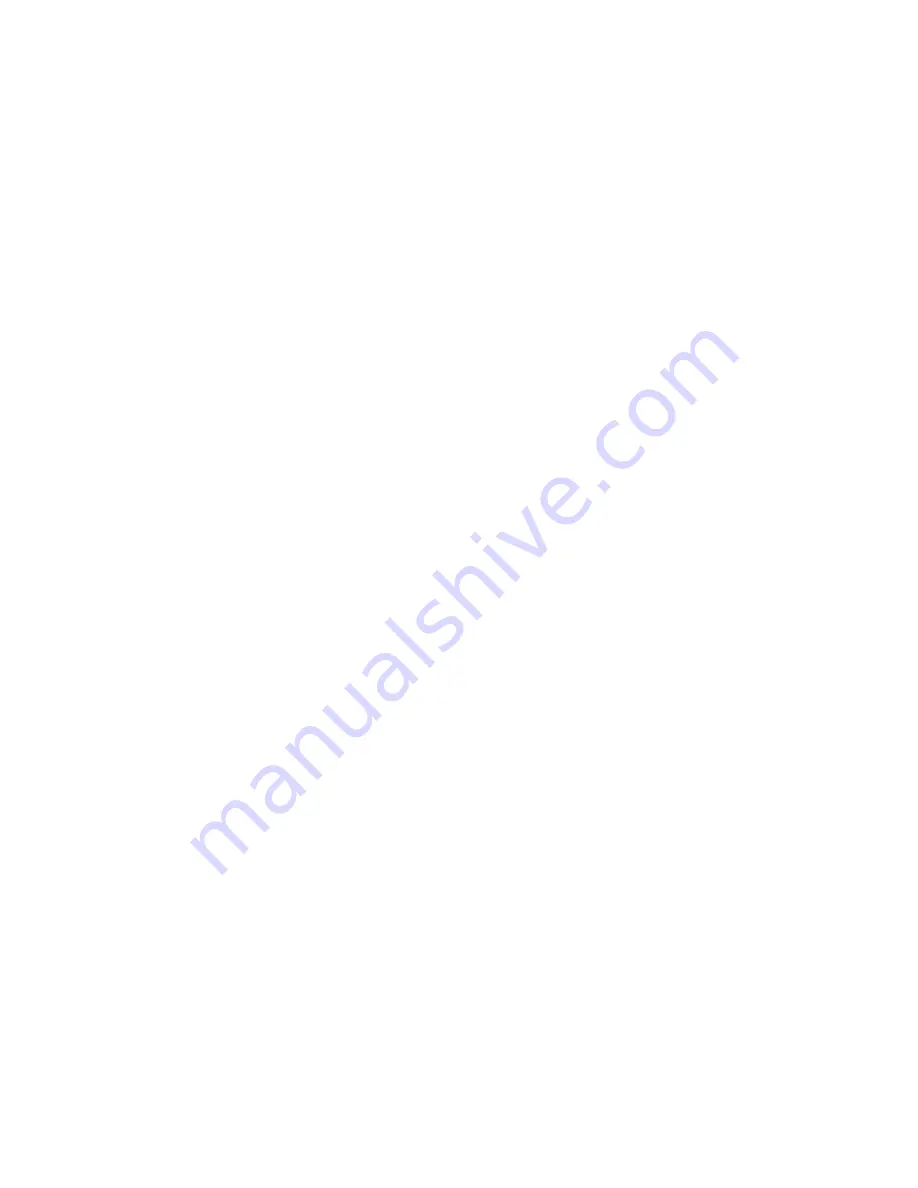
NOTE
The MODEL command removes all calibration
constants and substitutes default values. Consequently,
after the MODEL command is sent, you must recalibrate
each output.
10 OUTPUT 705; "CMODE 1"
20 OUTPUT 705; "MODEL 6624A"
30 OUTPUT 705; "CMODE 0"
40 OUTPUY 705; "CLR"
50 END
After sending the above program, wait at least 3 seconds for
the supply to complete initialization. Next, cycle the ac
power to initiate a power-on self test and initialize the
supply; then perform the calibration procedures outlined in
Appendix A of the Operating Manual.
