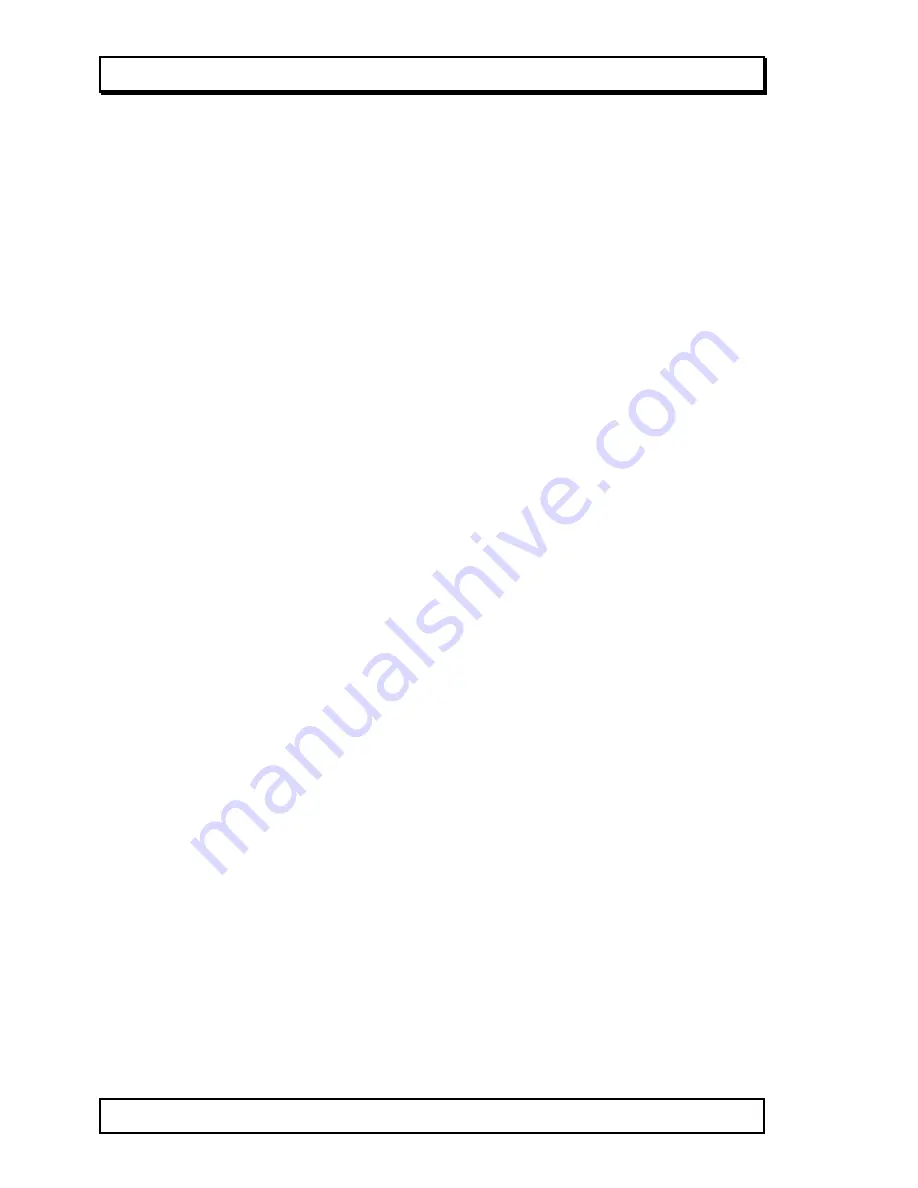
Gasguard
®
250 VMB System Installation Manual
Air Products and Chemicals, Inc.
Page A - 6
6.8.5
Finished tube and fittings in each lot shall be measured for interior surface
finish with a stylus type measuring device in accordance with ASME B46.1 -
1985. Surface roughness shall be measured at three locations for each
piece tested. Sample quantity for tubing shall be 10% of tube ends and 1%
of middle sections. Sample quantity for fittings shall be 10% of fitting ends.
The average of the readings shall not exceed 7 microinch Ra with no single
reading above 10 microinch Ra. Sampling length cutoff shall be 0.030" and
traverse length will be 0.150".
6.8.6
Scanning electron microscopy (SEM) photographs of finished component
surfaces shall be analyzed for each machining, honing, polishing, or
electropolishing process change or supply of material other than stainless
steel. SEM analysis shall verify that no more than 40 defects shall be
distinguishable in a 3600X field of view. A sample shall be taken from the
middle of the tube or fitting. The test method shall conform to SEMATECH
standard 90120401A-STD.
6.8.7
Chemistry analysis (ESCA) of electropolished surfaces shall be performed
for each electropolishing process change to verify surface elemental
composition. Elemental composition shall be expressed in atomic percent
units and shall verify chromium to iron ratio of 1.5:1 and a minimum
chromium oxide to iron oxide ratio of 3:1 for stainless steel.
6.8.8
Moisture testing shall be performed on one length of cleaned and packaged
tube from each heat for each size (O.D. and nominal wall thickness). Testing
shall verify the addition of less than 1 ppm moisture to nitrogen gas as
described in Section 8.1 of this specification while flowing N2 gas at a flow
not to exceed 10ÿSCFH/IN2.
6.8.9
Particle testing shall be performed on one length of cleaned and packaged
tube from each size (O.D. and nominal wall thickness). Testing shall verify
that particle counts be no more than 10 per cubic foot of size greater than or
equal to 0.1 microns and zero particles of size 0.3 microns or larger while
flowing nitrogen gas at a velocity of 133 ft/sec.
6.8.10
A weld test shall be performed for each heat and lot number of material that
is used. Weld tests on fittings can be avoided by completing this
requirement on the tube that will be used to make the fitting. The test welds
shall be made per Semiconductor Equipment Manufacturer Center
specification, QAF020. Weld test shall be deemed acceptable if no internal
discoloration of the weld is visible. Samples can be developed between
APCI and the tube vendor to judge acceptable welds.
6.8.11
A Rockwell hardness test shall be performed on each mill heat of material to
assure a Rockwell Rb 90 maximum hardness. This test shall be performed
for each size after "pulling".
Summary of Contents for Gasguard 250
Page 3: ......
Page 9: ...Gasguard 250 VMB System Installation Manual Air Products and Chemicals Inc Page i 2...
Page 50: ...Gasguard 250 VMB System Installation Manual Air Products and Chemicals Inc Page 5 6...
Page 60: ...Gasguard 250 VMB System Installation Manual Air Products and Chemicals Inc Page 6 10...
Page 68: ...Gasguard 250 VMB System Installation Manual Air Products and Chemicals Inc Page A 8...