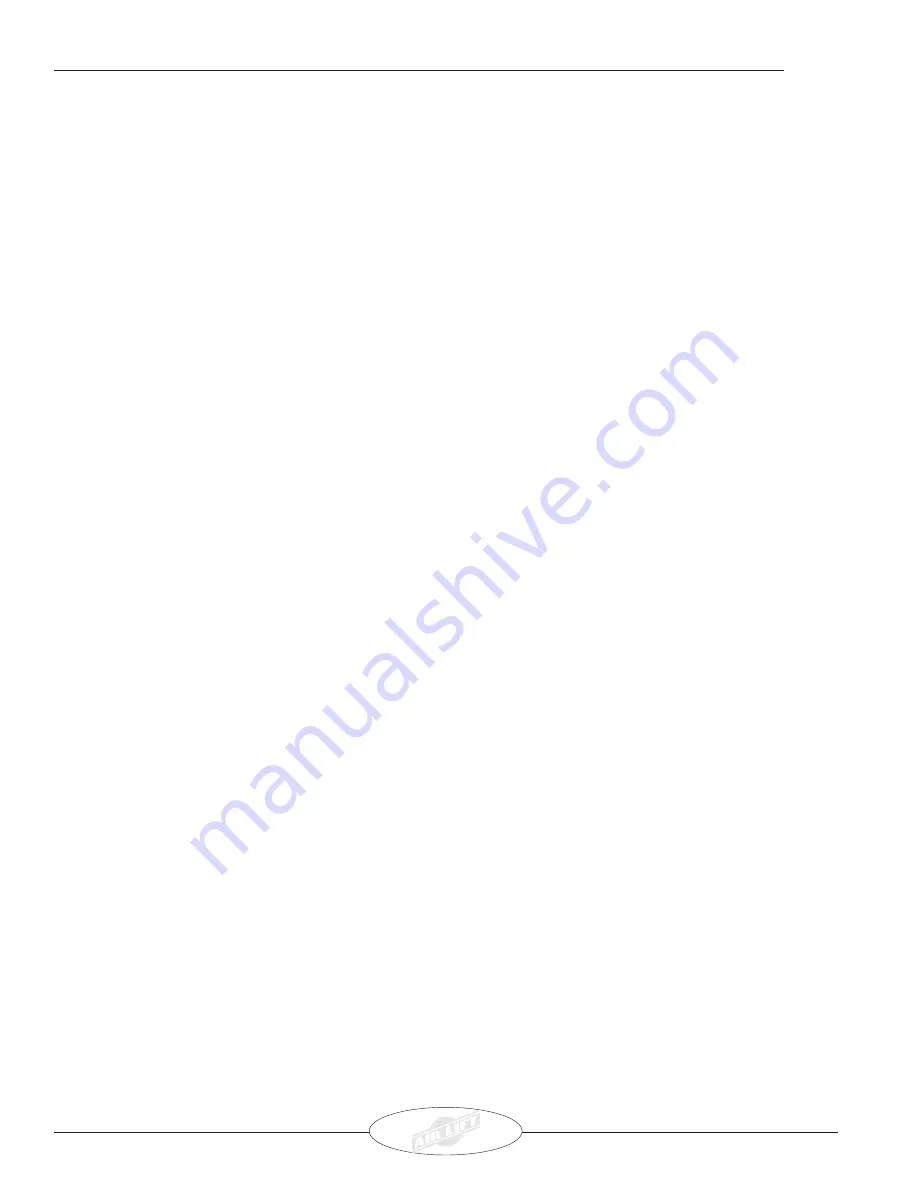
Customer Service
1-800-248-0892
2
STEP BY STEP INSTALLATION (REFER TO PAGE 3 FOR FIGURES 2–4)
As an exclusive feature from AIR LIFT you will find a completely preassembled wiring harness (2 coils), dual gauge
panel, and the compressor unit. There is no need to cut, solder, crimp, or measure. (Figure 1)
All pre-assembled gauge panels have been 100% leak and function tested. DO NOT attempt to tighten,
loosen or adjust any fitting or connection. This will likely cause a leak or malfunction and void the
warranty.
All of the electrical connections are matched by male to female push in terminals. All of the air line connections
will be white to white, green to green, indicated by the color band. The color band also serves as a reference point
for installing the air line into the fitting. Properly installed, the front edge of the color band should be against the
collar of the fitting (Figure 2 & 3).
Do not cut, trim, modify, or disassemble the harness. If you have excess length, simply coil it up and secure out of
the way with the provided tie straps.
We recommend that you install the air spring kit first.
1. Install the gauge panel. Select a convenient mounting location that has a rigid surface that will provide for a
sturdy mounting surface. The bottom edge of the dash on either side of the steering wheel is a good location.
Use the black self tapping screws to attach the panel to the selected location.
2. Now install the compressor unit. Refer to the Recommended Compressor Location list included with this kit.
Hold the compressor in the recommended location and use the provided silver self tapping screws to attach
the mounting brackets to the vehicle. In some cases the mounting area does not allow enough room to use
a drill to drive the screws in. It will be necessary to use the mounting brackets as a template to drill 13/64"
holes through the frame first and then use a 7/16" nut driver to install the self tapping screws. NOTE: Attach
the ground wire to one of the screws (Figure 1).
Box Frames
-In most cases the frame section will not be wide enough to mount the compressor legs flat to the
rail. It may be necessary to bend the mounting brackets into a 90 degree angle to allow the brackets to attach
to the side and bottom of the frame rail (Figure 5). The compressor mounting legs can be bent by putting the
bracket into a vise. Bend it by using a crescent wrench or tapping it lightly with a hammer, into a L shape.
CAUTION-Do not drill any holes into the frame or the floor board before checking for hydraulic lines, gas lines
and/or electrical wires that may need to be moved aside. Also, when attaching to the floor board, it is important
to check where the screws protrude through the floor board. It may be necessary to trim or cover the top of
the screws inside the vehicle. A sealer should be used around the screw to prevent the elements from entering
the cab area.
3. Now connect Wiring Harness #1 to the back of the gauge panel. With your thumb against the front side of
the switch, connect the wire by pushing the female connectors onto the blade connectors on the switch. Match
the air line by the color band on the air line to the color band on the tees. Push the air lines onto the T fittings
until the air line completely covers the barb (Figure 2). Some lubrication on the air line will ease pushing the
air line over the barb.
Do not connect the power wire at this time.
Wiring Harness #1 also connects the gauge panel to the Low Pressure Sensor assemblies. The Low Pressure
Sensors protect the air springs from failure due to low pressure in the unloaded condition. These sensors are
pre-set to maintain a MINIMUM pressure of 10 psi in the air springs. This is accomplished by sensing the
pressure in each spring and turning on the compressor if the pressure should fall below 10 psi. NOTE: The
Low Pressure Sensors are pre-assembled onto Wiring Harness #1. The sensors should be located under the
dash inside the vehicle and secured with the provided tie straps.
4. Connect the check valves and power wire on Harness #2 to the compressor as shown in Figure 4. DO NOT
OVERTIGHTEN THE CHECK VALVE CONNECTOR - HAND TIGHT IS SUFFICIENT.