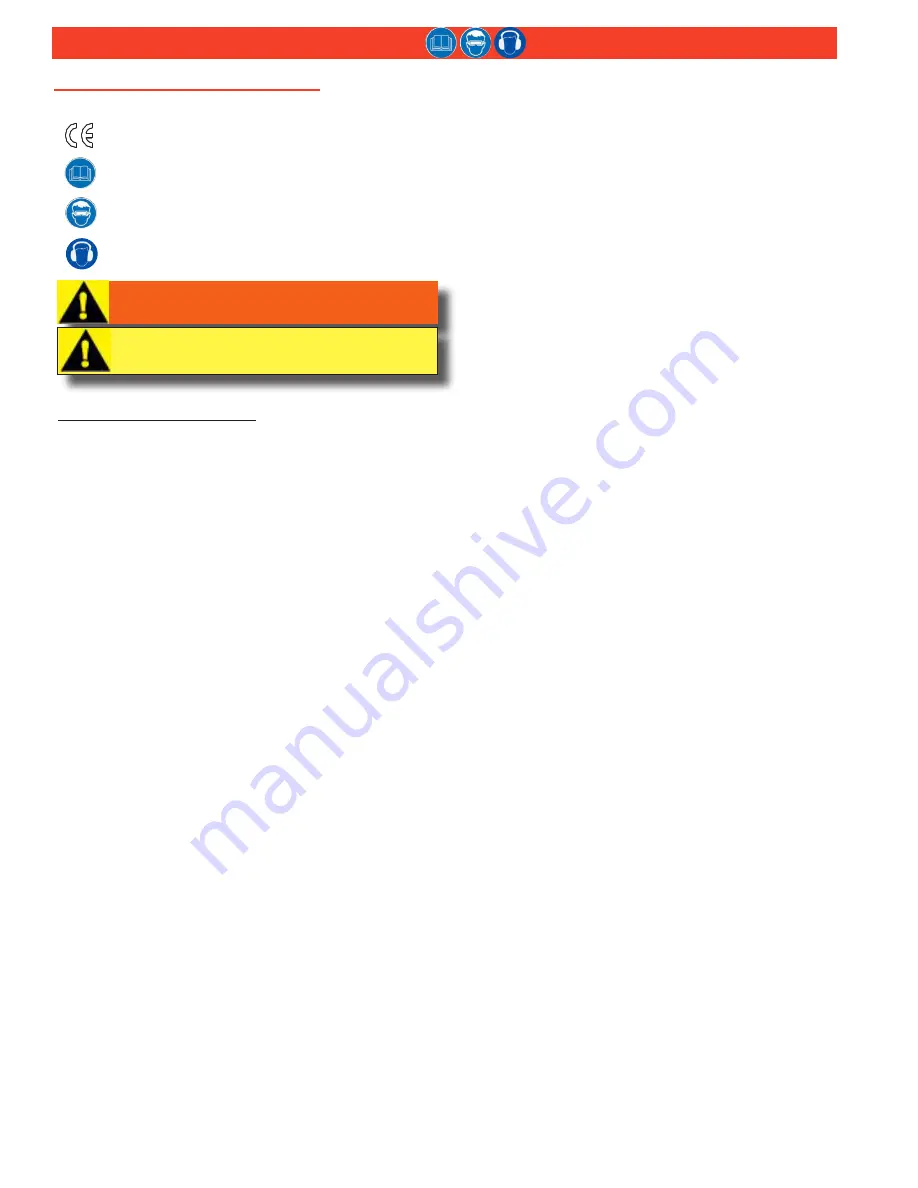
4
B4600 Battery-Powered Tool (
HK1189
) Alcoa Fastening Systems & Rings
s
afety
I
nstruCtIons
I. GENERAL SAFETY RULES:
1. A half hour long hands-on training session with
qualified personnel is recommended before using Huck
equipment.
