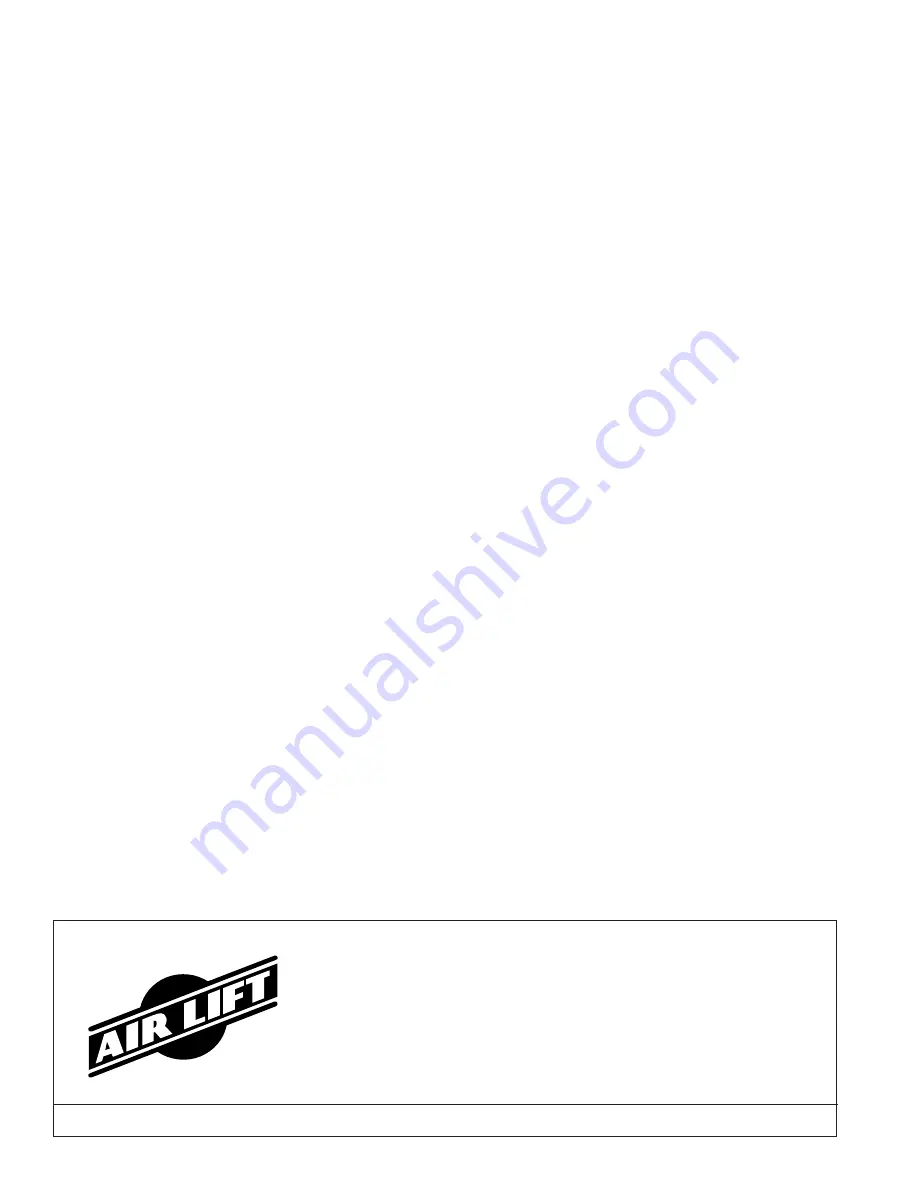
Customer Service
1-800-248-0892
4
For Technical Assistance call 1-800-248-0892
Thank you for purchasing Air Lift Products
Mailing Address:
Street Address:
AIR LIFT COMPANY
AIR LIFT COMPANY
P.O. Box 80167
2727 Snow Rd.
Lansing, MI 48908-0167
Lansing, MI 48917
Local Phone: (517) 322-2144
Fax: (517) 322-0240
4
Route Wiring Harness #2 from the compressor. Use existing grommets in the floorboard or firewall to route
the Harness from the compressor to the Low Pressure Sensors on Harness #1. In some cases a hole may
have to be drilled to allow access for the Harness. Drill a 1" diameter hole and install the provided grommet.
It will be necessary to seal any grommets or holes that have been cut, drilled or removed so as not to allow
elements to enter the cab area of the vehicle.
When routing Wiring Harness #2 from the compressor, it should NOT be routed so as to lay on, or near, the
exhaust pipe/muffler/catalytic convertor of the vehicle. Routing along the top of a crossmember or over a heat
shield is the recommended way of routing the harness.
5. Now connect Wiring Harness #2 to Wiring Harness #1 inside the vehicle. You need only to connect the red
wire from Harness #2 and the banded air lines to the Low Pressure Sensors.
See Figure 3 for air line and
electrical connection.
6. The next connection is between each air spring and the air line T fitting located just ahead of the check valves
in Harness #2 (Figure 1 & 4). With the Air Springs deflated, use a hose cutter, a razor blade, or very sharp
knife to cut the air line already installed between the air springs and the inflation valves. Install the provided
T fittings in each air line (Figure 1). Push the air line into each leg of the T until you feel a definite click. the
line should go in 9/16". Connect a single length of air line to the open leg of each tee. Bring each of the
lines to the T fittings in Harness #2 just in front of the check valves and connect as shown in Figure 4.
Route
the air line across the chassis from the far side over the exhaust system heat shields and along the
frame up to the compressor. Avoid heat sources, sharp edges and tight bends.
7. Now connect the power wire from Harness #1. Route it to the vehicle fuse box. Use a test light to determine
which open terminal (accessory, etc.) works only when the key is in the on or accessory position (or refer to
the owners manual for an available accessory fuse). The terminal should have an amperage rating equal to
or higher than the 15 amp in-line fuse. Connection to the fuse terminal will depend on what type of fuse your
vehicle uses. If your vehicle uses the barrel type fuse, use adapter #1. If you have the standard spade type
fuses, use adapter #2. Many late model vehicles use a smaller spade type fuse which requires adapter #3 -
see INSET A on front page. If adapter #1 or #2 are used, it will be necessary to cut off the 1/4" female
connector attached to the power wire and crimp the smaller 3/16" female connector supplied with this kit.
NOTE: Connect adapter to HOT side of the fuse (use a test light to determine). With the ignition on, the
compressor will turn on and fill the system to 10 p.s.i. before shutting off.
8. Press the off/on button to inflate both air springs and use the small deflate button to adjust the pressure.
Inflate to 30 p.s.i. (20 p.s.i. for AirLift 1000 kits). Check all fittings and inflation valve cores with
a soapy water solution for leaks.
9. Recheck air pressure after 24 hours. A 2-4 p.s.i. loss after initial installation is normal. If pressure
has dropped more than 5 p.s.i., re-test for leaks with soapy/water solution. Please read and follow
the Maintenance and Operating tips in the installation manual that came with your air spring kit.
If the compressor runs continually or often, there is most likely a leak. Disconnect the compressor at the
fuse box and test for leaks with a soapy water solution.
Never run compressor longer than 4 minutes continuously. Allow at least 5 minutes for cool down before
starting compressor again.