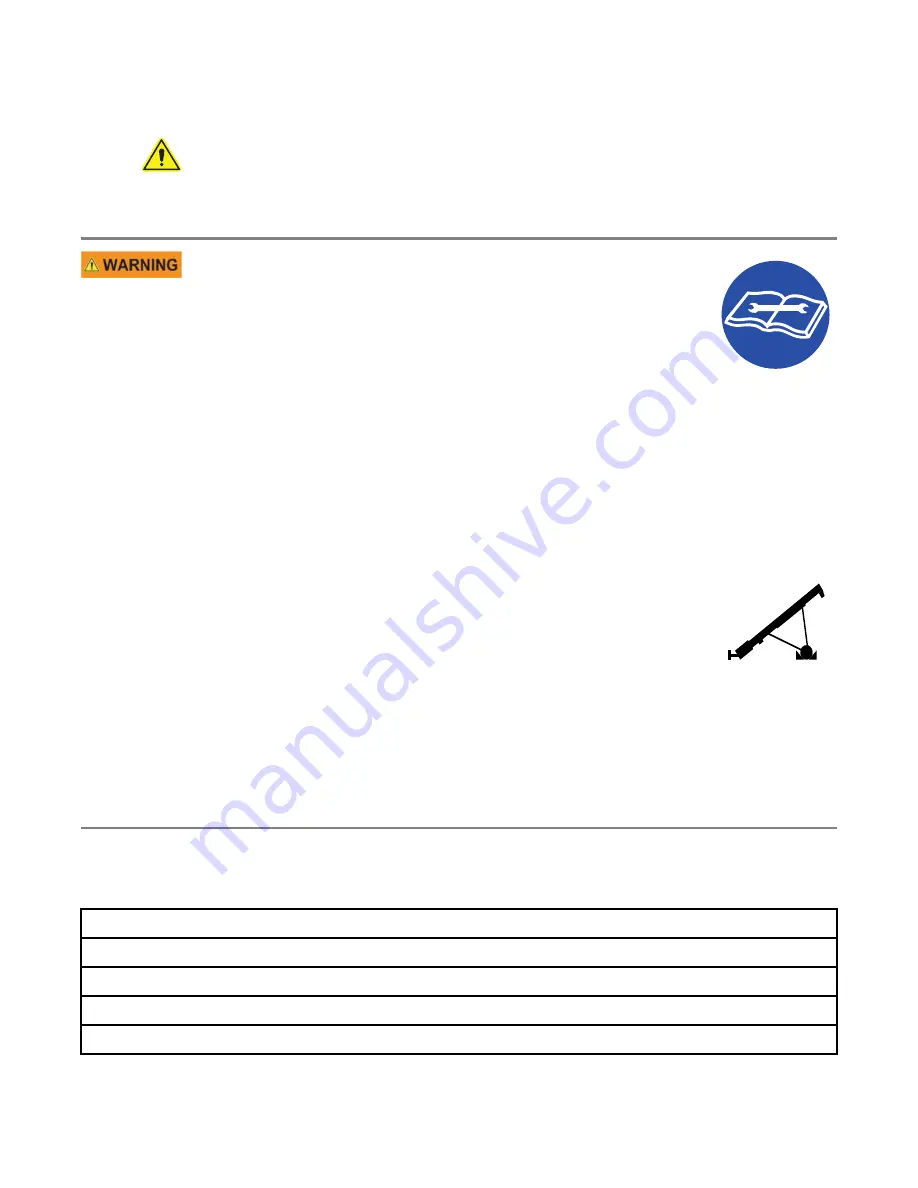
8210-00001 R0
35
7. Maintenance
Before continuing, ensure you have completely read and understood this manual’s
Safety section, in addition to the safety information in the section(s) below.
7.1. Maintenance Safety
• Keep components in good condition. Follow the maintenance
procedures.
• Ensure the service area is clean, dry, and has sufficient
lighting.
• Do not modify any components without written authorization
from the manufacturer. Modification can be dangerous and
result in serious injuries.
• Shut down and lock out power before maintaining
equipment.
• After maintenance is complete, replace all guards, service
doors, and/or covers.
• Use only genuine AGI replacement parts or equivalent. Use of
unauthorized parts will void warranty. If in doubt, contact
AGI or your local dealer.
Before attempting maintenance of any kind:
• Lower the conveyor fully.
• Chock wheels.
• Support tube if performing maintenance on the
undercarriage assembly.
•
If equipped with hydraulics:
Before applying pressure to a
hydraulic system, make sure all components are tight and
that hoses and couplings are in good condition.
7.2. Maintenance Schedule
Proper maintenance habits mean a longer life, better efficiency, and safer operation. Please follow the
Maintenance Schedule below. Keep good records of the hours the conveyor has been operated and the
maintenance performed.
Daily:
Section 7.3 – Visually Inspect the Equipment on page 36
Section 7.4 – Lubricate the Equipment on page 37
Monthly:
Hydraulic Drive Models:
Section 7.6 – Inspect Hydraulic Hoses and Fittings on page 38
PTO TOP-DRIVE FIELD LOADER – PORTABLE GRAIN BELT CONVEYOR