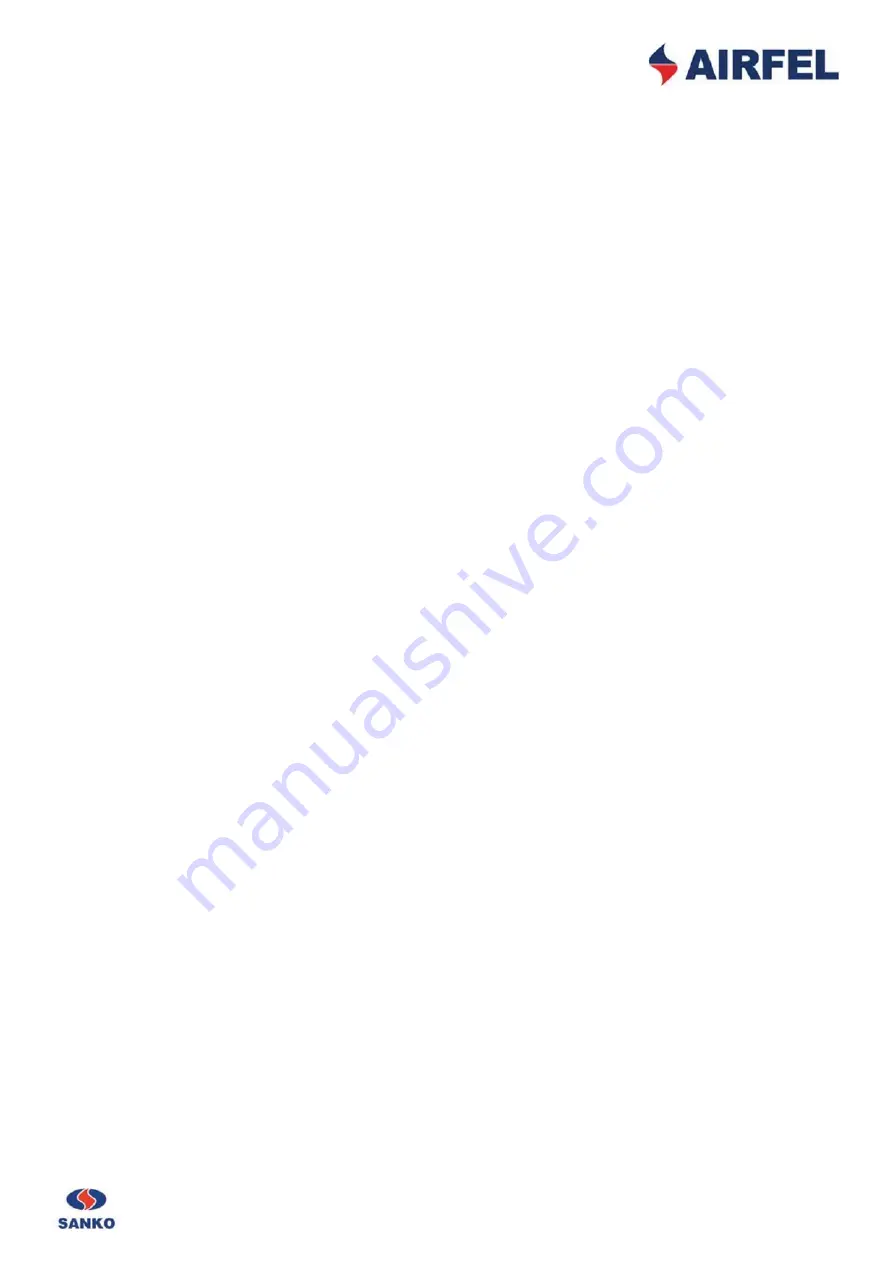
ECOFEL BOILER SERVICE MANUAL
4. Safety
Measures:
4.1 Flue Kit Safety System:
It is controlled by the differential pressure switch (pressure switch).
4.2 Pump
Anti-blockage system:
In case the boiler is not operated for a long time, to prevent jamming of the circulation pump it is activated every 24
hours for 30 seconds. For this function to operate, the incoming power must be on even if the boiler is turned off.
4.3 Overheating safety system:
It is controlled by the limit thermostat. Limit thermostat shuts down the boiler when water temperature at main heat
exchanger outlet reaches 105ºC (±4ºC). When the water temperature cools down to 80ºC ± 12ºC, boiler should be
reset for restarting.
4.4 Waterless Operation Safety System:
It is a safety system preventing waterless operation of the boiler when the closed circuit water pressure on the
hydraulic block falls below 0.8 bars.
4.5 Ionization Flame Control:
The burner cuts off the gas automatically when there is no flame on its surface or the flame goes out due to any reason
and the user is warned via the failure code.
4.6 Safety Valve (3 bars):
Protects the heater system and boiler against probable high pressure.
4.7 Automatic
Air Purger:
Provides the discharge of the air in heater system and prevents air compression within the system.
4.8 Frost Safety System:
It is developed for preventing the heater system and boiler against freezing. It is controlled by the sensor located at
the main heat exchanger outlet. When the water temperature falls to +8ºC, only the circulation pump and burner are
activated and turned off after raising the water in the heater circuit to 36ºC. For this function to operate, the incoming
power and gas must be on even if the boiler is turned off.
4.9 Low Voltage Safety System:
In case of low voltage supply from the network, the boiler continues to operate safely up to 186 Volts.
4.10 Automatic Bypass System:
By creating a short circuit between the heater stream and return piping, the boiler is prevented against damage.
4.11 IP X 4D Electrical protection:
Electronic card block is protected against water splash and humidity.
- 5 -
Revision Date: 29 February 2008, Rev. No: 0