
S
eizur
e
Mechanical
s
eal lea
k
age
Mechanical
s
eal lea
k
age
Probable Causes
Solutions
√
√
Incorrect direction of rotation.
Reverse motor.
√
Pump not primed.
Expel gas from suction line and pumping chamber and introduce fluid.
Increase suction line diameter.
Increase suction head.
Simplify suction line configuration and reduce length.
√ √ √ √ √
√
Insufficient NPSH available.
Reduce pump speed.
Increase suction line diameter.
Increase suction head.
Simplify suction line configuration and reduce length.
√ √ √ √
√
Fluid vaporising in suction line.
Reduce pump speed.
√ √ √ √ √
√
Air entering suction line.
Remake pipework joints.
√ √ √ √
√
Strainer or filter blocked.
Service fittings.
Increase fluid temperature.
Decrease pump speed.
√
√ √ √ √ √ √
√
Fluid viscosity above rated figure.
Check seal face viscosity limitations.
Decrease fluid temperature.
√ √ √
Fluid viscosity below rated figure.
Increase pump speed.
Cool the pump casing.
Reduce fluid temperature.
√
√ √
√ √
Fluid temp. above rated figure.
Check seal face and elastomer temp. limitations.
Heat the pump casing.
√ √ √
Fluid temp. below rated figure.
Increase fluid temperature.
Clean the system.
Fit strainer to suction line.
√ √
√ √
Unexpected solids in fluid.
If solids cannot be eliminated, consider fitting double mechanical seals.
Check for obstructions i.e. closed valve.
Service system and change to prevent problem recurring.
√ √ √
√ √ √ √ √ √ √ √ √ √
Discharge pressure above rated figure
Simplify discharge line to decrease pressure.
√ √ √
√
Gland over-tightened
Slacken and re-adjust gland packing.
√ √
√
√
√
Gland under-tightened
Adjust gland packing.
Increase flush flow rate.
√ √
Seal flushing inadequate.
Check that flush fluid flows freely into seal area.
√
√ √ √
Pump speed above rated figure.
Decrease pump speed.
√ √
Pump speed below rated figure.
Increase pump speed.
Check alignment of pipes.
Fit flexible pipes or expansion fittings.
√
√ √ √ √ √ √
Pump casing strained by pipework.
Support pipework.
√
√ √ √
Flexible coupling misaligned.
Check alignment and adjust mountings accordingly.
√ √ √ √ √ √
Insecure pump driver mountings.
Fit lock washers to slack fasteners and re-tighten.
√ √ √ √ √ √ √ √
Shaft bearing wear or failure.
Refer to pump maker for advice and replacement parts.
√ √ √ √ √ √
Insufficient gearcase lubrication.
Refer to pump maker’s instructions.
Check rated and duty pressures.
√ √
√ √ √ √ √ √
Metal to metal contact of pumping element.
Refer to pump maker.
√ √ √
Worn pumping element.
Fit new components.
Check pressure setting and re-adjust if necessary.
Examine and clean seating surfaces.
√ √
√
Rotorcase cover relief valve leakage.
Replace worn parts.
Check for wear on sealing surfaces, guides etc.
√
√
Rotorcase cover relief valve - chatter.
Replace if necessary.
√ √
Rotorcase cover relief valve incorrectly set.
Re-adjust spring compression - valve should lift approx. 10% above duty pressure.
√
√
Suction lift too high.
Lower pump or raise liquid level.
Fluid pumped not compatible with
√ √
materials used.
Use optional materials.
√
No barrier in system to prevent flow passing.
Ensure discharge pipework higher than suction tank.
Ensure system operation prevents this.
Fit single or double flushed mechanical seals.
√ √
Pump allowed to run dry.
Fit flushed packed gland.
√ √
Faulty motor.
Check and replace motor bearings.
√
Pumping element missing
Fit pumping element.
36