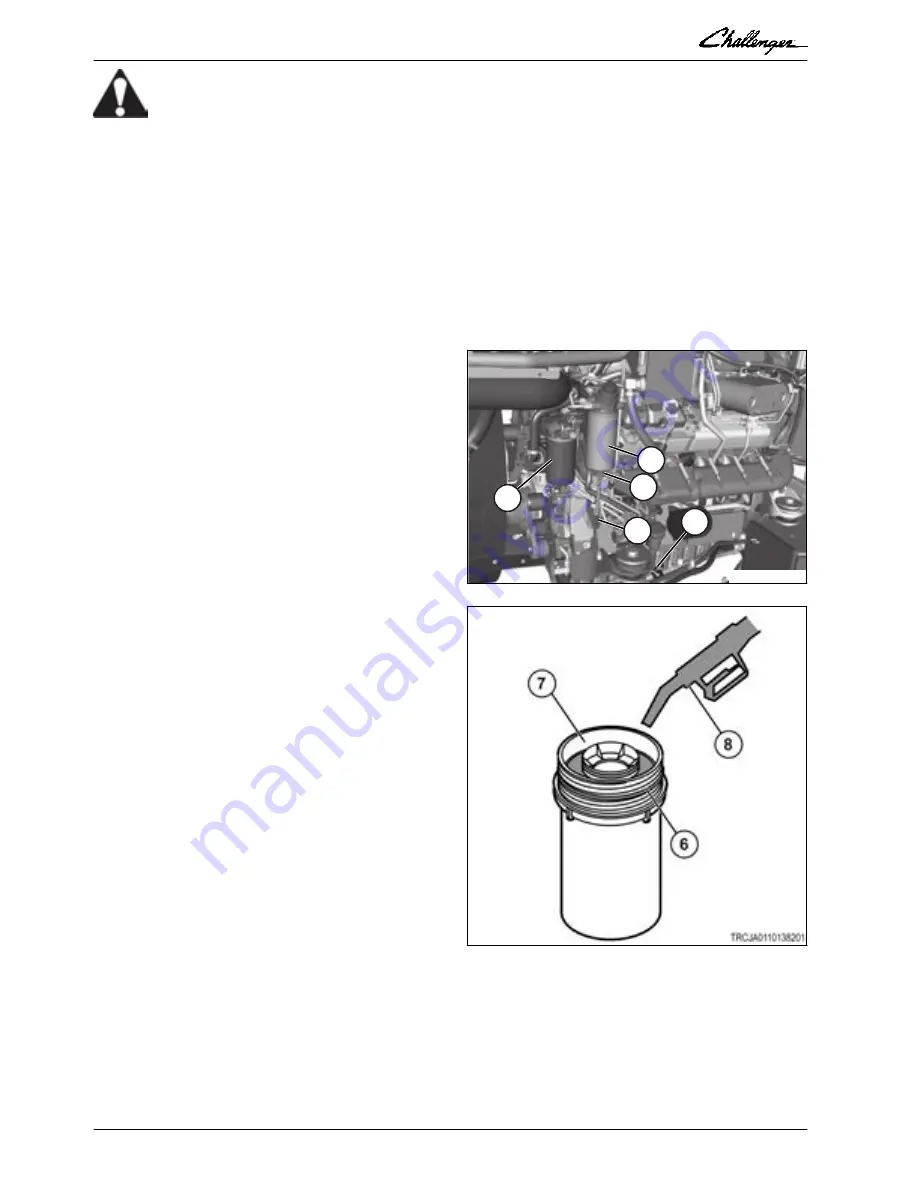
CAUTION:
Escaping fluid under pressure can penetrate skin causing serious injury. Release pressure
before disconnecting fuel or other lines. Tighten all connections before you apply pressure.
Keep hands and body away from pin holes and nozzles which eject fluids under high
pressure. Use a piece of cardboard or paper to search for leaks. Do not use your hand.
IMPORTANT:
Precaution must be necessary to be sure that the fluids are contained during performance of
inspection, maintenance, test, adjust, and repair. Be prepared to collect the fluid with correct containers
before opening a compartment or you disassemble a component with fluid. Dispose all fluids in accordance
with local regulations and mandates.
NOTE:
Replace the fuel filter elements at 800 hour intervals or if shown by fault code.
IMPORTANT:
The engine warranty is applicable only when original AGCO Power Diesel fuel filter elements
are used.
Procedure
1.
Clean the fuel filters and adjacent area.
2.
Close the fuel valve (5).
3.
Drain prefilter (2).
4.
Disconnect prefilter water detector
connector (1).
5.
Turn filter element (2) counterclockwise and
remove element from the bracket. Collect
fuel into a applicable container.
6.
Remove the water detector (3) from the
prefilter bottom end.
4
5
2
1
3
TREJA0110063201
GUID-BA2EEB53-E1B3-4D3B-9F43-16A638AB01F2-high.eps [High]
Fig. 3
7.
Remove the primary filter (4) in an equivalent
procedure.
8.
Connect the water detector (3) to the new
prefilter bottom end.
9.
Lubricate the filter element o-ring seal (6)
with clean fuel.
10.
Fill the outer shell of the filter element (7)
with clean fuel (8).
11.
Turn filter element on the bracket.
12.
Connect the water detector connector (1).
13.
The primary filter (4) is assembled in an
equivalent procedure.
14.
Open the fuel valve
15.
Prime the fuel system.
16.
Start the engine and make sure there are no
leaks.
GUID-764AE0F5-6EA1-4F5A-8ABD-EBA65A7A4869-high.jpg [High]
Fig. 4
Related Links
page 1-22
2. Engine, fuel, and exhaust system
2-8
Rubber Track Tractor
79036240F