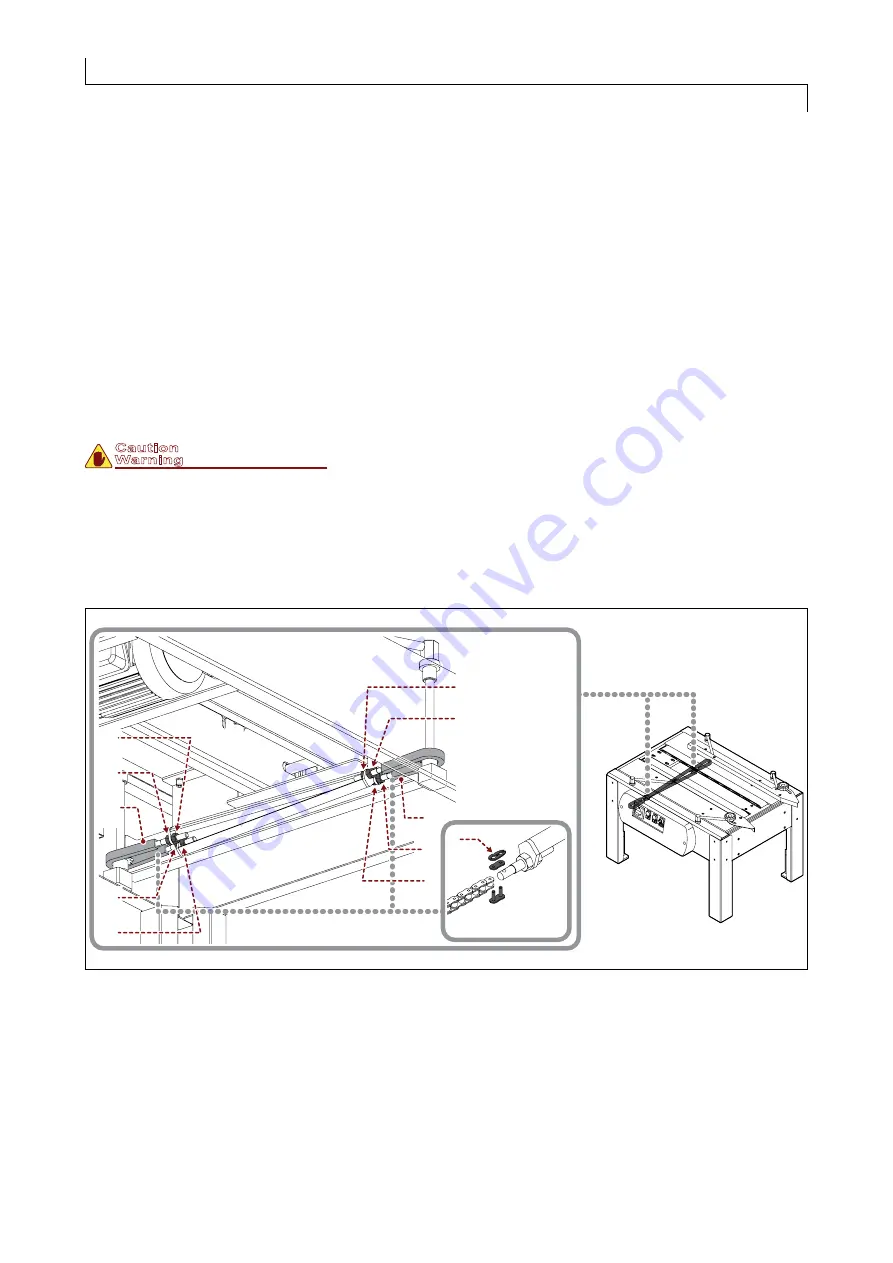
- 42 -
15C011025
F
G
E
E
F
G
E
F
F
E
T
English
Chapter 9
SPArE PArTS rEPLACEMENT INforMATIoN
9.3.
hoW To replace The self-
cenTerInG GuIde drIVInG chaIn
Proceed as indicated.
1. Deactivate the main electrical knife to stop the machine under safe
conditions.
2. Unscrew the nuts
(e - f)
to loosen chains
(G)
completely.
3. remove the chain links
(T)
and remove chains
(G)
.
4. Install the new chains and lock them with the chain links.
5.
Adjust chain tension (See 5.3. “how the adjust the driving chain of
the self-centering guides”).
6. Carry out the operation on both driving units.
7. restart the machine and check that it functions correctly.
caution
Warning
Before re-starting the machine, check that no tools or other
equipment has been left near the moving parts.
Summary of Contents for Robopac INDEX 50
Page 2: ......
Page 4: ......
Page 6: ...2 English Summary Page deliberately empty...
Page 50: ...46 English Chapter 10 Enclosed documentation Page deliberately empty...