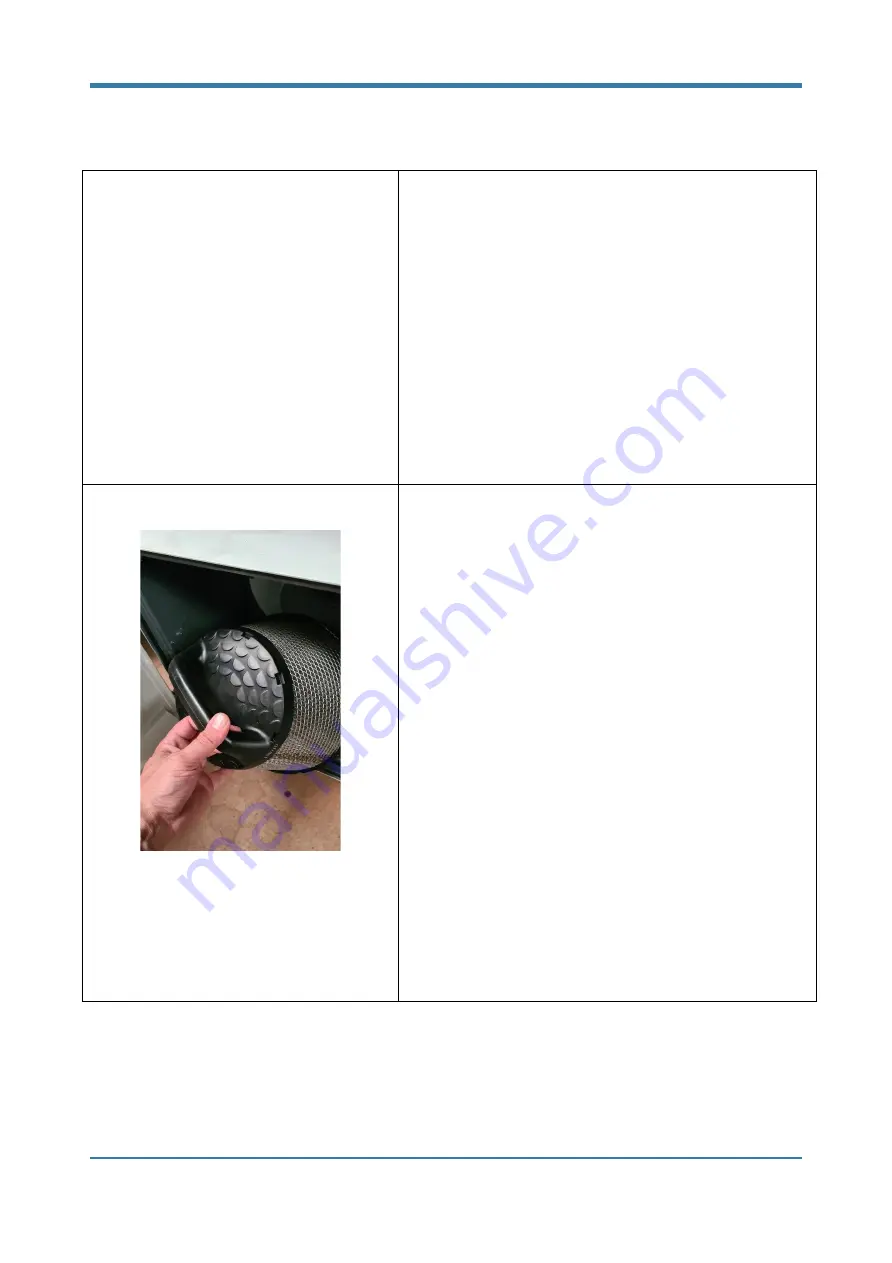
© Copyright AirBench Ltd 2022
Page 10 of 20
Cleaning times will vary per customer so please adjust
your maintenance intervals as required.
Pre-filters should be replaced every 12 months
Main filter
Once the pre-filter has been removed you can now
access and remove the main filter.
These are a very tight fitting as they are an airtight fit
around the inlet of the fan assembly, to remove grasp
the handle and provide a pulling motion until the filter
comes away from the housing.
To clean the main filter please soak in detergent as per
the pre-filter and then using compressed air blow
through the filter from the inside out to remove any
restrictions within the filter, this can then be refitted
along with the pre-filter.