4-22
Signature Analysis Testing
The easiest and most efficient method of troubleshooting
microprocessor-based instruments is signature analysis
which is similar to signal tracing with an oscilloscope in
linear circuits. Part of the microcomputer memory is
dedicated to signature analysis and a known bit stream is
generated to stimulate as many nodes as possible within the
circuit. However, because it is virtually impossible to
analyze a bit stream with an oscilloscope, a signature
analyzer is used to compress the bit stream into a four-
character signature. By comparing signatures of the IC
under test to the correct signatures for each node, faults can
usually be isolated to one or two components.
Signature Analysis (S.A.) Tests 1 through 8 (Tables 4-6
through 4-13, respectively) test most of the circuits on the
sequence (i. e. Test No. 1, No. 2, etc.). Note that the
signatures taken for the ROM (S.A. Test No. 2, Table 4-7)
apply only to firmware revision A_02 (date 2629), see
paragraph 4-24.
The general test setup for S.A. tests is given in paragraph 4-
23. The following general notes apply to signature analysis
1. Be certain to use the correct test setup.
2. Note the signatures for Vcc (+ 5 V) and ground on the
IC being examined. If an incorrect signature is the same
as that of Vcc or ground, that point is probably shorted
to Vcc or ground.
3. If two pins have identical signatures, they are probably
shorted together. If two signatures are similar, it is only
a concidence.
4. If a signature is incorrect at an input pin, but is correct
at its source (output of the previous IC), check for
printed circuit and soldering problems.
5. An incorrect signature at an output could be caused by
a faulty component producing that output. It can also
be caused by an input short circuit in another
component on the board.
4-23 Test Setup for S.A
Figure 4-8 shows the general test setup for the signature
analysis tests given in Tables 4-6 through 4-13. Note that
jumper pack W202 can be installed in either of two positions
as shown in Figure 4-8. The following is a general
description of the test setup. Specific signature analyzer and
jumper connections for each test are given in the applicable
table.
described in paragraph 4-19. Be sure that the power
supply is turned off before continuing with the
following steps.
b. Connect jumper W201 in the SIG. ANALYSIS position
(across pins 5 and 6) of connector P201 as shown in
Figure 4-8.
c. Short pins 1 and 4 together on connectors P205 through
P208 as shown in Figure 4-8.
d. Check that jumper pack W202 is in the proper position
specified by the particular S.A. test. Figure 4-8 shows
two operating positions: normal run position and NOP
(no operation) position. W202 is a 16-pin jumper pack.
To select the normal run position, W202 is plugged into
16-pin socket J202. To select the NOP position, W202 is
connected between 8-pin socket J203 and pins 1-8 of 16-
pin socket J202 (see Figure 4-8).
e. Set the signature analyzer START, STOP, CLOCK,
GND, and edge settings as described in the applicable
S.A. Test table.
f. Turn the power supply on and use the signature
analyzer probe to take signatures at the applicable IC
test points (see Table 4-6 through 4-13).
g. Upon completion of the S.A. tests, remove short circuit
connections from pins 1 and 4 on P205-P208 And return
jumpers W201 and W202 to their normal run positions.
4-24 Firmware
Revisions
ROM? command can be used to query the revision date. As
stated in paragraph 4-22, the revision date for firmware
revision A_02 is 2629; where 26 specifies 1986 and 29 is the
week number. The previous firmware revision was 1.01
(2605). To query the revision date of the firmware (ROM) in
your supply, run the short program listed below.
10 OUTPUT 705;”ROM?"
20 ENTER 705;A
30 DISP A
40 END
The computer should display the revision date; e.g. "2629"
No. 2) for the ROM are for revision A_02 and will be
different for different revisions. The signatures for the
previous revision (1.01) are given in Appendix A in the back
of this manual.
4-14
a.
