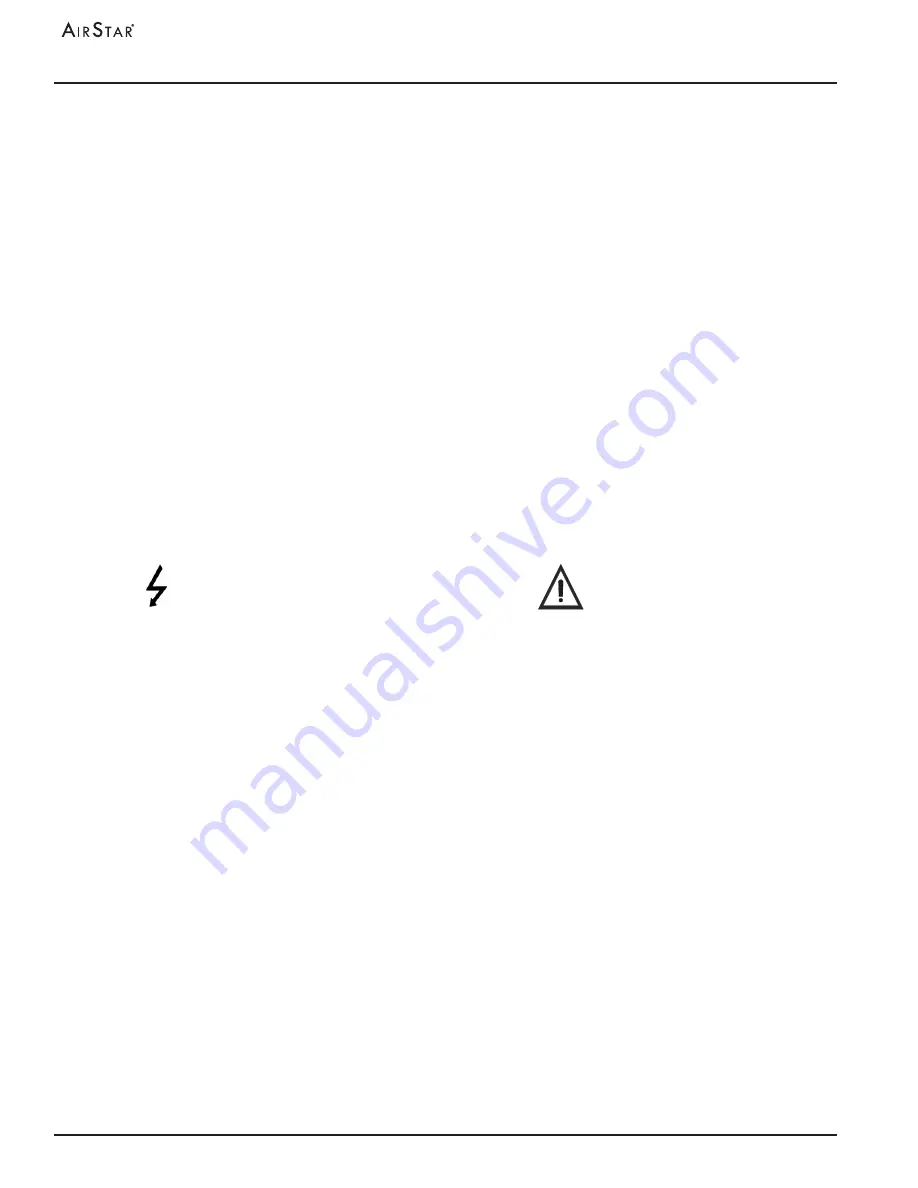
Air Techniques, Inc.
Page 8
AS12, AS22, AS50, AS70,
I n t e r n a t i o n a l
INSTALLATION INFORMATION
Important:
Each system should have a dedicated circuit panel .
Remove all power to the system prior to working
with electrical circuits. Contacting high voltage
can cause serious injury or even death.
All systems must be wired directly
from an electrical box that complies
with local electrical codes.
Note:
If voltage is higher than 242V, install a bucking transformer.
MINIMUM VOLTAGE:
The minimum voltage for an AS12INT, AS22INT, AS50INT or
AS70INT is 198 Volts . Install a boost transformer if the service is below this rating .
WIRING REQUIREMENTS:
To help prevent fire, electric shock, injury, or death, the
wiring and grounding must conform to the latest edition of the National Electrical Code,
ANSI/NFPA 70 and all applicable local regulations. Please contact a qualified electri
-
cian to check your wiring and breakers/fuses to ensure that there is adequate electrical
power to operate the
AIRSTAR
.
EQUIPMENT GROUNDING:
All
AIRSTARs
must be connected to a grounded metal,
permanent wiring system, or an equipment grounding conductor must be run with the
circuit conductors and connected to the equipment grounding lead in the
AIRSTAR's
flexible metal conduit power supply. Failure to do so can result in fire, electric shock,
injury, or death. See Figure 2, Overall Site Requirements, page 7.
ELECTRICAL POWER CONNECTION:
AS12INT is supplied with an installed line
cord with an IEC female connector that requires a 220V male IEC, minimum 16AWG,
connector . AS22INT, AS50INT and AS70INT systems are shipped with open electrical
connections, which are directly connected to the branch supply circuit as shown by
Figure 3 . See Site Electrical Requirements, page 7, for required branch circuit size for
each system .
AIRSTARs
are installed by authorized Air Techniques dealer technicians . Please review these
installation guidelines to make sure that your
AIRSTAR
works to capacity for your office . (See
Site Requirements, pages 6 & 7 .)
Your
AIRSTAR
should be installed in a well ventilated area, with at least 12 inch
clearance on each side for service access and to prevent overheating during high
demand periods . If other equipment is located in the vicinity, the ambient temperature
of the area must not exceed 105°F .
The installation site should be clean and dry to prevent the air intake filters from
clogging . If there is a concern about the quality of air where the
AIRSTAR
is placed,
we recommend an optional Remote Air Intake (See Optional Accessories, page 16)
which allows the compressor to intake clean air from a remote location .
Air distribution piping for all models should be 1/2", type "L" or type "K" copper .
PLUMBING CONNECTION:
The Tank Outlet Assembly (See Figure 1, View C), (the
storage tank outlet for the dry air) is connected to the operatory air system via a 3/8"
F .N .P .T . shut-off valve and 6 foot length of pressure hose (supplied) .