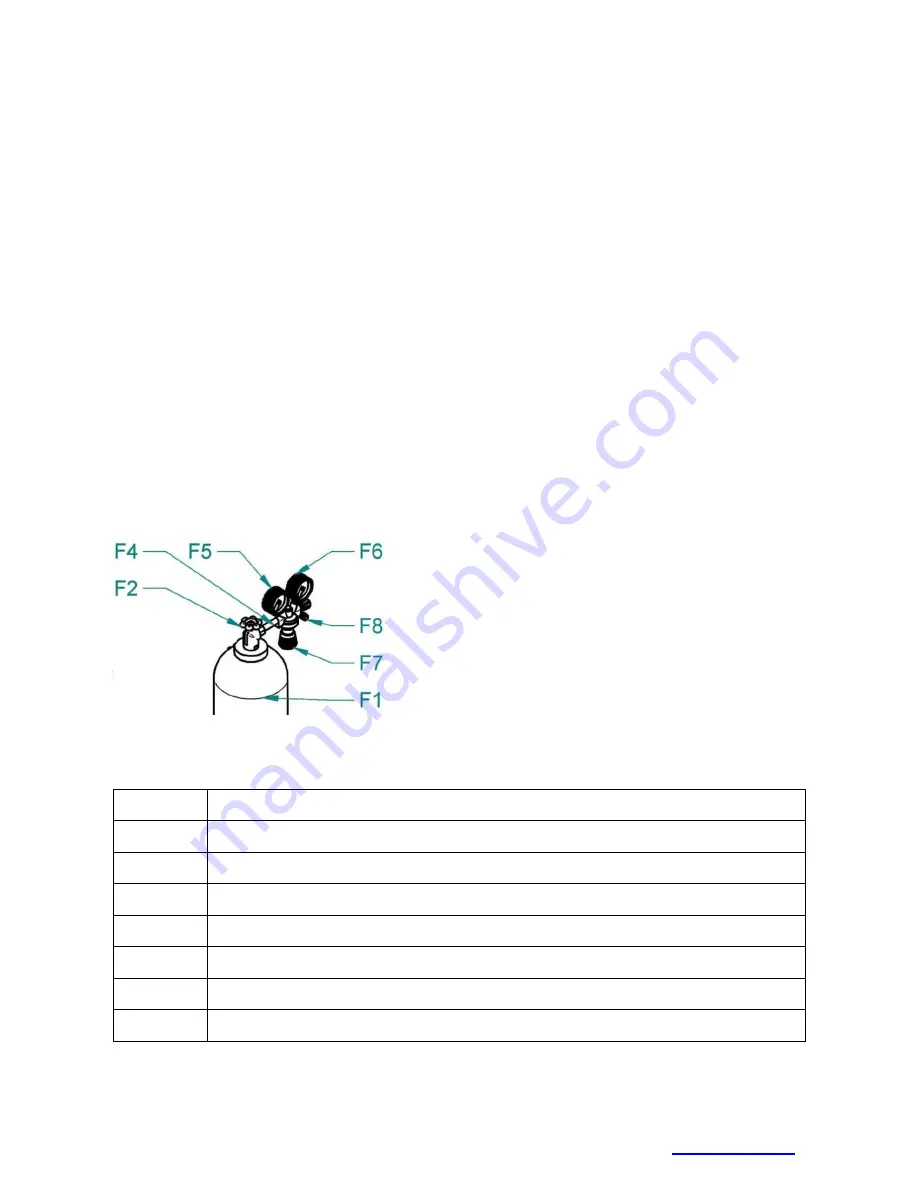
16/24
ALFA IN a.s. ©
www.alfain.eu
nozzle and gas nozzle on.
12.
Before welding, spray the area in a gas hose and current nozzle with
a separation spray, to prevent damage.
ADJUSTMENT OF GAS FLOW
The electric arc and the weld must be perfectly shielded by gas. Too small
amount of gas does not perform the protective atmosphere and on the other
hand to big amount of the gas brings air into the electric arc.
Notice
Gas bottle must be well secured against fall. This manual does
not solve the safe securing of gas bottle. Information can be obtained from a
supplier of industrial gases.
1. Connect the gas hose to gas outlet
F8
on the valve and the gas inlet to
the gas valve
A8
.
2. Press the button
38
in the space of the wire feeder.
3. Turn the adjusting screw
F7
at the bottom side pressure reducing valve,
until the meter
F6
shows the required flow, then release the button. The
optimum flow is 10-15l/min.
4. After long-term shutdown of the machine or replacement of the torch it is
suitable to blow the pipes with protective gas before welding.
Fig. 7. Gas flow setting
Pos.
Description
F1
Gas bottle
F2
Cylinder Valve
F4
Pressure Reducer
F5
High Pressure Manometer
F6
Low Pressure Manometer
F7
Adjusting Screw
F8
Gas outlet