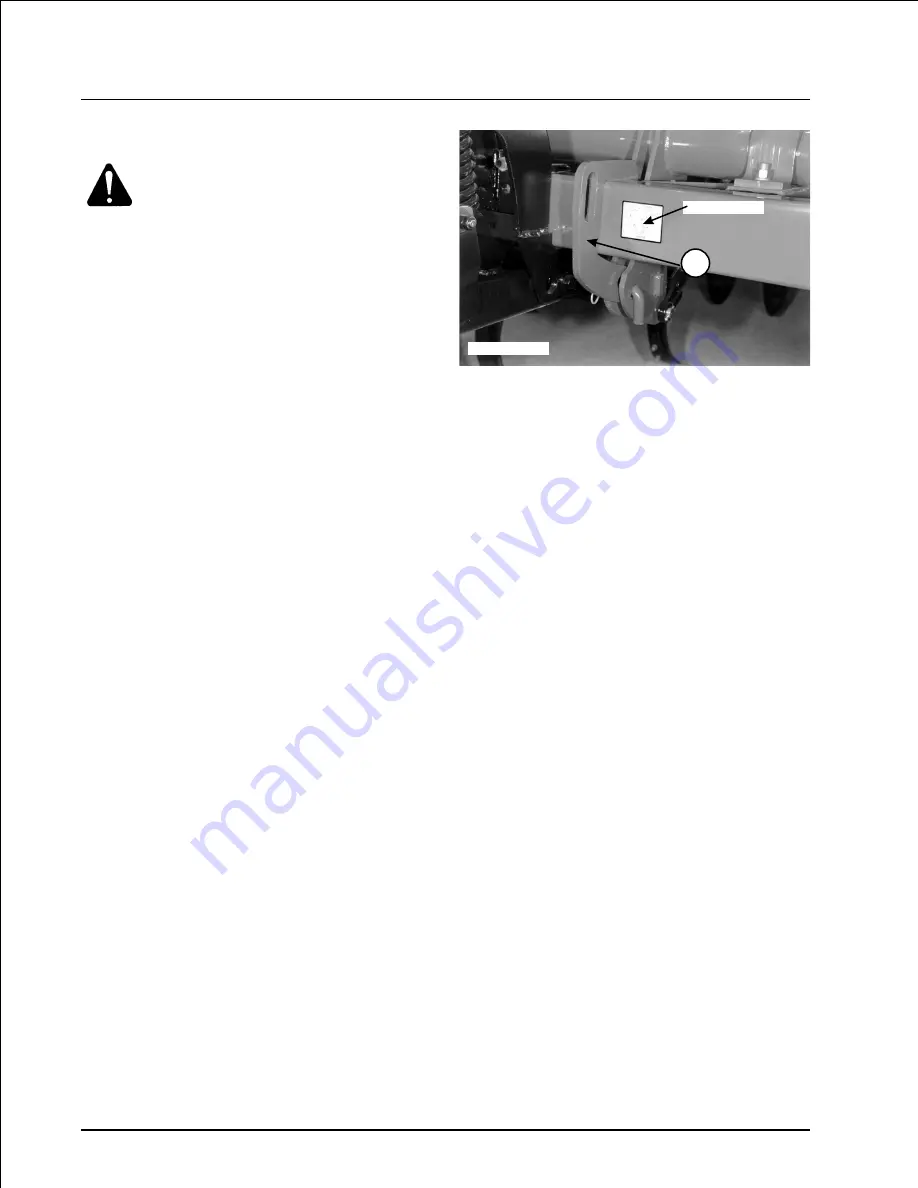
OPERATION
UNHITCHING FROM TRACTOR
WARNING! TO AVOID SERIOUS INJURY OR
DEATH, STOP TRACTOR ENGINE,
SHIFT TO PARK POSITION OR SHIFT
TO NEUTRAL AND SET BRAKES
BEFORE UNHITCHING.
Chisel Lowered
IMPORTANT!
To prevent chisel point damage, do
not lower chisel on concrete or rocks.
1. Choose a level area to unhitch. Lower chisel
plow to ground.
2. Using tractor control lever, relieve pressure in
hydraulic system.
3. Disconnect hydraulic hoses and install coupler
dust caps.
4. Install jack. Remove transport safety chain and
hitch pin.
5. Perform “End of Day” service as outlined in the
SERVICE Section.
Chisel Raised
1. Choose a level area to unhitch.
2. Install lockup on rockshaft and secure with L-pin
and cotter pin.
3. Securely block wheels.
4. Follow Steps #2 - #5, “Chisel Lowered.
10
Fig. 15 - Lockup in Lockup Position
1. Lockup
1
360459
C445-5A-1
Summary of Contents for Glencoe CC4450
Page 2: ......
Page 4: ...ii...
Page 18: ...NOTES 14...
Page 22: ...Notes 18...
Page 28: ...SERVICE TRANSPORT LIGHTING WIRING DIAGRAM 24...
Page 34: ......
Page 35: ......
Page 36: ......
Page 37: ...Glencoe AGCO CORPORATION 4205 River Green Parkway Duluth Georgia 30096 Printed in U S A...