Gain access to the GPIB board components as
GPIB board as well as the keypad and display circuit boards
on the front panel. The tests should be performed in
The ROM chip (U206) on the GPIB board is identified with a
label that specifies the revision of your supply's firmware.
Alternatively, if the GPIB board is operating properly, the
of the GPIB board.
Note that the signatures in Table 4-7 (GPIB Board S.A. Test
Summary of Contents for 6621A
Page 12: ...2 2...
Page 16: ...2 6...
Page 19: ...2 9...
Page 22: ...2 12...
Page 25: ...Figure 2 7 Typical Output Range Characteristics 2 15...
Page 28: ...2 18...
Page 30: ...3 2...
Page 31: ...3 3...
Page 44: ...3 16...
Page 45: ...3 17...
Page 48: ...4 3...
Page 51: ...4 6...
Page 55: ...4 10...
Page 56: ...4 11...
Page 57: ...4 12...
Page 60: ...4 15...
Page 61: ...4 16...
Page 62: ...4 17...
Page 63: ...4 18...
Page 64: ...4 19...
Page 65: ...4 20...
Page 67: ...4 22...
Page 68: ...4 23...
Page 70: ...4 25...
Page 71: ...4 26...
Page 72: ...4 27...
Page 73: ...4 28...
Page 74: ...4 29...
Page 76: ......
Page 77: ...4 32...
Page 78: ...4 33...
Page 79: ...4 34...
Page 80: ...4 35...
Page 81: ...4 36...
Page 82: ...4 37...
Page 83: ...4 38...
Page 84: ...4 39...
Page 85: ...4 40...
Page 86: ...4 41...
Page 87: ...4 42...
Page 88: ...4 43...
Page 89: ...4 44...
Page 90: ...4 45...
Page 91: ...4 46...
Page 92: ...4 47...
Page 93: ...4 48...
Page 98: ...4 53...
Page 100: ...4 55...
Page 101: ...4 56...
Page 102: ...4 57...
Page 103: ...4 58...
Page 128: ...6 2...
Page 129: ...6 3...
Page 131: ...Figure 6 1 Power Distribution Schematic sheet 1 of 2 6 5...
Page 132: ...Figure 6 1 Power Distribution Schematic sheet 2 of 2 6 6...
Page 135: ...Figure 6 3 Output 1 2 Board Component Location 6 9...
Page 136: ...Figure 6 3 Output 1 2 Board Schematic Diagram sheet 1 of 4 6 10...
Page 137: ...Figure 6 3 Output 1 2 Board Schematic Diagram sheet 2 of 4 6 11...
Page 138: ...Figure 6 3 Output 1 2 Board Schematic Diagram sheet 3 of 4 6 12...
Page 139: ...Figure 6 3 Output 1 2 Board Schematic Diagram sheet 4 of 4 6 13...
Page 140: ...Figure 6 4 Output 3 4 Board Component Location 6 15...
Page 141: ...Figure 6 4 Output 3 4 Board Schematic Diagram sheet 1 of 4 6 16...
Page 142: ...Figure 6 4 Output 3 4 Board Schematic Diagram sheet 2 of 4 6 17...
Page 143: ...Figure 6 4 Output 3 4 Board Schematic Diagram sheet 3 of 4 6 3 6 18...
Page 144: ...Figure 6 4 Output 3 4 Board Schematic Diagram sheet 4 of 4 6 3 6 19...
Page 145: ...Figure 6 5 Output 1 2 80W Board Component Location 6 21...
Page 146: ...Figure 6 5 Output 1 2 80W Board Schematic Diagram sheet 1 of 4 6 22...
Page 147: ...Figure 6 5 Output 1 2 80W Board Schematic Diagram sheet 2 of 4 6 23...
Page 148: ...Figure 6 5 Output 1 2 80W Board Schematic Diagram sheet 3 of 4 6 24...
Page 149: ...Figure 6 5 Output 1 2 80W Board Schematic Diagram sheet 4 of 4 6 25...
Page 151: ...A 2...
Page 152: ...A 3...