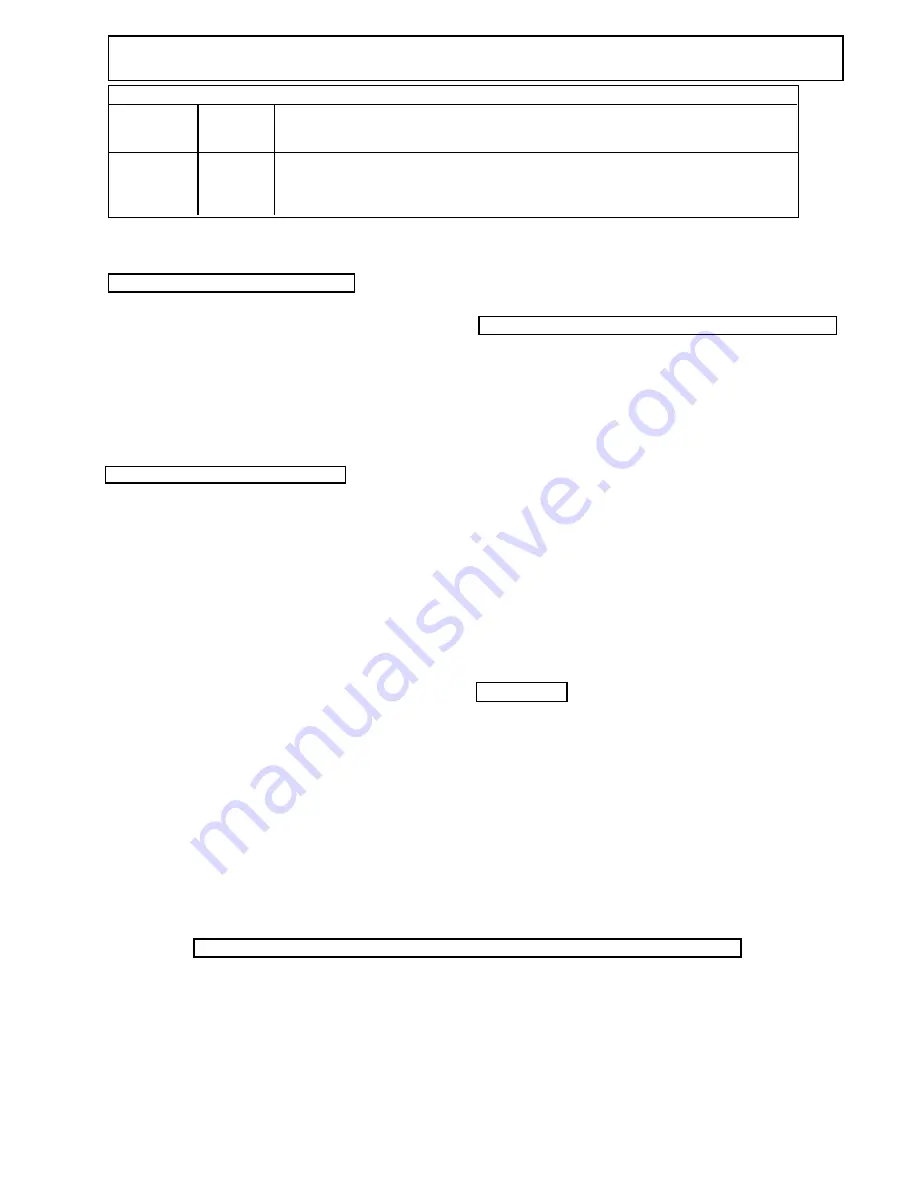
7
UL RECOMMENDATION FOR MINIMUM GAUGE EXTENSION CORD
AMPERAGE
RATING
RANGE
5 - 6
6 - 8
8 - 10
10 - 12
VOLTAGE
120
120
120
120
500
Always follow recommended pressure and operating
instructions.
KEEP CLEAR OF MOVING PARTS
Keep clear of moving parts when starting or operating
the sprayer. Do not put your iginfers into any openings
to avoid amputation by moving parts or burns on hot parts.
