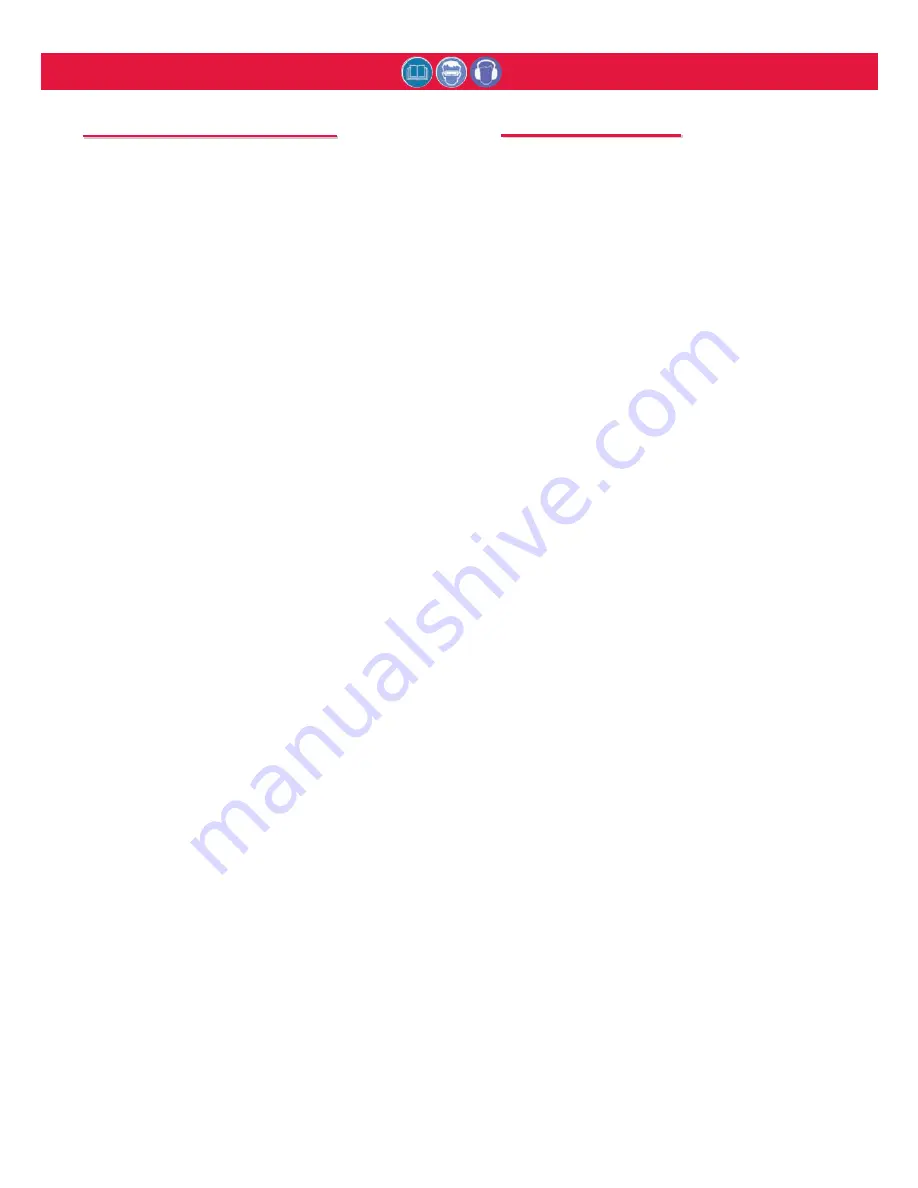
2025 series Tooling
(HK1006)
Alcoa Fastening Systems
20
Always check out the simplest possible cause of a
malfunction first. For example, an air hose not
connected. Then proceed logically, eliminating each
possible cause until the cause is located. Where
possible, substitute known good parts for suspected
bad parts. Use TROUBLESHOOTING CHART as an
aid in locating and correcting malfunction.
1. Tool fails to operate when trigger is
depressed
a) Air line not connected
b) Throttle Valve O-rings (50) worn or damaged.
c) Throttle Valve Cable (2) is broken.
2. Tool does not complete fastener installation
and break pintail
a) Air pressure too low
b) Air Piston Quad-ring (47) worn or damaged.
c) Tool is low on hydraulic fluid, refer to Fill and
Bleed section.
d) Air in hydraulic system, refer to Fill and Bleed
section.
3. Pintail stripped and/or swaged collar not
ejected
a) Check for broken or worn jaws in nose
assembly, refer to nose assembly data sheet.
b) Check for worn anvil, refer to nose data sheet.
4. Hydraulic fluid exhausts with air or leaks at
base of handle
a) Worn or damaged Gland Assembly (25).
Inspect Polyseal (28), O-rings (31 and 27),
Quad-ring (33) and Back-up ring (32). Replace
if necessary.
5. Hydraulic fluid leaks at rear of Pull Piston (6)
a) Worn or damaged piston Polyseal (18),
replace if necessary.
6. Hydraulic fluid leaks at front of Pull Piston (6)
a) Worn or damaged Front Gland (15), inspect
Polyseal (14), O-ring (12) and Back-up Ring
(11). Replace if necessary.
7. Pull Piston (6) will not return
a) Throttle Valve (52) stuck: Lubricate O-rings
(50).
b) Throttle Arm (53), Cable (2) or Trigger (5)
binding.
8. Air leaks at air Cylinder Head (45)
a) Worn or damaged O-ring (46) replace if
necessary.
Fill and Bleed Bottle
(Fig. 9)
- 120337
Stall Nut
(2025, 2025B, 2025S & 2025V)
- 124090
Stall Nut
(2025L, 2025LB, 2025SL & 2025LV)
- 125340
2025, 2025B, 2025S & 2025V
Assembly Tool Kit
- 123110-6
Includes: (Fig. 3)
Piston Assembly (Bullet)
- 123111-2
Spacer
- 123112-2
POLYSEAL Tool
- 121694-2025
2025L, 2025LB, 2025SL & 2025LV
Assembly Tool Kit
- 123110-8
Includes: (Fig. 3)
Piston Assembly (Bullet)
- 123111-4
Spacer
- 123112-3
POLYSEAL Tool
- 121694-2025
Conversion Kit
- 126190
(To convert 2025L to 2025LV)
Includes:
Pintail Collection Bottle
- 123772
Tubing and Slide Assembly
- 124245
Piston Assembly
- 125738-3
End Cap Assembly
- 125863
Conversion Kit
- 126432
(To convert 2025 to 2025V)
Includes:
Pintail Collection Bottle
- 123772
Tubing & Slide Assy
- 124245
Piston Assy
- 125738-2
End Cap Assembly
- 125863
Vacuum Attach Adapter
- 123784
Retaining Ring Ext
- 501007
Flat Washer
- 506628
Straight Connector
- 506675
Service Kit
(2025, 2025B, 2025L,
- 2025KIT
2025S, 2025SL &
2025LB)
Service Kit
(2025LV & 2025V)
- 2025VKIT
T
T
ROUBLESHOOTING
ROUBLESHOOTING
A
A
CCESSORIES
CCESSORIES