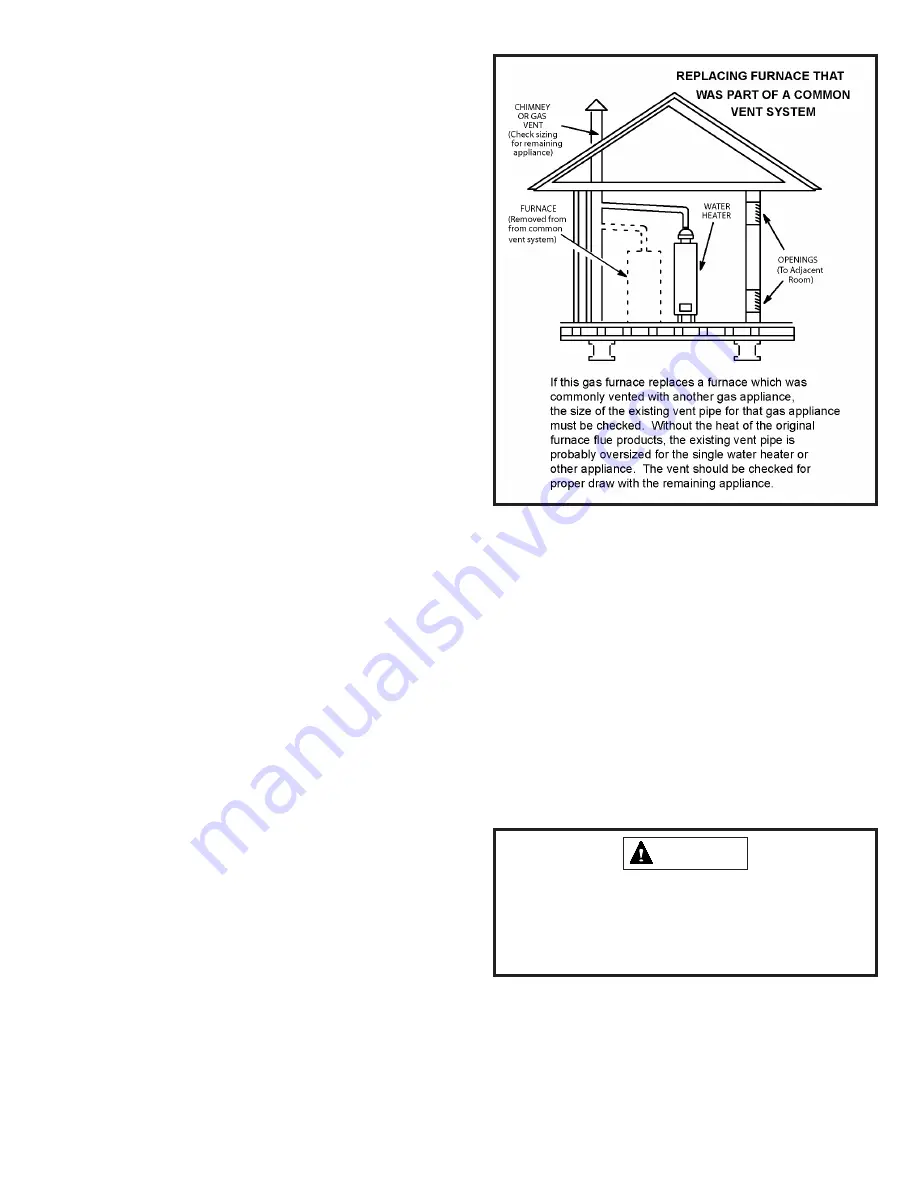
507206-01
Page 15 of 59
Issue 1337
Figure 20
1. Seal any unused openings in the common venting
system.
2. Inspect the venting system for proper size and horizontal
pitch. Determine that there is no blockage, restriction,
leakage, corrosion, or other deficiencies which could
cause an unsafe condition.
3. Close all building doors and windows and all doors
between the space in which the appliances remaining
connected to the common venting system are located
and other spaces of the building. Turn ON clothes
dryers and any appliances not connected to the common
venting system. Turn ON any exhaust fans, such as
range hoods and bathroom exhausts, so they will
operate at maximum speed. Do not operate a summer
exhaust fan. Close fireplace dampers.
4. Follow the lighting instructions. Turn ON the appliance
that is being inspected. Adjust the thermostat so that
the appliance operates continuously.
5. After the main burner has operated for 5 minutes, test
for leaks of flue gases at the draft hood relief opening.
Use the flame of a match or candle.
6. After determining that each appliance connected to
the common venting system is venting properly, (step
3) return all doors, windows, exhaust fans, fireplace
dampers, and any other gas burning appliances to their
previous mode of operation.
7. If a venting problem is found during any of the preceding
tests, the common venting system must be modified to
correct the problems.
Resize the common venting system to the minimum vent
pipe size determined by using the appropriate tables in
Appendix G. These are in the current standards of the
National Fuel Gas Code ANSI Z223.1.
1. In areas where piping penetrates joist or interior walls,
hole must be large enough to allow clearance on all
sides of pipe through center of hole using a hanger.
2. When furnace is installed in a residence where unit
is shut down for an extended period of time, such
as a vacation home, make provisions for draining
condensate collection trap and lines.
Exhaust Piping
Route piping to outside of structure. Continue with
installation following instructions given in piping termination
section.
Do not discharge exhaust into an existing stack or
stack that also serves another gas appliance. If vertical
discharge through an existing unused stack is required,
insert PVC pipe inside the stack until the end is even
with the top or outlet end of the metal stack.
CAUTION
Summary of Contents for 95G2DFE
Page 3: ...507206 01 Page 3 of 59 Issue 1337 Figure 1 ...
Page 17: ...507206 01 Page 17 of 59 Issue 1337 A95DF2E 95G2DFE Table 7A ...
Page 18: ...507206 01 Page 18 of 59 Issue 1337 A95DF2E 95G2DFE Table 7B ...
Page 19: ...507206 01 Page 19 of 59 Issue 1337 A95DF2E 95G2DFE Table 7C ...
Page 27: ...507206 01 Page 27 of 59 Issue 1337 Figure 32 ...
Page 34: ...507206 01 Page 34 of 59 Issue 1337 Figure 48 TRAP DRAIN ASSEMBLY USING 1 2 PVC or 3 4 PVC ...
Page 36: ...507206 01 Page 36 of 59 Issue 1337 Figure 50 Table 10 ...
Page 40: ...507206 01 Page 40 of 59 Issue 1337 TYPICAL WIRING DIAGRAM Figure 54 ...
Page 56: ...507206 01 Page 56 of 59 Issue 1337 Start UP Performance Check List ...