Precaution is the best insurance against an acci-
dent. When starting the motor, maintain a safe
distance from moving parts of the equipment.
Before adjusting or servicing any mechanical part of
the sprayer, follow the PRESSURE RELIEF PROCE-
DURE on page 6.
AVOID COMPONENT RUPTURE
This sprayer operates at 3000 psi (205 bar). Always
be sure that all components and accessories have a
maximum working pressure of at least 3000 psi to avoid
rupture which can result in serious bodily injury includ-
ing injection and property damage.
NEVER leave a pressurized sprayer unattended to avoid
accidental operation of it which could result in serious
bodily injury.
ALWAYS follow the PRESSURE RELIEF PROCEDURE
whenever you stop spraying and before adjusting, re-
moving or repairing any part of the sprayer.
NEVER alter or modify any part of the equipment to
avoid possible component rupture which could result in
serious bodily injury and property damage.
NEVER use weak or damaged or non-conductive paint
hose. Do not allow kinking or crushing of hoses or allow
it to vibrate against rough or sharp or hot surfaces.
Before each use, check hoses for damage and wear
and ensure all fluid connections are secure.
REPLACE any damaged hose. NEVER use tape or any
device to mend the hose.
NEVER attempt to stop any leakage in the line or fit-
tings with your hand or any part of the body. Turn off
the unit and release pressure by following PRESSURE
RELIEF PROCEDURE,
ALWAYS use approved high pressure fittings and re-
placement parts.
ALWAYS ensure fire extinquishing equipment is readily
available and properly maintained.
PREVENT STATIC SPARKING FIRE/EXPLOSIONS
ALWAYS be sure all equipment & objects being sprayed
are properly grounded. Always ground sprayer, paint
bucket and object being sprayed. See grounding on
page 6 for grounding information.
Vapors created when spraying can be ignited by sparks.
To reduce the risk of fire, always locate the sprayer at
least 20 feet (6 m.) away from spray area. Do not plug
in or unplug any electrical cords in the spray area, which
can create sparks, when there is any chance of ignit-
ing vapors still in the air. Follow the coating & solvent
manufacturers safety warnings and precautions.
Use only conductive fluid hoses for airless applications.
Be sure gun is grounded through hose connections.
check ground continuity in hose & equipment. Overall
(end to end) resistance of unpressurized hose must not
exceed 29 megohms for any coupled length or combi-
nation of hose length. Use only high pressure airless
hoses with static wire approved for 3000 psi.
FLUSHING
Reduce the risk of injection injury, static sparking or
splashing by following the specific cleaning process.
ALWAYS follow the PRESSURE RELIEF PROCEDURE
on page 6.
ALWAYS remove the spray tip before flushing. Hold a
metal part of the gun firmly to the side of a metal pail
and use the lowest possible fluid pressure during flush-
ing.
NEVER use cleaning solvents with flash points below
140 degrees F. Some of these are: acetone, benzene,
ether, gasoline, naptha. Consult your supplier to be sure.
NEVER SMOKE in the spraying/cleaning area.
WHEN SPRAYING & CLEANING WITH FLAMMABLE PAINTS AND THINNERS
1. When spraying with flammable liquids, the unit must be located a minimum of 25 feet away from the spraying
area in a well ventilated area. Ventilation must be sufficient enough to prevent the accumulation of vapors.
2. To eliminate electrostatic discharge, ground the spray unit, paint bucket & spraying object. See GROUNDING
on pg. 6. Use only high pressure airless hoses approved for 3000 psi which is conductive.
3. Remove spray tip before cleaning gun and hose. Make contact of gun with bucket and spray without the tip in
a well ventilated area, into the grounded steel bucket.
4. Never use high pressure in the cleaning process. USE MINIMUM PRESSURE.
5. Do not smoke in spraying/cleaning area.
50
100
150
250
200
25
18
18
18
16
16
16
14
14
12
10
10
8
10
10
8
8
10
8
8
6
300
8
6
6
6
400
8
6
6
4
6
6
4
4
12
12
12
10
WARNINGS