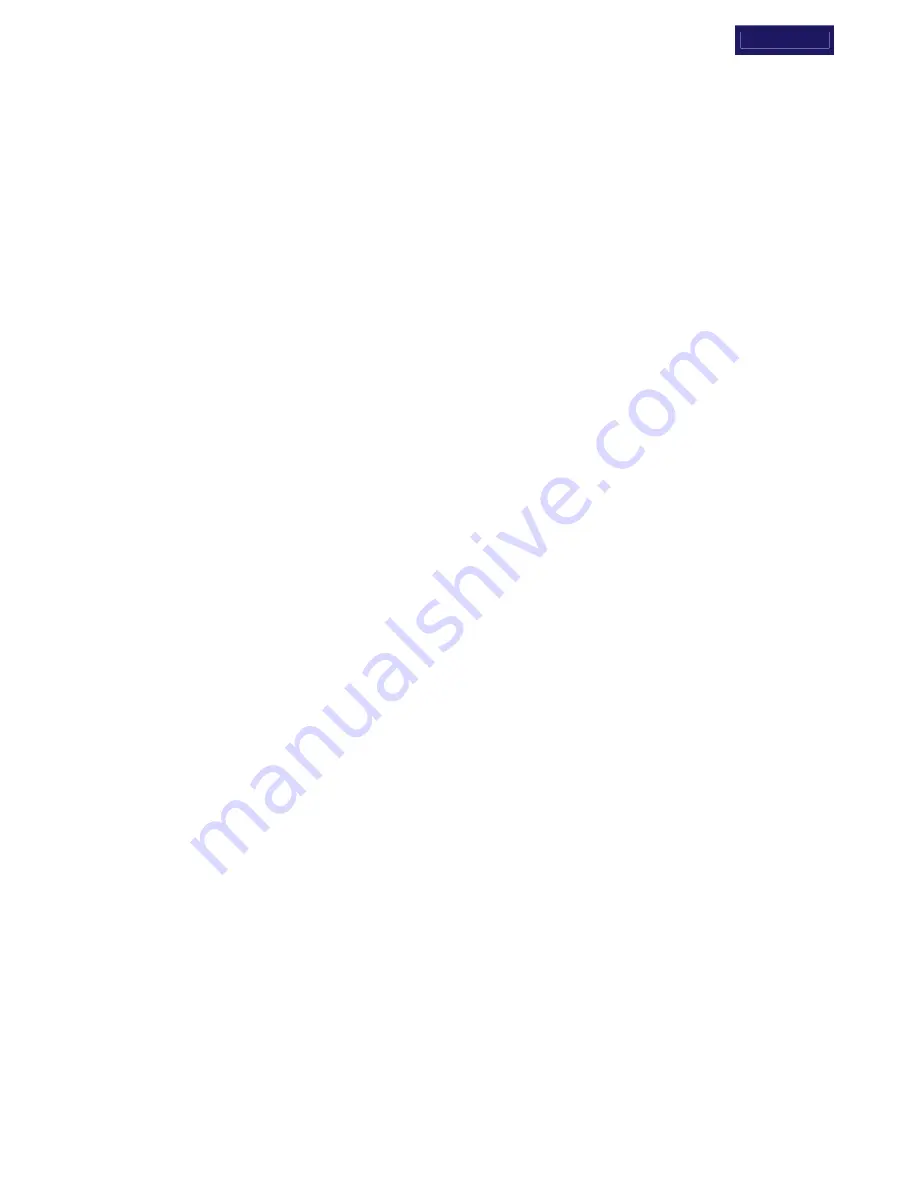
----EN
EN
EN
EN----
5.5 CONDENSER
The condenser is the component in which the gas coming from the compressor is cooled down and
condensed becoming a liquid. Mechanically, a serpentine copper tubing circuit (with the gas flowing inside)
is encapsulated in an aluminum fin package.
The cooling operation occurs via a high efficiency fan, creating airflow within the dryer, moving air through
the fin package. It’s mandatory that the ambient air temperature does not exceed the nominal values. It is
also important
TO KEEP THE CONDENSER UNIT FREE FROM DUST AND OTHER IMPURITIES
5.6 FILTER DRIER
Traces of humidity and slag can accumulate inside the refrigerating circuit. Long periods of use can also
produce sludge. This can limit the lubrication efficiency of the compressor and clog the expansion valve or
capillary tube. The function of the Filter Drier, located before the capillary tubing, is to eliminate any
impurities from circulating through the system.
5.7 AFTERCOOLER
The aftercooler is the element where the incoming hot air undergoes the cooling stage. Mechanically, it is
formed by a copper tubing circuit (with the compressed air flowing inside) immersed in an aluminium blades
package. The cooling operation occurs via a high efficiency axial ventilator which, in applying pressure on
the air contained within the dryer, forces it into the blades package. In models AHT 20-50 the aftercooler is
combined with the dryer’s condenser, thus forming just one heat exchanger battery, cooled by just one high
efficiency axial fan.
It is mandatory that the temperature of the ambient air will not exceed the nominal values of the dryer. It is
important
TO KEEP THE UNIT FREE FROM DUST AND OTHER IMPURITIES
taken in by the fan.
5.8 PRE-FILTER (FTP Series - 3 micron)
Positioned at the outlet of the aftercooler, it assures a good air cleanliness level, in addition to the complete
removal of the water condensed in the aftercooler.
REPLACE THE FILTERING ELEMENT (CARTRIDGE)
AT LEAST EVERY 12 MONTHS.
5.9 CAPILLARY TUBE
It consists of a piece of reduced cross section copper tubing located between the condenser and the
evaporator to form a throttling against the flow of the refrigerating fluid. This throttling creates a pressure
drop, which is a function of the temperature to be reached within the evaporator: the lower the capillary tube
outlet pressure, the lower the evaporation temperature. The length and the diameter of the capillary tubing
are accurately sized with the performance to be reached by the dryer; no maintenance/adjustment
operations are necessary.
5.10 ALU-DRY MODULE
The air-to-air and the air-to-refrigerant heat exchangers plus the demister type condensate separator are
housed in a unique module.
The counter-flows of compressed air in the air-to-air heat exchanger ensure maximum heat transfer. The large
cross section of flow channels within the heat exchanger module leads to low velocities and reduced power
requirements. The air-to-refrigerant exchanger, with counter-current flows, assure excellent performances.
The generous dimensions of the exchange surface determines the correct and complete evaporation of the
refrigerant (preventing liquid returning to the compressor). The high efficiency condensate separator is located
within the drying module. No maintenance is required and it offers the additional advantage of creating a cold
coalescing effect for excellent air drying results. The generous collection volume assures the correct operation
of the dryer even with extremely damp inlet air.
Summary of Contents for 20-350
Page 29: ...7 1 1 AHT 20 50 AC 7 1 2 AHT 75 AC 7 1 3 AHT 100 150 AC ...
Page 30: ...7 1 4 AHT 200 250 AC 7 1 5 AHT 300 350 AC ...
Page 31: ...7 2 1 AHT 20 50 ...
Page 32: ...7 2 2 AHT 75 ...
Page 33: ...7 2 3 AHT 100 ...
Page 34: ...7 2 4 AHT 150 ...
Page 35: ...7 2 5 AHT 200 250 ...
Page 36: ...7 2 6 AHT 300 350 ...
Page 41: ...NOTE ...
Page 42: ...NOTE ...
Page 43: ...NOTE ...
Page 44: ...GRAMAGLIA GO ...