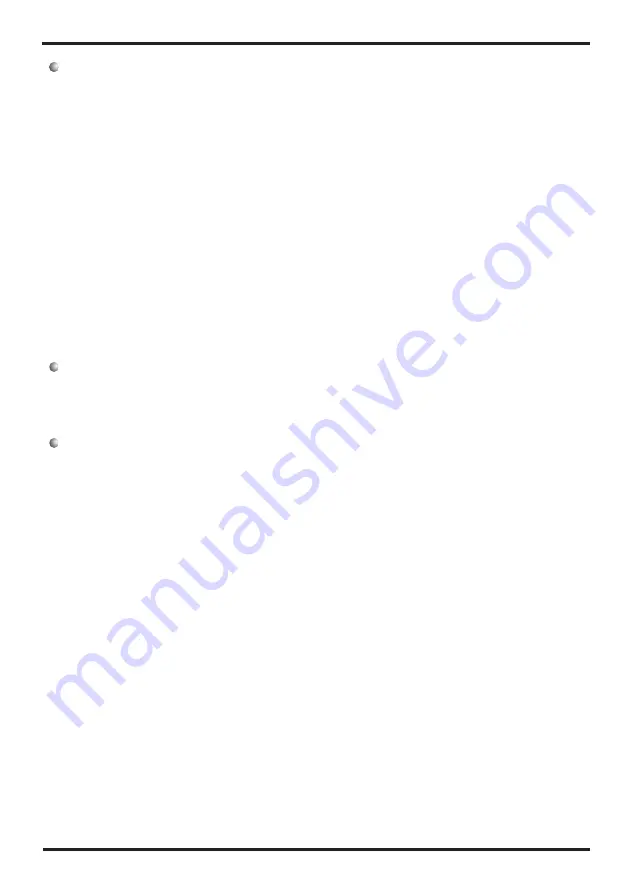
5. MAINTENANCE AND INSPECTION
5. MAINTENANCE AND INSPECTION
Removal and evacuation
When breaking into the refrigerant circuit to make repairs or for any other purpose
conventional procedures shall be used. However, it is important that best practice is
followed since flammability is a consideration. The following procedure shall be adhered to:
. Remove refrigerant;
. Purge the circuit with inert gas;
. Evacuate;
. Purge again with inert gas;
. Open the circuit by cutting or brazing.
The refrigerant charge shall be recovered into the correct recovery cylinders. The system
shall be "flushed" with OFN to render the unit safe. This process may need to be repeated
several times. Compressed air or oxygen shall not be used for this task.
Flushing shall be achieved by breaking the vacuum in the system with OFN and continuing
to fill until the working pressure is achieved, then venting to atmosphere, and finally pulling
down to a vacuum. This process shall be repeated until no refrigerant is within the system.
When the final OFN charge is used, the system shall be vented down to atmospheric
pressure to enable work to take place. This operation is absolutely vital if brazing
operations on the pipe-work are to take place.
Ensure that the outlet for the vacuum pump is not close to any ignition sources and there is
ventilation available. working on them.
Labelling
Equipment shall be labelled stating that it has been de-commissioned and emptied of
refrigerant. The label shall be dated and signed. Ensure that there are labels on the
equipment stating the equipment contains flammable refrigerant.
Recovery
When removing refrigerant from a system, either for servicing or decommissioning, it is
recommended good practice that all refrigerants are removed safely.
When transferring refrigerant into cylinders, ensure that only appropriate refrigerant
recovery cylinders are employed. Ensure that the correct number of cylinders for holding
the total system charge is available. All cylinders to be used are designated for the
recovered refrigerant and labelled for that refrigerant (i.e. special cylinders for the recovery
of refrigerant). Cylinders shall be complete with pressure relief valve and associated shut-
off valves in good working order. Empty recovery cylinders are evacuated and, if possible,
cooled before recovery occurs.
