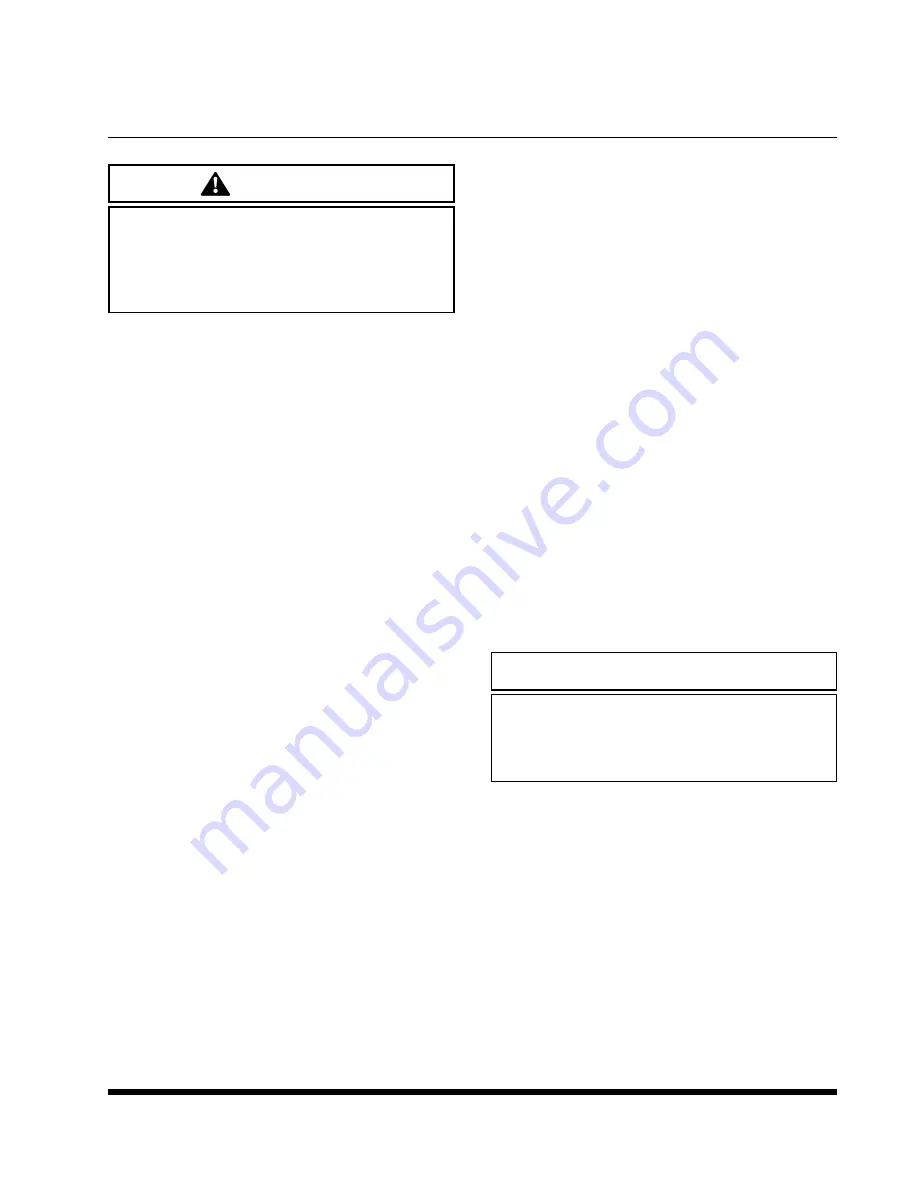
3-3 SINGLE AXLE MODEL ROCKSHAFT INSTALLATION
WARNING
TO PREVENT SERIOUS INJURY OR
DEATH, READ ALL SAFETY PRECAU-
TIONS AT THE FRONT OF THIS SEC-
TION BEFORE ATTEMPTING ANY OF
THE FOLLOWING PROCEDURES.
IMPORTANT
SEE FIGURE 3-2 FOR PART NAMES.
3-3.1
Position the rockshaft under the gauge
wheel mounting brackets.
IMPORTANT
THE GAUGE WHEEL ARMS SHOULD POINT
TOWARD THE REAR OF THE MACHINE WITH
THE CYLINDER ANCHORS FACING UP.
3-3.2
Install the upper bearings.
a.
