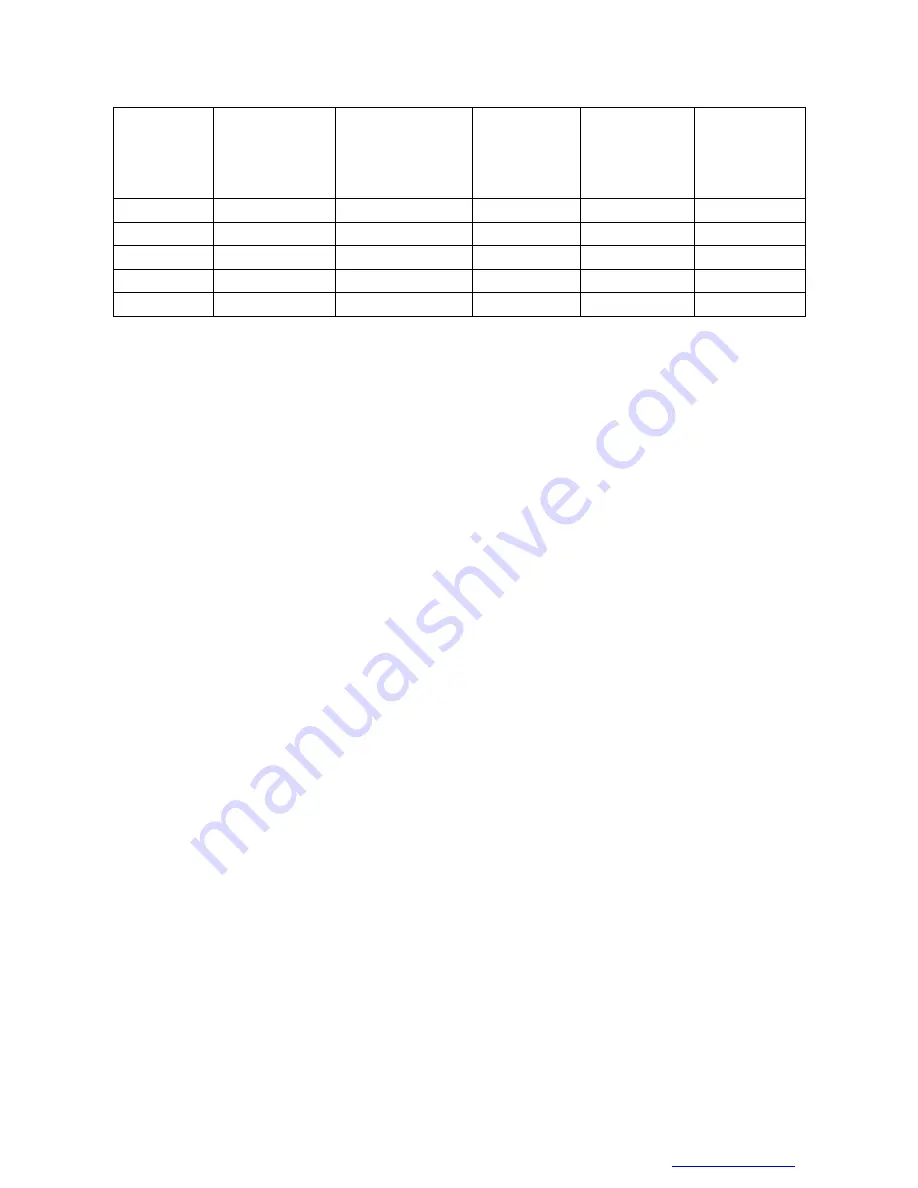
10/12
ALFA IN a.s. ©
www.alfain.eu
Basic settings for TIG welding – stainless steel, DC current
Material
thickness
mm
Tungsten
electrode
diameter
mm
Filler material
diameter mm
Welding
current
A
Argon flow
l/min
Gas
nozzle mm
1
1
1,5
40-60
3
10
1,5
1,5
1,5
50-90
4
10
2
2
2
80-100
4
12
3
2-3
2-3
90-140
5
12
4-5
3-4
3-4
110-180
5
12
7. ROUTINE MAINTENANCE & INSPECTION
1. The only routine maintenance required for the PEGAS range of machines
is a thorough cleaning and inspection, with the frequency depending on
the usage and the operating environment.
2.
WARNING
Disconnect the PEGAS from the mains supply voltage before
disassembling.
3. Special maintenance is not necessary for the control unit parts in the
Welder. If these parts are damaged for any reason, replacement is
recommended.
4.
CAUTION
Do not blow air into the welder during cleaning. Blowing air into the welder
can cause metal particles to interfere with sensitive electronic components
and cause damage to the welder.
5. To clean the welder, disconnect it from the mains supply voltage then open
the enclosure and use a vacuum cleaner to remove any accumulated dirt
and dust. The welder should also be wiped clean. If necessary, solvents
that are recommended for cleaning electrical apparatus may be used.
6. Troubleshooting and repairing of PEGAS welding equipment should only
be carried out only by suitably qualified or competent person.
7. A ‘competent person’ must be a person who has acquired through training,
qualification or experience, or a combination of them, the knowledge and
skills enabling that person to safely carry out a risk assessment and repairs
to the electrical equipment in question.
8. The person carrying out the servicing needs and repairs must know what
to look at, what to look for and what to do.