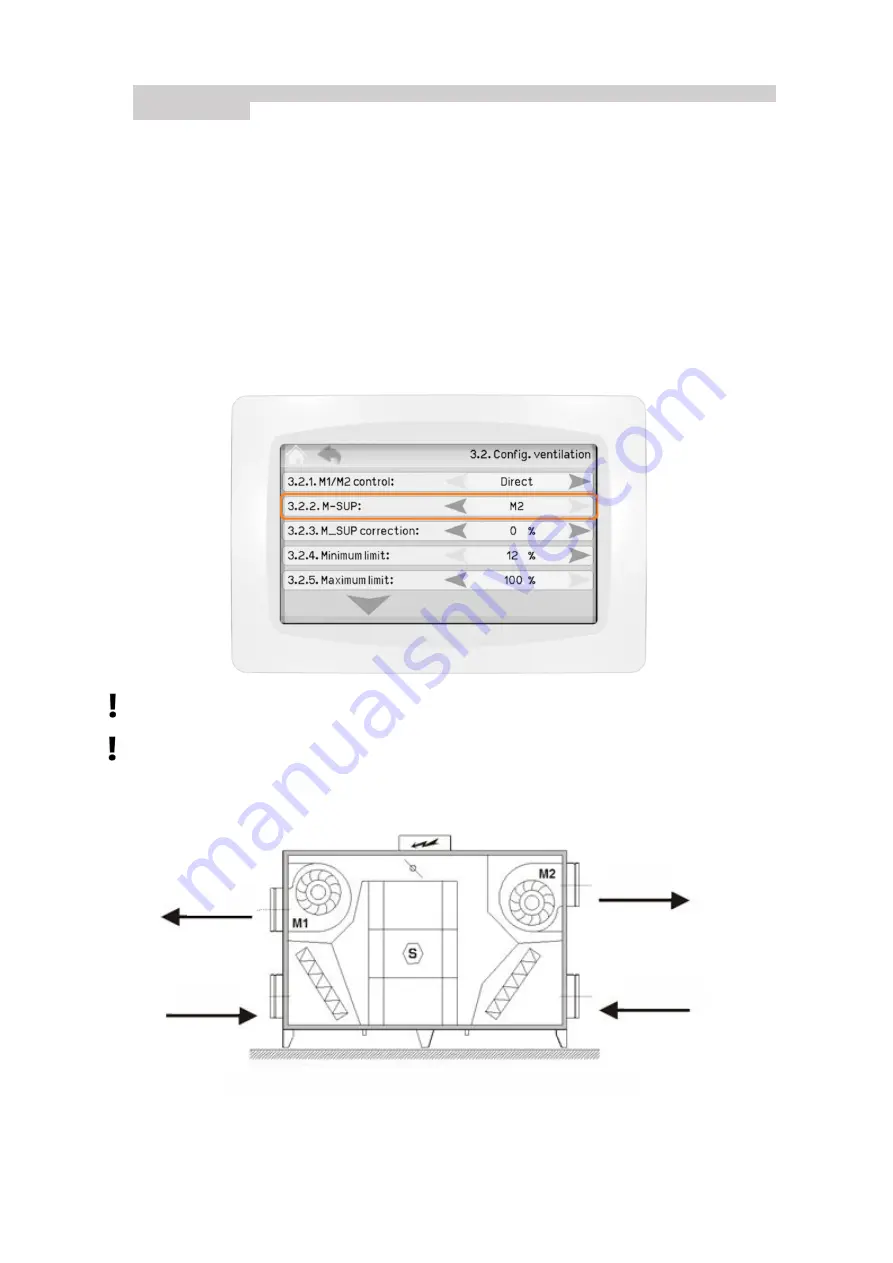
8
of the HVAC network ensures positive pressure in the supply section of the appliance against the
extraction section
5.3. Configuring orientation of the unit
The versatile design of sizes 650, 1100, 1600, 2600 and 3600 allows adjusting the direction of air flow
through the appliance; it can be configured which of the fans will be supplying and extracting the air.
The direction of air flow can be configured once the unit is switched ON for the first time.
1. Open the door of the unit. Check the labels on the fans to learn which fan is marked M1 and M2.
2. Connect the control panel CP Touch to the unit. Turn the unit ON. The control panel will report an
error by showing a yellow triangle on the top of the display.
3. Click on the symbol of the error. The control panel will display the message
Orientation is not set
.
4. Proceed back to the default screen, click on the cogwheel in the bottom left corner.
5. Click on the Settings symbol in the top right corner.
6. Enter the service menu password. The password is available to authorized partners.
7. Proceed to the parameter 3.2.2 on the control panel. Set up the fan M1 or M2 as M-SUP (supply
fan).
The operation of the unit is blocked until the parameter M
SUP
is configured to M1 or M2.
By default, the unit is equipped with filters of different filtration classes. Make sure the filters are
placed correctly according to the orientation of the unit. For more information see Chapter 5.9.
e1 (ODA)
e2 (SUP)
i1 (ETA)
i2 (EHA)
DUPLEX
VENT
Flexi unit where M1 is set as supply fan (M-SUP)