The recovery equipment shall be in good working order with a set of instructions
concerning the equipment that is at hand and shall be suitable for the recovery of
flammable refrigerants. In addition, a set of calibrated weighing scales shall be available
and in good working order. Hoses shall be complete with leak-free disconnect couplings
and in good condition. Before using the recovery machine, check that it is in satisfactory
working order, has been properly maintained and that any associated electrical
components are sealed to prevent ignition in the event of a refrigerant release. Consult
manufacturer if in doubt.
The recovered refrigerant shall be returned to the refrigerant supplier in the correct
recovery cylinder, and the relevant Waste Transfer Note arranged. Do not mix refrigerants
in recovery units and especially not in cylinders.
If compressors or compressor oils are to be removed, ensure that they have been
evacuated to an acceptable level to make certain that flammable refrigerant does not
remain within the lubricant. The evacuation process shall be carried out prior to returning
the compressor to the suppliers. Only electric heating to the compressor body shall be
employed to accelerate this process. When oil is drained from a system, it shall be carried
out safely.
32
5. MAINTENANCE AND INSPECTION
5. MAINTENANCE AND INSPECTION
Repairs to sealed components
1) During repairs to sealed components, all electrical supplies shall be disconnected from
the equipment being worked upon prior to any removal of sealed covers, etc. If it
isabsolutely necessary to have an electrical supply to equipment during servicing, then a
permanently operating form of leak detection shall be located at the most critical point to
warn of a potentially hazardous situation.
2) Particular attention shall be paid to the following to ensure that by working on electrical
components, the casing is not altered in such a way that the level of protection is affected.
This shall include damage to cables, excessive number of connections, terminals not made
to original specification, damage to seals, incorrect fitting of glands, etc.
Ensure that apparatus is mounted securely.
Ensure that seals or sealing materials have not degraded such that they no longer serve
the purpose of preventing the ingress of flammable atmospheres. Replacement parts shall
be in accordance with the manufacturer's specifications.
NOTE: The use of silicon sealant may inhibit the effectiveness of some types of leak
detection equipment. Intrinsically safe components do not have to be isolated prior to
working on them.
Detection of flammable refrigerants
Under no circumstances shall potential sources of ignition be used in the searching for or
detection of refrigerant leaks. A halide torch (or any other detector using a naked flame)
shall not be used.
Repair to intrinsically safe components
Do not apply any permanent inductive or capacitance loads to the circuit without ensuring
that this will not exceed the permissible voltage and current permitted for the equipment in
use.
Intrinsically safe components are the only types that can be worked on while live in the
presence of a flammable atmosphere. The test apparatus shall be at the correct rating.
Replace components only with parts specified by the manufacturer. Other parts may result
in the ignition of refrigerant in the atmosphere from a leak.
Cabling
Check that cabling will not be subject to wear, corrosion, excessive pressure, vibration,
sharp edges or any other adverse environmental effects. The check shall also take into
account the effects of aging or continual vibration from sources such as compressors or
fans.
Leak detection methods
The following leak detection methods are deemed acceptable for systems containing
flammable refrigerants.
Electronic leak detectors shall be used to detect flammable refrigerants, but the sensitivity
may not be adequate, or may need re-calibration. (Detection equipment shall be calibrated
in a refrigerant-free area.) Ensure that the detector is not a potential source of ignition and
is suitable for the refrigerant used. Leak detection equipment shall be set at a percentage
of the LFL of the refrigerant and shall be calibrated to the refrigerant employed and the
appropriate percentage of gas (25 % maximum) is confirmed.
Leak detection fluids are suitable for use with most refrigerants but the use of detergents
containing chlorine shall be avoided as the chlorine may react with the refrigerant and
corrode the copper pipe-work.
If a leak is suspected, all naked flames shall be removed/ extinguished.
If a leakage of refrigerant is found which requires brazing, all of the refrigerant shall be
recovered from the system, or isolated (by means of shut off valves) in a part of the system
remote from the leak. Oxygen free nitrogen (OFN) shall then be purged through the system
both before and during the brazing process.
31
Summary of Contents for hydro-pro PX
Page 38: ...Code ...