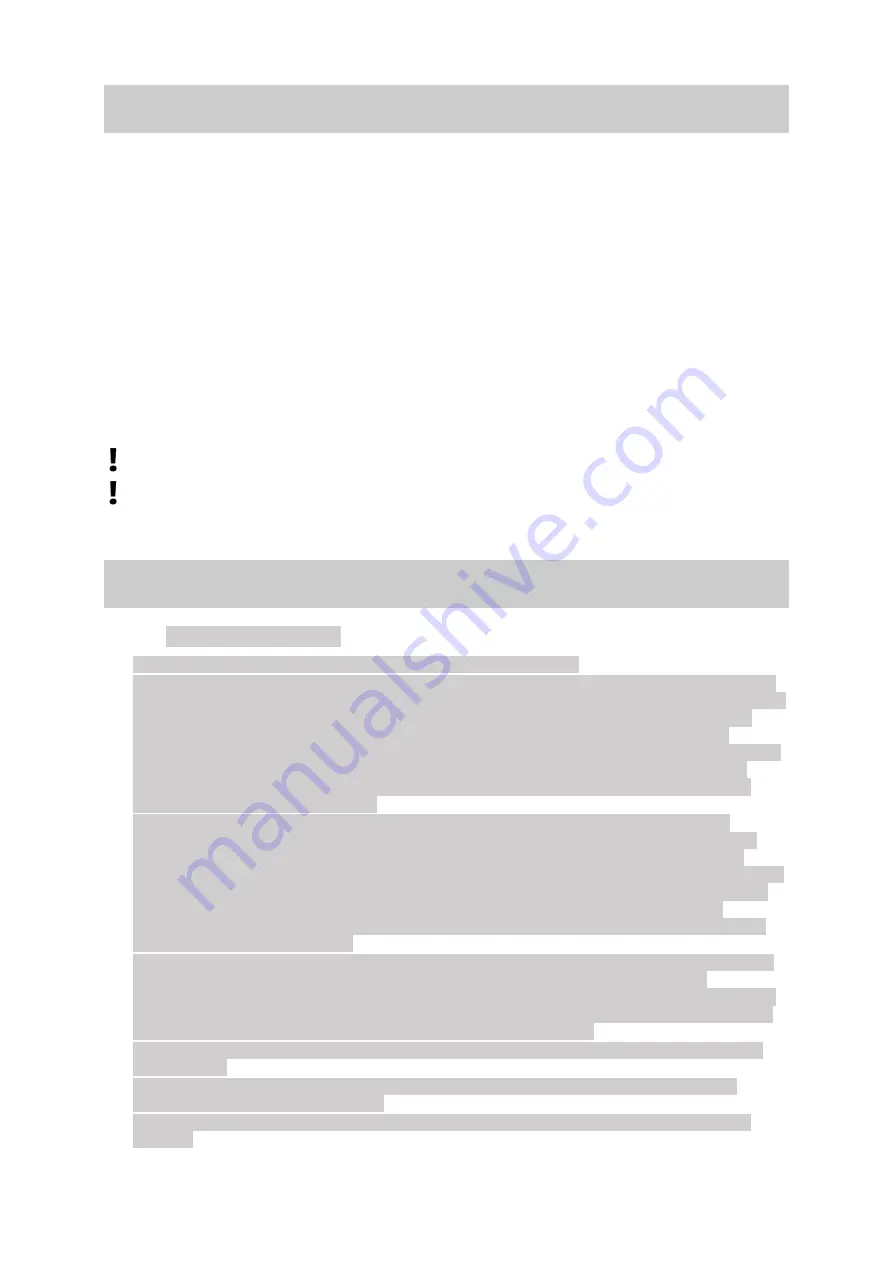
17
6 . E l e c t r i c a l c o n n e c t i o n , c o m m i s s i o n i n g ,
d e s c r i p t i o n o f c o n t r o l s
The electrical equipment of the unit is designed following standards in effect for electrical
connections to power supply network TN-C, TN-S, TN-C,S. The appliance may only be connected
by a qualified electrician. The appliance is provided with external connections for equipotential
bonding.
The wiring diagram of the equipment is shown in the appendix that forms an integral part of this
set of documentation. Instructions for and the diagrams of electrical connections of optional
accessories are included in the documentation sets of these accessories.
The power supply line to the equipment must be provided with a disconnecting device - a service
switch for disconnecting from power supply - whose opening contacts are at least 3 mm apart at
all poles. This disconnecting device must be installed within an appropriate distance from the
appliance. The protection device included as a standard with delivery may act as such a
disconnecting device provided that the switchboard is located within reach of the appliance.
Commissioning may vary depending on the type of control system. Commissioning is carried out
by a trained technician following the separate documentation set included.
The controls are described in the separate document titled “Operating the control system”.
The unit is to be protected using a breaker with characteristics "
C
".
In case of using additional overcurrent protection against accidental direct or indirect contact, it is
necessary to use a
special
circuit breaker designed for frequency inverters and switching
sources. It is a protector sensitive to alternating pulsed DC
residual currents, resistant to current
surges 5 kA.
7 . H y g i e n i c i n s t r u c t i o n s f o r c o m p l i a n c e w i t h V D I
6 0 2 2
7.1. General instructions
Basic hygiene-related requirements are outlined in the Chapter 5.2.
The appliance has been manufactured in a hygienic design that complies with all requirements of
the VDI 6022 standard for the hygiene o HVAC device. In order to meet those requirements during
operation it is essential to ensure for the appliance to be operated, maintained, inspected and
cleaned by sufficiently qualified personnel in accordance with instructions contained in the
operation and maintenance manual. It is also essential to ensure for the remaining components of
the HVAC system (HVAC distribution systems, distribution elements, ancillary devices, noise
silencers etc.) to meet all hygienic requirements of the VDI 6022 standard and be operated in
compliance with those requirements.
If long-term high relative humidity (short-term more than 90 % or more than 80 % for three
consecutive days) is likely to occur with the subsequent moistening of filters (e.g. in areas with
frequent fogs, frequent and long rains, flying snow etc.), suitable measures must be taken to
prevent microbiologic growth. Recommended measures include more frequent hygienic checks as
per VDI 6022 or shorter filter replacement intervals. Another option is the preheating of air using
an appropriate control devices (electrical duct heaters are an available accessory), or the
appliance must be put out of operation for the period when filters are at the risk of moistening (if
the type of operation allows this).
Air duct including accessories with autonomous regulation of operation is to be connected on the
fresh air supply. Such duct will, in compliance with the regulation VDI 6022, provide for
appropriate treatment of supplied fresh air to prevent air filter from getting wet. In case the duct is
not connected or if it does not include such accessory, the appliance is to be put out of operation
as long as the risk of air filters to get wet persists (thick fog, snowing).
Operators must be familiar with the tasks and functions as well as the individual components of
the appliance.
The appliance must be regularly inspected, cleaned and maintained by sufficiently qualified
personnel (see the following chapter).
Regardless of their qualifications, personnel must undergo hygiene training (see the following
chapter).