Slip the 3/4" x 8-1/2" cap screws through the
holes provided for them in the mounting
brackets.
b.
Place the upper bearing halves (with the
grease zerk in the side) on top of the rock-
shaft with grease zerks away from the gauge
wheel arms. There are five bearing assem-
blies on the rockshaft.
IMPORTANT
BE SURE TO INSTALL THE FIFTH BEARING IN
THE CENTER, TO ITS PROPER MOUNTING
BRACKET.
c.
Use a hoist or forklift to raise the rockshaft.
Use the cap screws to guide the rockshaft
and top bearing halves into place.
3-3.3
Set a lower bearing half (with a grease
zerk between the bolt holes) under the rock-
shaft and through the hanging ends of the
cap screws.
3-3.4
Secure each set of bearings tight enough
to the rockshaft to hold the assembly to-
gether. Use the washers and locking nuts
provided.
3-3.5
Insert the rockshaft shims, as needed, be-
tween each set of bearings. Use the shims
to allow the rockshaft to rotate freely, yet not
loosely, in the bearing halves. Repeat this
step for each set of bearings.
Then tighten
the cap screws.
3-3.6
Mount the tires on the wheel rims and as-
semble to the hubs. Tighten wheel bolts
evenly to assure proper wheel alignment.
Wheel bolts should be tightened to 90 ft-lbs
of torque. The hoist can then be removed.
IMPORTANT
AN 11L X 15" FARM SERVICE TIRE SHOULD
BE USED ON THE 15" X 8" RIM. INFLATE THE
TIRE TO ITS MANUFACTURER’S RECOM-
MENDED PRESSURE.
3-3.7
Install the base end of the gauge wheel
cylinders on the frame cylinder anchors.
Face the rod end down, towards the gauge
wheel, and face the ports upwards
(See Fig-
ure 3-3)
. Secure each cylinder to the cylin-
der anchor with the clevis pins and cotter
pins supplied with the cylinder.
CAUTION
BE SURE EACH CYLINDER HAS A RE-
STRICTOR FITTING IN THE BASE END.
FAILURE TO DO SO WILL CAUSE THE
ROCKSHAFT TO FAIL.
3-3.8
Position the lockout assemblies above the
gauge wheel arms and the rod ends of the
cylinders
. The
open end of the lockouts should be over the
gauge wheel arms with the U-shaped cutout
on the opposite end facing upwards.
3-3.9
Insert the extended cylinder pin through
the lockout assembly, the cylinder clevis and
the gauge wheel arm bracket
(See Figure
. Secure with hairpin clips.
3-5
Summary of Contents for Glencoe SS7600 Series
Page 1: ...Glencoe MODEL SS7600 SERIES SOIL SAVER OPERATOR S MANUAL Form No 79019153 December 2001...
Page 2: ......
Page 4: ......
Page 11: ...NOTES 2 4...
Page 12: ...2 5 Figure 2 1 Single Axle 28 Disc 7 Shank Spacing...
Page 13: ...2 6 Figure 2 2 Single Axle 32 Disc 9 Shank Spacing...
Page 14: ...2 7 Figure 2 3 Single Axle 36 Disc 11 Shank Spacing...
Page 15: ...2 8 Figure 2 4 Tandem Axle 36 Disc 11 Shank Spacing...
Page 16: ...2 9 Figure 2 5 Tandem Axle 42 Disc 13 Shank Spacing...
Page 17: ...2 10 Figure 2 6 Tandem Axle 46 Disc 15 Shank Spacing...
Page 19: ...3 2 Figure 3 1 Tandem Axle Frame Assembly...
Page 29: ...3 12 Figure 3 8 Pull Hitch Installation...
Page 31: ...3 14 Figure 3 9 Disc Gang Installation...
Page 33: ...3 16 Figure 3 11 Disc Gang Hydraulic Installation...
Page 35: ...3 18 Figure 3 12 Rigid and Spring Clamp Installation...
Page 37: ...3 20 Figure 3 13 Decal and Light Placement on Frame Assy...
Page 39: ...NOTES 3 22...
Page 44: ...4 5 Figure 4 4 Lubrication Schedule...
Page 45: ...NOTES 4 6...
Page 48: ...NOTES 5 3...
Page 49: ......
Page 50: ......
Page 51: ...Glencoe AGCO CORPORATION 4205 River Green Parkway Duluth Georgia 30096 Printed in U S A...