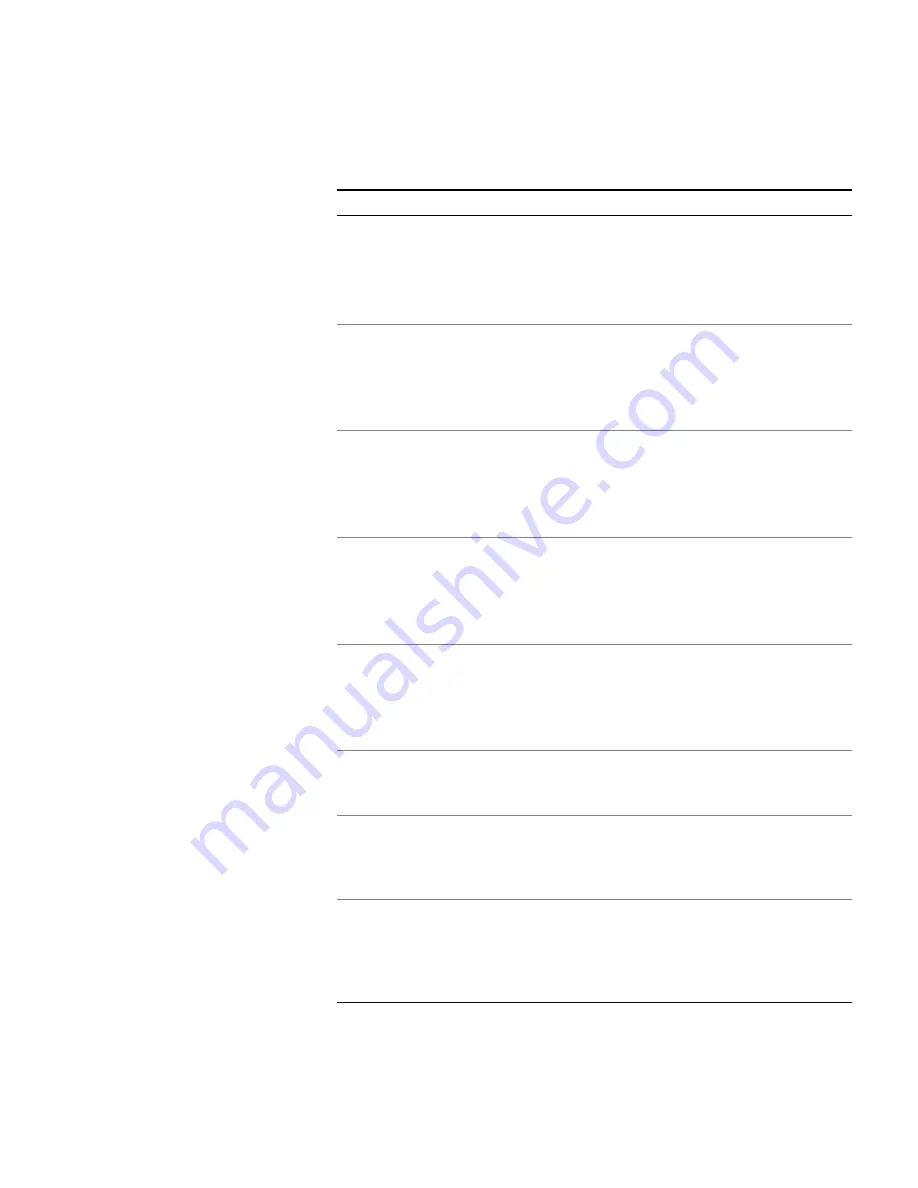
Supplemental Characteristics
110
Series N6700 User’s Guide
Supplemental Characteristics
Agilent Models N6751A/N6752A and N6761A/N6762A
N6751A / N6752A
N6761A / N6762A
Programming Ranges:
Voltage high range
20 mV – 51 V
15 mV – 51 V
Voltage low range (
≤
5.5 V)
N/A
12 mV – 5.5 V
Current high range
10 mA - 5.1A/10 mA- 10.2A
1 mA - 1.53 A/1 mA - 3.06 A
Current low range (
≤
0.1 A)
N/A
0.1 mA – 0.1 A
NOTE 1
Programming Resolution:
Voltage high range
3.5 mV
880
µ
V
Voltage low range (
≤
5.5 V)
N/A
90
µ
V
Current high range
3.25 mA
60
µ
A
Current low range (
≤
0.1 A)
N/A
2
µ
A
Measurement Resolution:
Voltage high range
1.8 mV
440
µ
V
Voltage low range (
≤
5.5 V)
N/A
44
µ
V
Current high range
410
µ
A 30
µ
A
Current low range (
≤
0.1 A)
N/A
1
µ
A
Programming Temperature Coefficient
per °C:
Voltage high range
18 ppm + 160
µ
V
18 ppm + 140
µ
V
Voltage low range (
≤
5.5 V)
N/A
40 ppm + 70
µ
V
Current high range
100 ppm + 45
µ
A
33 ppm + 10
µ
A
Current low range (
≤
0.1 A)
N/A
60 ppm + 1.5
µ
A
Measurement Temperature Coefficient
per °C:
Voltage high range
25 ppm + 35
µ
V
23 ppm + 40
µ
V
Voltage low range (
≤
5.5 V)
N/A
30 ppm + 40
µ
V
Current high range
60 ppm + 3
µ
A
40 ppm + 0.3
µ
A
Current low range (
≤
0.1 A)
N/A
50 ppm + 0.3
µ
A
Output Ripple and Noise (PARD):
CV peak-to-peak (typical value)
4 mV
4 mV
CC rms:
2 mA
2 mA
Common Mode Noise:
(from 20 Hz – 20 MHz; from either output to chassis)
rms
500
µ
A 500
µ
A
peak-to-peak
< 2 mA
< 2 mA
Over-voltage Protection:
Accuracy
0.25% + 250 mV
0.25% + 250 mV
Maximum setting
55 V
55 V
Response time
50
µ
s from occurrence of over-voltage
condition to start of output shutdown
1
If you are operating the unit below 255
µ
A in constant current mode, the output may
become unregulated with the following load conditions: The load resistance is <175 m
Ω
and
the load inductance is >20
µ
H. If this occurs, an UNRegulated flag will be generated and the
output current may rise above the programmed value but will remain less than 255
µ
A.