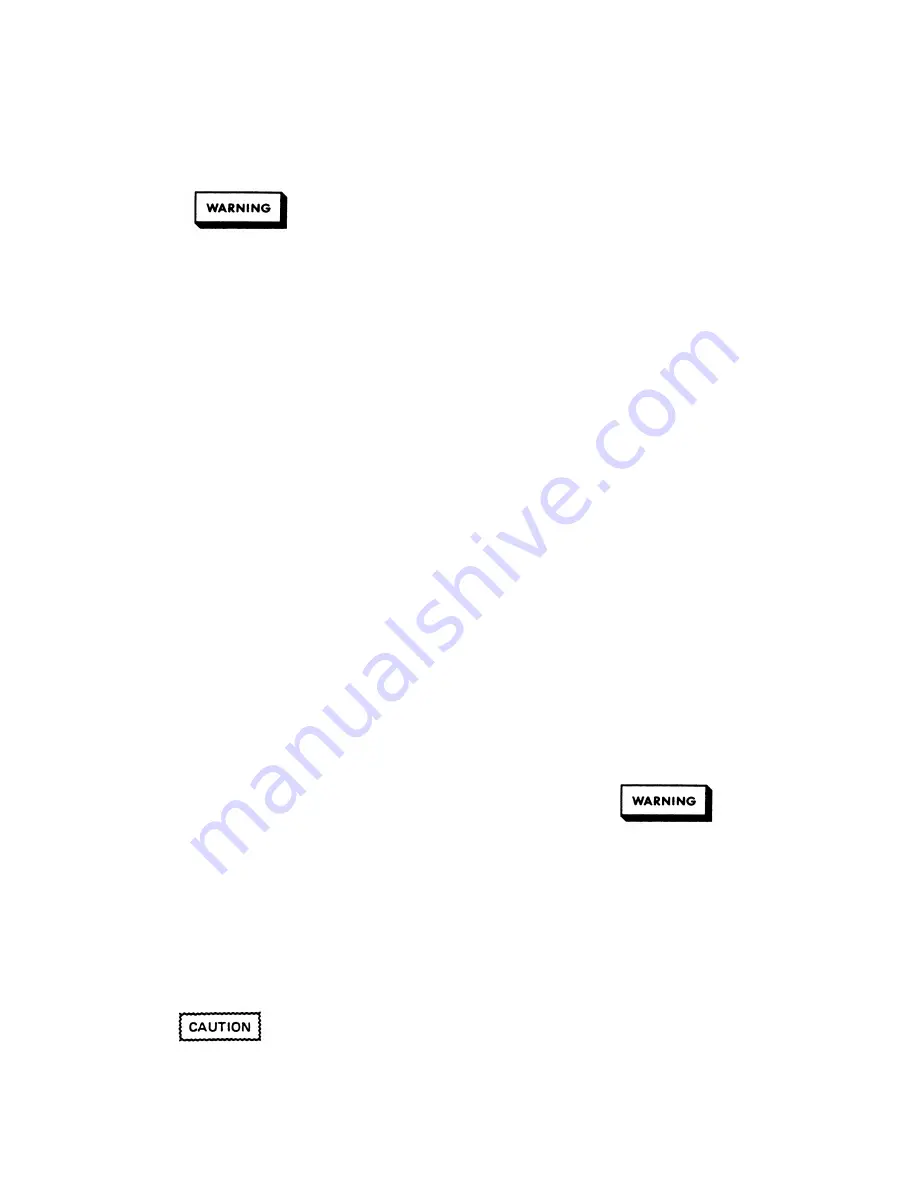
Section IV
Most of the maintenance procedures given in this
section are performed with power applied and
protective covers removed. Such maintenance should
be performed only by service-trained personnel who
are aware of the hazards involved (for example, fire
and electrical shock).
4-1 INTRODUCTION
This section provides troubleshooting and repair
information for the power supply. The troubleshooting
technique is to first isolate the problem to an assembly and
then follow the troubleshooting procedure provided for the
board) troubleshooting procedures will isolate the problem
to the defective component or circuit on the board.
Before attempting to troubleshoot the supply, ensure that
the fault is with the supply itself and not with an associated
circuit, load, or power line. The verification tests described
in Section III enable this to be determined without having to
remove the covers from the supply.
The most important aspect of troubleshooting is the
formulation of a logical approach to locating the source of
trouble. A good understanding of the principles of
operation is particularly helpful and it is recommended that
Section II of this manual as well as the Operating Manual
(Agilent Part No. 9557-6377 ) be reviewed before attempting
to troubleshoot the unit.
If a component is found to be defective, replace it and re-
conduct the performance tests given in Section III of this
supply must first be recalibrated as described in Appendix
A of the operating Manual. If an Output board is replaced,
the associated output channel must be recalibrated. If a
component in the output circuits or readback circuits on an
output board is replaced, the output must be calibrated
before you can reconduct the performance tests.
Section V in this manual lists all of the replaceable parts for
the power supply.
4-2 ELECTROSTATIC
PROTECTION
This instrument uses components which can be
damaged by static charge. Most semiconductors can
suffer serious performance degradation as a result of
static charge, even though complete failure may not
occur. The following precautions should be observed
when handling static-sensitive devices.
a. Always turn power off before removing or installing
printed circuit boards or components.
b. Always store or transport static-sensitive devices (all
semiconductors and thin-film devices) in conductive
material. Attach warning labels to the container or bag
enclosing the device.
c. Handle static-sensitive devices only at static-free work
stations. These work stations should include special
conductive work surfaces (such as Agilent Part No.