2. Huck equipment must be maintained in a safe working
condition at all times. Tools and hoses should be
inspected at the beginning of each shift/day for damage
or wear. Any repair should be done by a qualified
repairman trained on Huck procedures.
3. For multiple hazards, read and understand the safety
instructions before installing, operating, repairing,
maintaining, changing accessories on, or working near
the assembly power tool. Failure to do so can result in
serious bodily injury.
4. Only qualified and trained operators should install,
adjust or use the assembly power tool.
5. Do not modify this assembly power tool. This can reduce
effectiveness of safety measures and increase operator
risk.
6. Do not discard safety instructions; give them to the
operator.
7. Do not use assembly power tool if it has been damaged.
8. Tools shall be inspected periodically to verify all ratings
and markings required, and listed in the manual, are
legibly marked on the tool. The employer/operator
shall contact the manufacturer to obtain replacement
marking labels when necessary. Refer to assembly
drawing and parts list for replacement.
9. Tool is only to be used as stated in this manual. Any
other use is prohibited.
10. Only genuine Huck parts shall be used for replacements
or spares. Use of any other parts can result in tooling
damage or personal injury.
11. Never remove any safety guards or pintail deflectors.
12. Check clearance between trigger and work piece to
ensure there is no pinch point when tool is activated.
Remote triggers are available for hydraulic tooling if
pinch point is unavoidable.
13. Do not abuse tool by dropping or using it as a hammer.
Never use hydraulic or air lines as a handle or to bend
or pry the tool. Reasonable care of installation tools by
operators is an important factor in maintaining tool
efficiency, eliminating downtime, and preventing an
accident which may cause severe personal injury.
14. Never place hands between assembly power tool and
work piece. Keep hands clear from front of tool.
II. PROJECTILE HAZARDS:
1. Disconnect the assembly power tool from energy source
when changing inserted tools or accessories.
2. Be aware that failure of the workpiece, accessories,
or the inserted tool itself can generate high velocity
projectiles.
3. Always wear impact resistant eye protection during tool
operation. The grade of protection required should be
assessed for each use.
4. For overhead work, wear a safety helmet.
5. Ensure that the workpiece is securely fixed.
6. The risk to others should also be assessed at this time.
7. Be aware of the risk of being exposed to the ejection of
cuttings or chips.
8. Be aware that working on brittle material can cause
harmful splinters.
III. OPERATING HAZARDS:
1. Use of tool can expose the operator’s hands to hazards
including: crushing, impacts, cuts, abrasions and heat.
Wear suitable gloves to protect hands.
2. Operators and maintenance personnel shall be physically
able to handle the bulk, weight and power of the tool.
3. Hold the tool correctly and be ready to counteract
normal or sudden movements with both hands
available.
4. Maintain a balanced body position and secure footing.
5. Release trigger or stop start device in case of
interruption of energy supply.
6. Use only fluids and lubricants recommended by the
manufacturer.
7. Avoid direct contact with the inserted tool as it can
become hot.
8. Sharp tools shall always be used.
9. Be aware of risk of whipping compressed air hose.
10. Be aware of risk of cutting with tools with large
dimensions.
IV. REPETITIVE MOTION HAZARDS:
1. When using assembly power tool, the operator can
experience discomfort in the hands, arms, shoulders,
neck or other parts of the body.
2. When using tool, the operator should adopt a
comfortable posture while maintaining a secure footing
and avoid awkward or off balanced postures.
continued
GLOSSARY OF TERMS AND SYMBOLS:
- Product complies with requirements set forth by
the relevant European directives.
-
READ MANUAL
prior to using this equipment.
-
EYE PROTECTION IS REQUIRED
while using this
equipment.
-
HEARING PROTECTION IS REQUIRED
while
using this equipment.
Notes: are reminders of required procedures.
Bold, Italic type, and underline
:
emphasize a specific
instruction.
WARNINGS: Must be understood to avoid
severe personal injury.
CAUTIONS: show conditions that will
damage equipment and or structure.