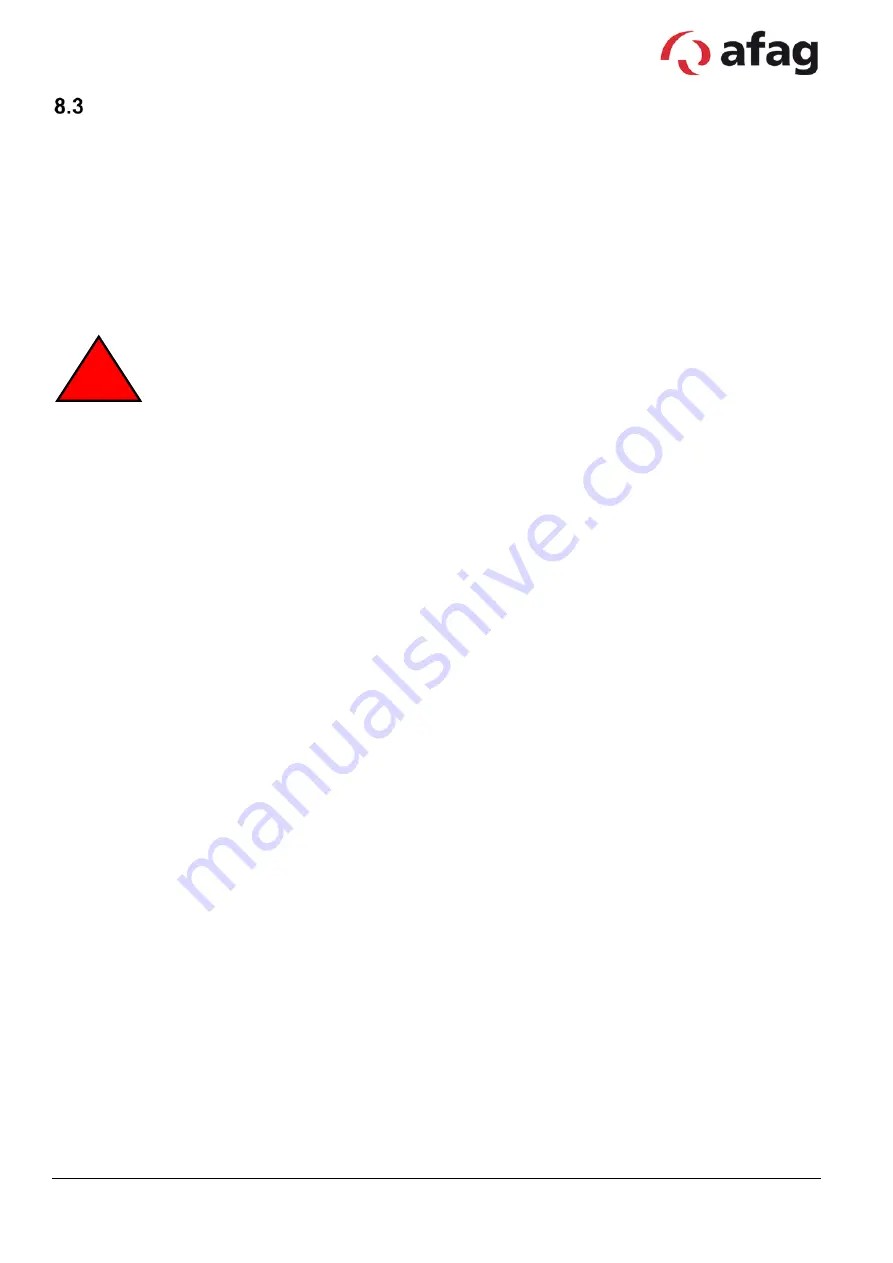
Subject to change.
32
Vers. 1.1 en 01.01.2019
Afag Hardt GmbH – Gewerbestraße 11 - 78739 Hardt - Phone:07422/56003-0
Company headquarters: 78739 Hardt, Managing Director: Walter Kunz, HRB 480966 Stuttgart
Teaching of positions on electric axes
The drive must be referenced first. Then you have the following possibilities:
Possibility 1 – move manually:
Move the axes into position by hand (logic voltage ON, motor power OFF) and then read out values
from the controller for use in the Pick&Place movement.
Danger
For the controller B1100 or E1xxx, the power pack (72 V) must be reliably disconnected
from the power supply on the primary side.
With controller C1xx0 the "safety inputs" input (X33) must be deactivated or the
power pack (72 V) reliably disconnected on the primary side.
Possibility 2 – jog mode:
•
Add value to or subtract value from current position
•
Can be programmed with relative commands.
The existing module for absolute positioning can be converted into one for relative
positioning by changing one variable.
Possibility 3:
Set-up with safely reduced speed. Please observe the manual on the safely reduced speed.
1.1 Switching distance
1.1.1 Reference sensor with electric axes
The sensor is installed parallel to the switching flag at a distance of 0.1 mm using a feeler
gauge.
!