9300-0797) grounded through a one-megohm resistor.
Note that metal table tops and highly conductive
carbon-impregnated plastic surfaces are too conductive;
they can shunt charges too quickly. The work surfaces
should have distributed resistance between 10
6
and 10
12
ohms per square.
d. Ground all conductive equipment or devices that may
come in contact with static-sensitive devices or
assemblies.
e. Where direct grounding of objects in the work area is
impractical, a static neutralizer should be used (ionized-
air blower directed at work). Note that this method is
considerably less effective than direct grounding and
provides less protection for static-sensitive devices.
f. While working with equipment on which no point
exceeds 500 volts, use a conductive wrist strap in
contact with skin. The wrist strap should be connected
to ground through a one-megohm resistor. A wrist
strap with insulated cord and built-in resistor is
recommended, such as 3M Co. No. 1066 Agilent Part
No. 9300-0969 (small wrist size) and 9300-0970 (large).
Do not wear a conductive wrist strap when working
with potentials in excess of 500 volts; the one-megohm
resistor will provide insufficient current limiting for
personal safety.
g. All grounding (device being repaired, test equipment,
soldering iron, work surface, wrist strap, etc.) should be
done to the same point.
h. Do not wear synthetic (e.g. nylon) clothing. Keep
clothing of any kind from coming within 12 inches of
static-sensitive devices.
i. Low-impedance test equipment (signal generators, logic
pulsers, etc.) should be connected to static-sensitive
inputs only while the components are powered.
4-1
TROUBLESHOOTING
faulty assembly. The assembly (GPIB board or output
manual. When the GPIB board or the EEPROM (U221) IC on
the GPIB board is replaced, each output present in the
Summary of Contents for 6621A
Page 12: ...2 2...
Page 16: ...2 6...
Page 19: ...2 9...
Page 22: ...2 12...
Page 25: ...Figure 2 7 Typical Output Range Characteristics 2 15...
Page 28: ...2 18...
Page 30: ...3 2...
Page 31: ...3 3...
Page 44: ...3 16...
Page 45: ...3 17...
Page 48: ...4 3...
Page 51: ...4 6...
Page 55: ...4 10...
Page 56: ...4 11...
Page 57: ...4 12...
Page 60: ...4 15...
Page 61: ...4 16...
Page 62: ...4 17...
Page 63: ...4 18...
Page 64: ...4 19...
Page 65: ...4 20...
Page 67: ...4 22...
Page 68: ...4 23...
Page 70: ...4 25...
Page 71: ...4 26...
Page 72: ...4 27...
Page 73: ...4 28...
Page 74: ...4 29...
Page 76: ......
Page 77: ...4 32...
Page 78: ...4 33...
Page 79: ...4 34...
Page 80: ...4 35...
Page 81: ...4 36...
Page 82: ...4 37...
Page 83: ...4 38...
Page 84: ...4 39...
Page 85: ...4 40...
Page 86: ...4 41...
Page 87: ...4 42...
Page 88: ...4 43...
Page 89: ...4 44...
Page 90: ...4 45...
Page 91: ...4 46...
Page 92: ...4 47...
Page 93: ...4 48...
Page 98: ...4 53...
Page 100: ...4 55...
Page 101: ...4 56...
Page 102: ...4 57...
Page 103: ...4 58...
Page 128: ...6 2...
Page 129: ...6 3...
Page 131: ...Figure 6 1 Power Distribution Schematic sheet 1 of 2 6 5...
Page 132: ...Figure 6 1 Power Distribution Schematic sheet 2 of 2 6 6...
Page 135: ...Figure 6 3 Output 1 2 Board Component Location 6 9...
Page 136: ...Figure 6 3 Output 1 2 Board Schematic Diagram sheet 1 of 4 6 10...
Page 137: ...Figure 6 3 Output 1 2 Board Schematic Diagram sheet 2 of 4 6 11...
Page 138: ...Figure 6 3 Output 1 2 Board Schematic Diagram sheet 3 of 4 6 12...
Page 139: ...Figure 6 3 Output 1 2 Board Schematic Diagram sheet 4 of 4 6 13...
Page 140: ...Figure 6 4 Output 3 4 Board Component Location 6 15...
Page 141: ...Figure 6 4 Output 3 4 Board Schematic Diagram sheet 1 of 4 6 16...
Page 142: ...Figure 6 4 Output 3 4 Board Schematic Diagram sheet 2 of 4 6 17...
Page 143: ...Figure 6 4 Output 3 4 Board Schematic Diagram sheet 3 of 4 6 3 6 18...
Page 144: ...Figure 6 4 Output 3 4 Board Schematic Diagram sheet 4 of 4 6 3 6 19...
Page 145: ...Figure 6 5 Output 1 2 80W Board Component Location 6 21...
Page 146: ...Figure 6 5 Output 1 2 80W Board Schematic Diagram sheet 1 of 4 6 22...
Page 147: ...Figure 6 5 Output 1 2 80W Board Schematic Diagram sheet 2 of 4 6 23...
Page 148: ...Figure 6 5 Output 1 2 80W Board Schematic Diagram sheet 3 of 4 6 24...
Page 149: ...Figure 6 5 Output 1 2 80W Board Schematic Diagram sheet 4 of 4 6 25...
Page 151: ...A 2...
Page 152: ...A 3...