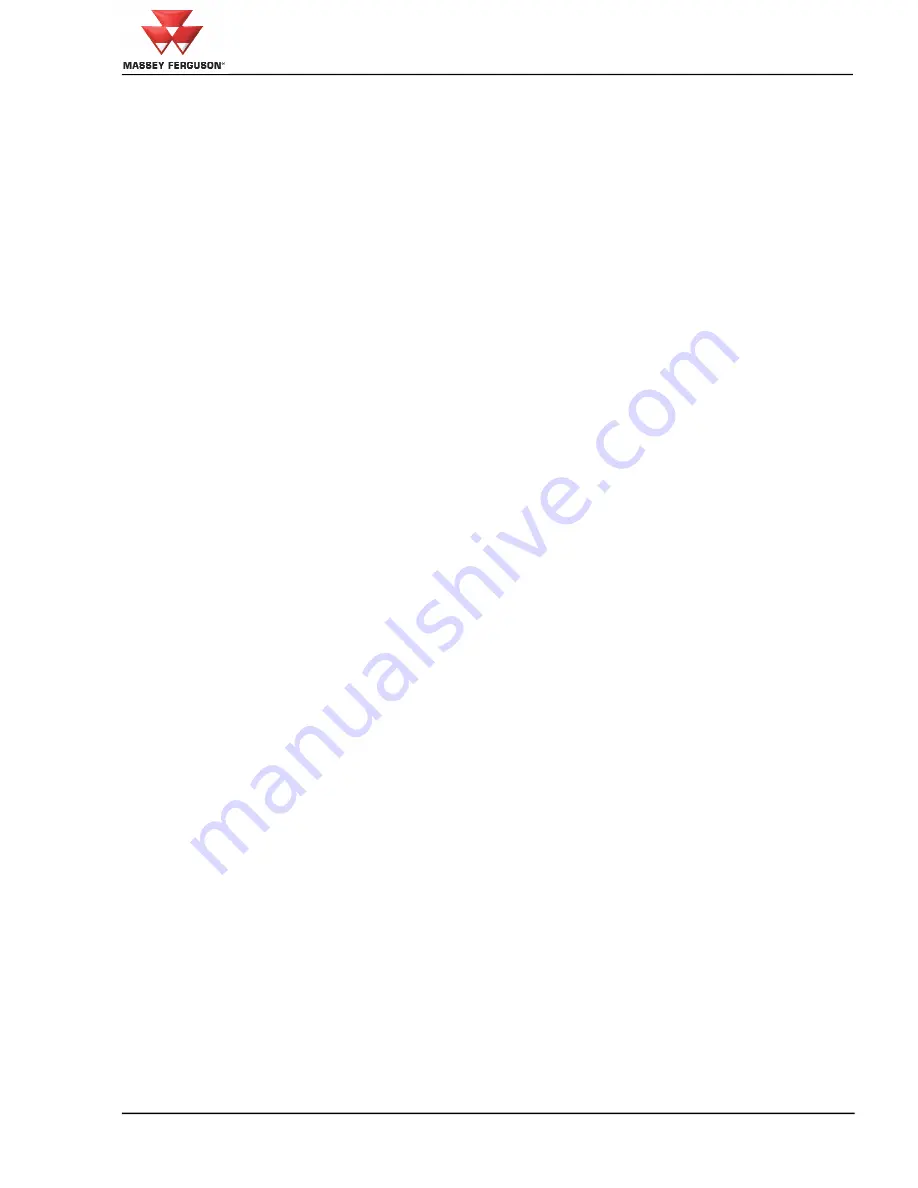
AGCO 1- 10
MF 2600 H SERIES WORKSHOP SERVICE MANUAL
INTRODUCTION AND SAFETY
Replace ‘O’ rings, seals or gaskets whenever they are
disturbed. Never mix new and old seals or ‘O’ rings,
regardless of condition. Always lubricate new seals and
‘O’ rings with hydraulic oil before installation.
When replacing component parts use the correct tool for
the job.
Hoses and Tubes
Always replace hoses and tubes if their ends are damaged.
When installing a new hose, loosely connect each end
and make sure the hose takes up the designed position
before tightening the connection. Clamps should be
tightened sufficiently to hold the hose without crushing
and to prevent chaffing or contact with other parts.
Before removing hoses or tubes make sure they are
identified so that they can be correctly re-assembled.
Be sure any hose which has been installed is not kinked
or twisted after it is tightened.
Bearings
Bearings which are considered suitable for further service
should be cleaned in a suitable solvent and immersed in
clean lubricating oil until required.
DO NOT spin bearing with compressed air the centrifugal
force could cause a ball or roller to fly outward with enough
force to cause an injury.
Installation of a bearing can be classified in two ways.
Press fit on rotating parts such as shafts & gears. Push
fit into static locations such as reduction gear housings.
Where ever possible, install the bearing onto the rotating
component first.
Always use pullers or a press to remove and / or install
bearings, bushings and cylinder sleeves, etc. Use
hammers, punches and chisels only when absolutely
necessary and be sure to wear safety goggles.
Shims
When shims are removed, tie them together and identify
them as to location. Keep shims clean and flat until they
are re-installed.
Gaskets
Be sure the holes in the gasket correspond with the
lubricant passages in the mating parts. If gaskets
are to be made, select material of the proper type
and thickness. Be sure to cut holes in the right
places. Blank gaskets can cause serious damage
– always renew gaskets prior to re-installation.
Lip Type Seals
Lubricate the lips of the lip-type seals before
installation. Use petroleum jelly. DO NOT use
grease. Ensure that the oil seal is fitted the right
way round, the lip of the seal is placed next to the
lubricant that is sealed. Some seals have a second
auxiliary lip, which is used to prevent the ingress of
dirt to the seal lip.
During Installation, if the seal lip must pass over a
shaft that has splines, a keyway, rough surface or
a sharp edge, the lip can be easily damaged. Always
use a seal protector, when one is provided.
Use of Bolts in Blind Holes
Use bolts of the correct length. A bolt which is too
long may ‘bottom’ before the head is tight against
the part it is to hold. The threads can be damaged
when a ‘long’ bolt is removed. If a bolt is too short,
there may not be enough threads engaged to hold
the part securely.
Locking Devices
Lockwashers, flat metal locks or split pins are used
to lock nuts and bolts.
Flat metal locks must be installed properly to be
effective. Bend one end of the lock around the edge
of the part. Bend the other end against one flat
surface of the nut or bolt head. Always install new
locks.
Always fit new split pins / cotter pins and bend the
ends round so that they will not catch in clothing
and help to prevent cuts.
Cables and Wires
When removing or disconnecting a group of cables
or wires, tag each one to assure proper re-assembly.
Always clip back wires and cable looms properly to
prevent chaffing, cable damage and possible
damage by fire.