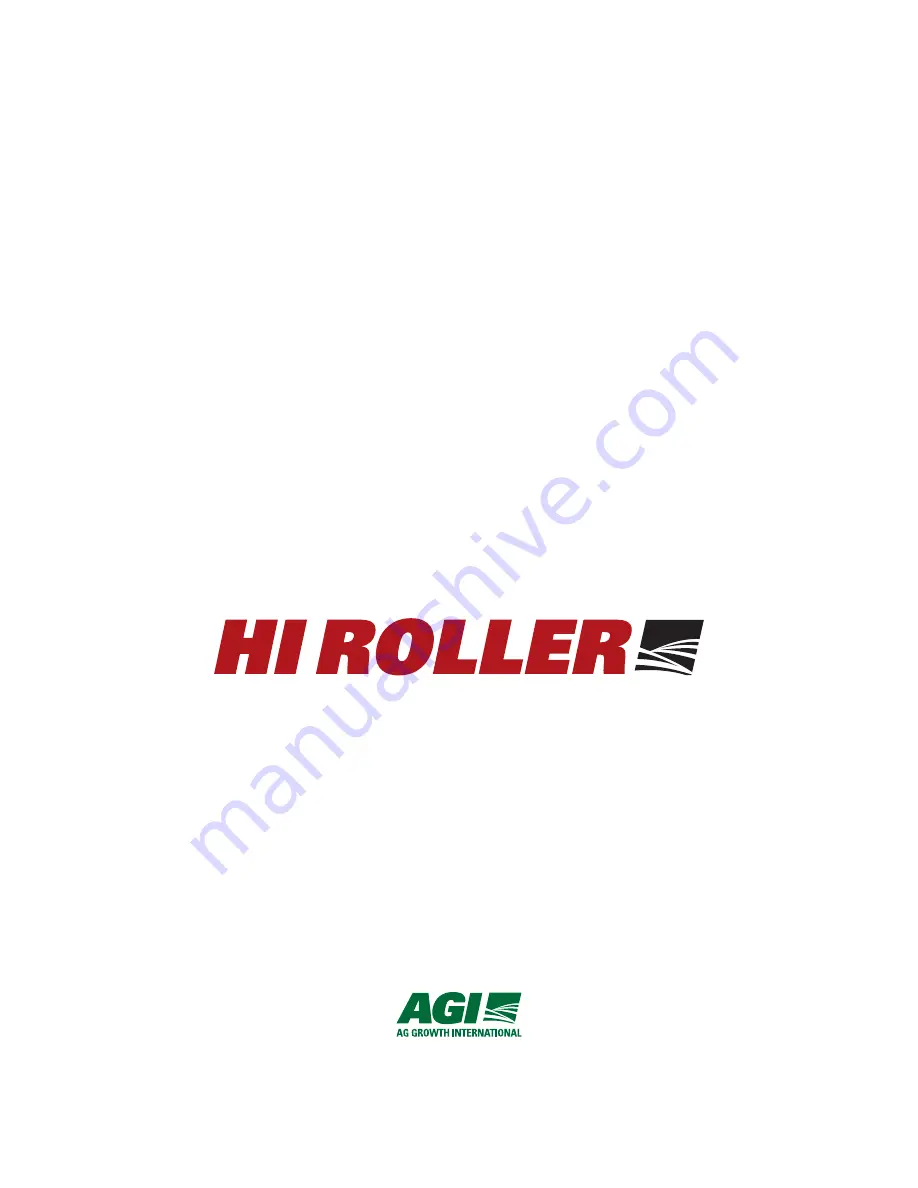
Part of the Ag Growth International Inc. Group
4511 N Northview Ave
Sioux Falls, SD 57107
Toll free (US & Canada): 800-328-1785
Phone: 605-332-3200
Fax: 605-332-1107
www.hiroller.com
e-mail: [email protected]
© Ag Growth International 2014
Part of the Ag Growth International Inc. Group
4511 N Northview Ave
Sioux Falls, SD 57107
Toll free (US & Canada): 800-328-1785
Phone: 605-332-3200
Fax: 605-332-1107
www.hiroller.com
e-mail: [email protected]
© Ag Growth International 2014