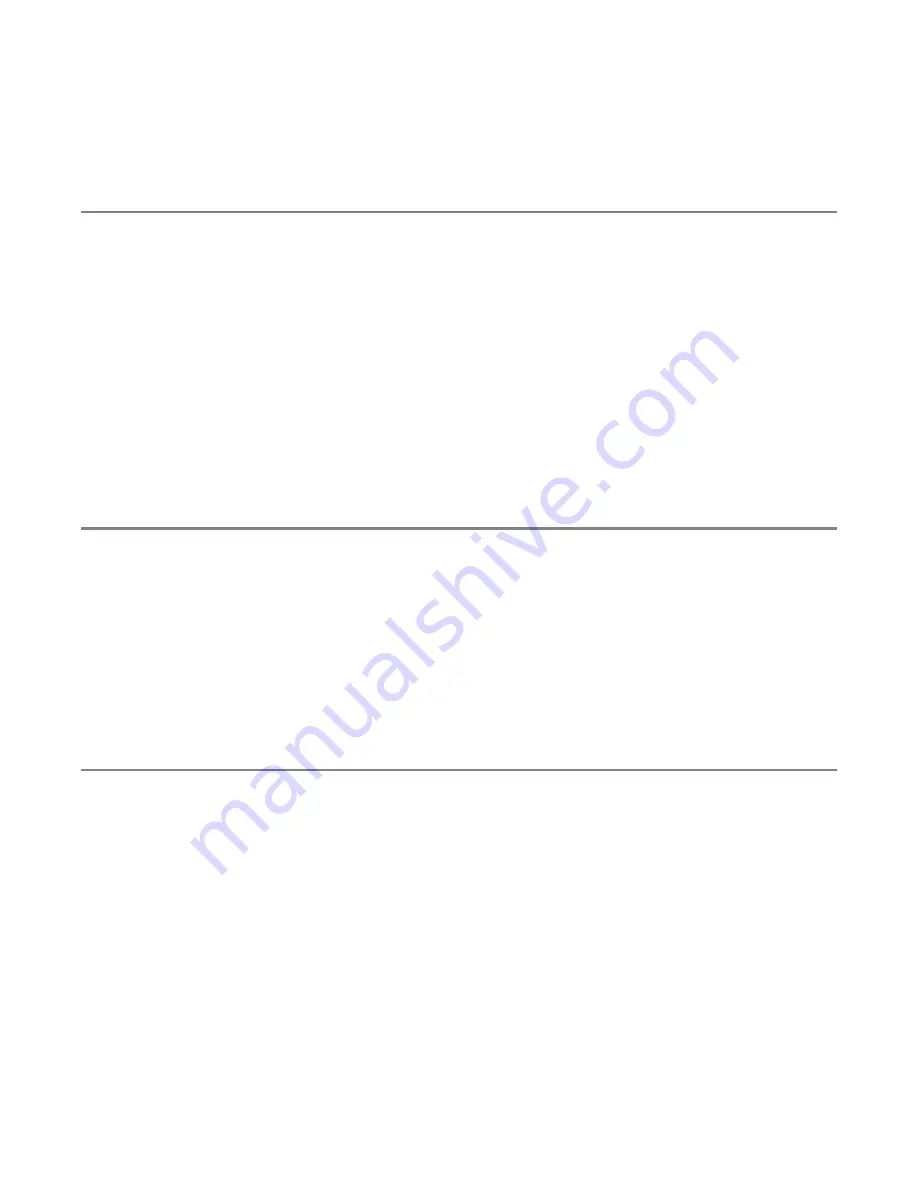
8210–00009 R1
51
9. Check all operating, lifting, and transport components. Replace damaged or worn parts before using the
conveyor.
10. Inspect the winch cable for fraying, kinking, unwinding, or other possible damage.
7.4. Lubricate the Equipment
Your equipment can operate at top efficiency only if clean fluids and lubricants are used. Use clean containers
to handle all fluids and lubricants. Store them in an area protected from dust, moisture, and other
contaminants.
1. Wipe the grease fittings with a clean cloth before greasing to avoid injecting dirt and grit.
2. Use a hand-held grease gun for all greasing.
3. If fittings will not take grease, remove and clean thoroughly.
4. Replace fittings if they are broken or will not accept grease.
5. If Intake Bushing is present in your auger, lubricate it.
Use SAE multi-purpose high-temperature grease with extreme pressure (EP) performance. SAE multi-purpose
lithium-based grease is also acceptable.
7.5. Check the Gearbox Oil
1. Remove fill/vent plug to check gearbox oil level. Insert an improvised dipstick (rolled paper or plastic tie)
into the oil filler hole to determine the oil level.
2. Note the level and the condition of the oil. Maintain oil level at half full (center of cross shaft) with 90W or
equivalent gear oil, adding as necessary or drain and refill if condition is poor.
3. Ensure gearbox is level when checking or refilling.
4. Do not overfill when adding oil.
5. Replace fill/vent plug.
7.6. Change the Gearbox Oil
Use SAE approved 90W or equivalent gear oil.
1. Remove gearbox from the conveyor.
2. Place a pan under the drain plug.
3. Use a wrench and remove the drain plug.
4. Loosen the filler plug so air can enter the gearbox and the oil will drain freely.
5. Allow the oil to drain completely.
6. Replace the drain plug.
7. Add oil until the gearbox is half full (center of cross shaft) and replace filler plug. A flexible funnel may be
required. Gearbox should be level when checking or refilling.
Do not overfill.
8. Reinstall the gearbox and guards.
S-DRIVE FIELD LOADER – PORTABLE GRAIN BELT CONVEYOR