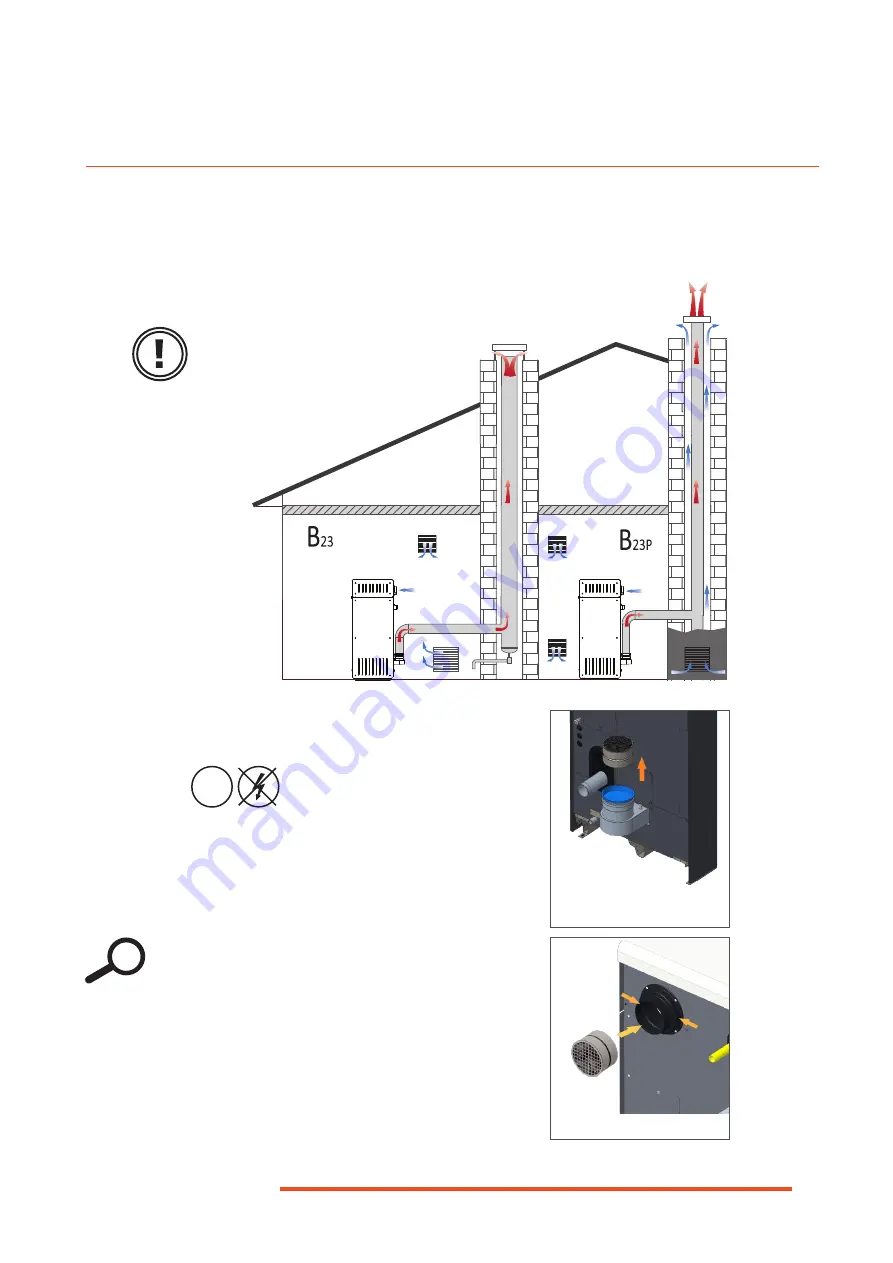
I-41
A-070336_EN • B_0821
P
roduct
I
nstallatIon
Silencer Installation in Open Chimney Sys-
tems (B)
Conditions:
Tools and material:
Cordless screwdriver, size 3.5
Procedure:
1. Remove silencer from its storage location, in
the flue connection.
î
Before installation, check on silenc-
er sticker that it is the correct com-
ponent for the boiler model. If not,
contact your AIC representative.
î
Be aware that the presence of the si-
lencer (B-type chimney connection) af-
fects the fan speed setting when carry-
ing out a gas conversion.
2. Install silencer into air inlet connection.
3. Secure with 2 screws.
OFF
i
Fig. 14. Silencer removal from
storage
Fig. 15. Silencer installation
Make sure that the ventila-
tion openings remain unob-
structed at all times.
B (Open)
Description
B
23
Combustion air is taken directly from the boiler room, fl ue gas is discharged outside of the room
where the appliance is installed (roof terminal).
B
23P
Same as B23, but using a positive pressure.