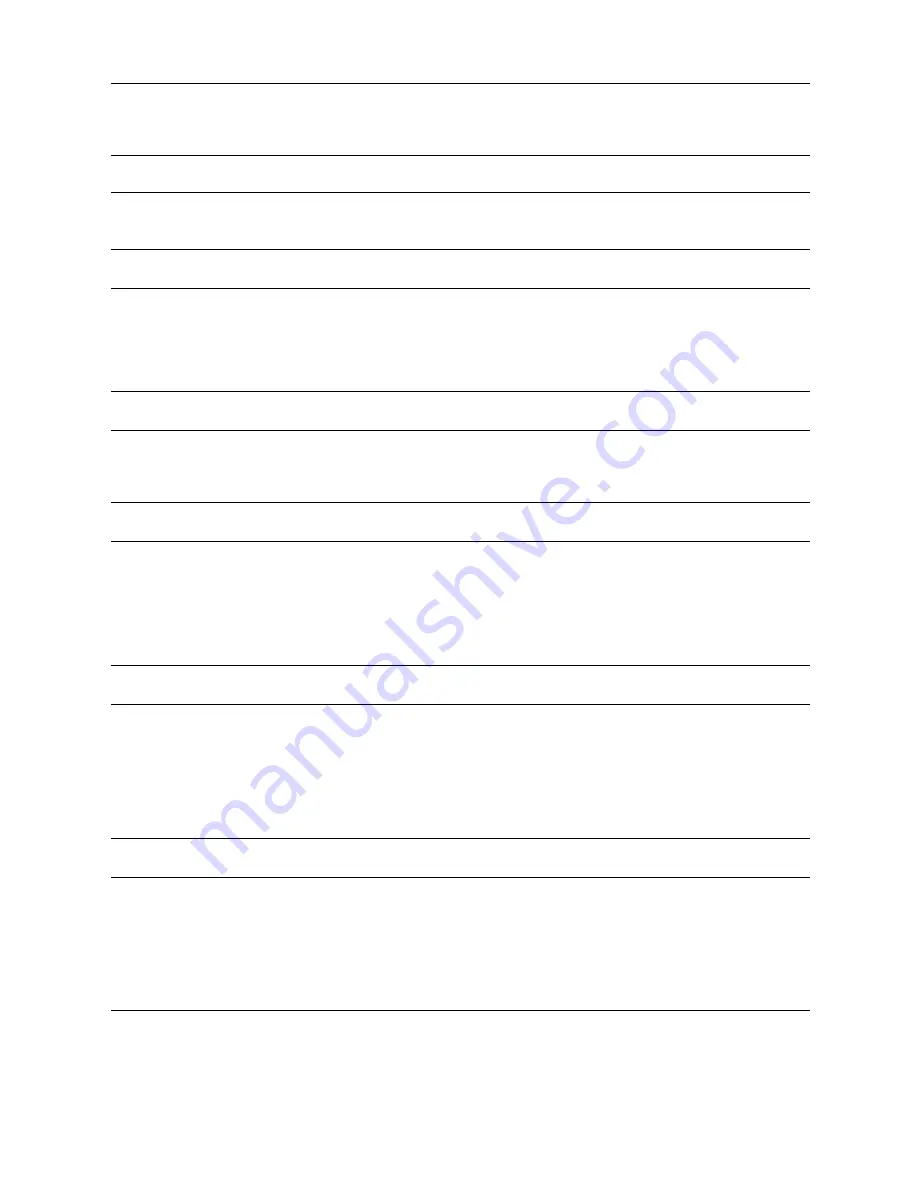
4 Maintenance
4.1
Inspection
At regular intervals and as frequently as experience indicates, an examination should be made of the interior and exterior
condition of the unit. Failure to keep all tubes clean may result in decreased performance of the heat exchanger.
4.2
Indication of fouling
Heat exchangers subject to fouling or scaling should be cleaned periodically. A light sludge or scale coating on the tube greatly
reduces its thermal efficiency. An increase in pressure drop and/or reduction in performance usually indicates that cleaning is
necessary. The unit should first be checked for air or vapour binding to confirm that this is not the cause for the reduction in
performance. Since the difficulty of cleaning increases rapidly as the scale thickness or deposit increases, the intervals between
cleaning should not be excessive.
4.3
Disassembly for inspection or cleaning
Before disassembly, the user must ensure that the unit has been depressurised, vented and drained.
To inspect the inside of the tubes and also make them accessible for cleaning, remove the front head cover.
Always replace the gasket when the front cover is loosened to make sure that the gasket seals correctly.
4.4
Locating leaks
The heat exchanger has double tube sheets and a leakage in the joint in the inner tube sheet will show as a leakage between the
double tube sheets. A leakage in the joint in the outer tube plate will also show as a leakage between the double tube sheets.
The following procedure may be used to locate perforated or split tubes inside the shell.
- Remove the front head cover and apply pressure in the shell. Any leakage coming out of any tube shows a leakage in a
tube inside the shell.
4.5
Cleaning the heat exchanger
The heat transfer surfaces of the heat exchanger must be clean to ensure satisfactory performance.
The method selected is the choice of the operator and will depend on the type of deposit and the facilities available in the plant.
Cleaning compounds must be compatible with the metallurgy of the heat exchanger.
Caution! If necessary, use proper protective equipment, such as safety boots, safety gloves and eye protection, when using
the cleaning agents.
4.6
Gasket replacement
Remove the front head cover to replace the gasket.
Tighten the bolts after replacement of the gasket.
It is important that bolts are tightened uniformly and in a diametrically staggered pattern, see section 3 Operation.
The bolts should first be tightened to 15 Nm (for all bolts) then tightened to 30 Nm. Then tighten the bolts to 50 Nm and
finally torque the bolts with full torque (70 Nm).
13
www.sks-online.com
www.sks-webshop.com