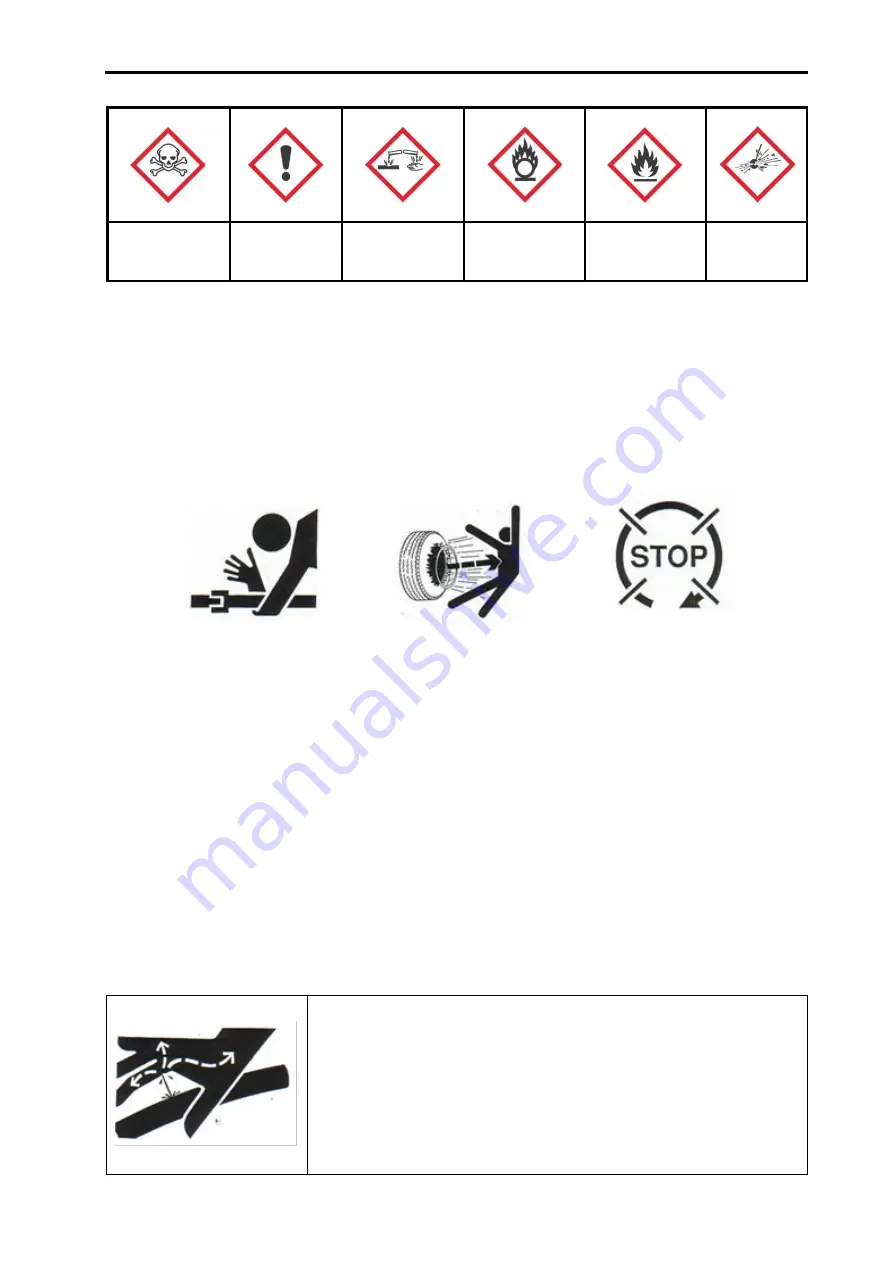
INSTRUCTIONS FOR USE
AGP 300 – 600 PRO
Rev.02/2019
11
1
2
3
4
5
6
1.
acute toxicity;
2.
acute toxicity, skin and respiratory tract irritant;
3.
corrosive;
4.
oxidising;
5.
inflammable materials;
6.
explosive materials – chemical products which can explode.
2.7
Danger of mechanical injuries
•
do not touch the machine while operating;
•
do not remove safety labels or any other safety equipment of the machine;
•
do not exceed air pressure in the tyres;
•
maintain the tyres regularly;
•
if using the machine in the public traffic you must fit it with lights and other illuminates in
accordance with traffic regulations;
•
do not enter the tank while preparing or cleaning;
•
never set working pressure above 15 bar (maximum allowed working pressure);
•
do not start working until you are sure that there are no unauthorized people in the vicinity
of the machine;
•
pull out the key from the key-lock after you have finished working to prevent sudden,
unwanted start of the machine.
2.8
Dangers, caused by liquids under high pressure
Liquids, leaking from the pipes, can be under high pressure and can
cause injuries to your skin, and cause dangerous injuries, if they
spread under your skin.
Never try to dismount a hydraulic pipe or any other of the hydraulic
installation as long as this one is under high pressure. Before you
start up the hydraulic system make sure that the installation is safe.