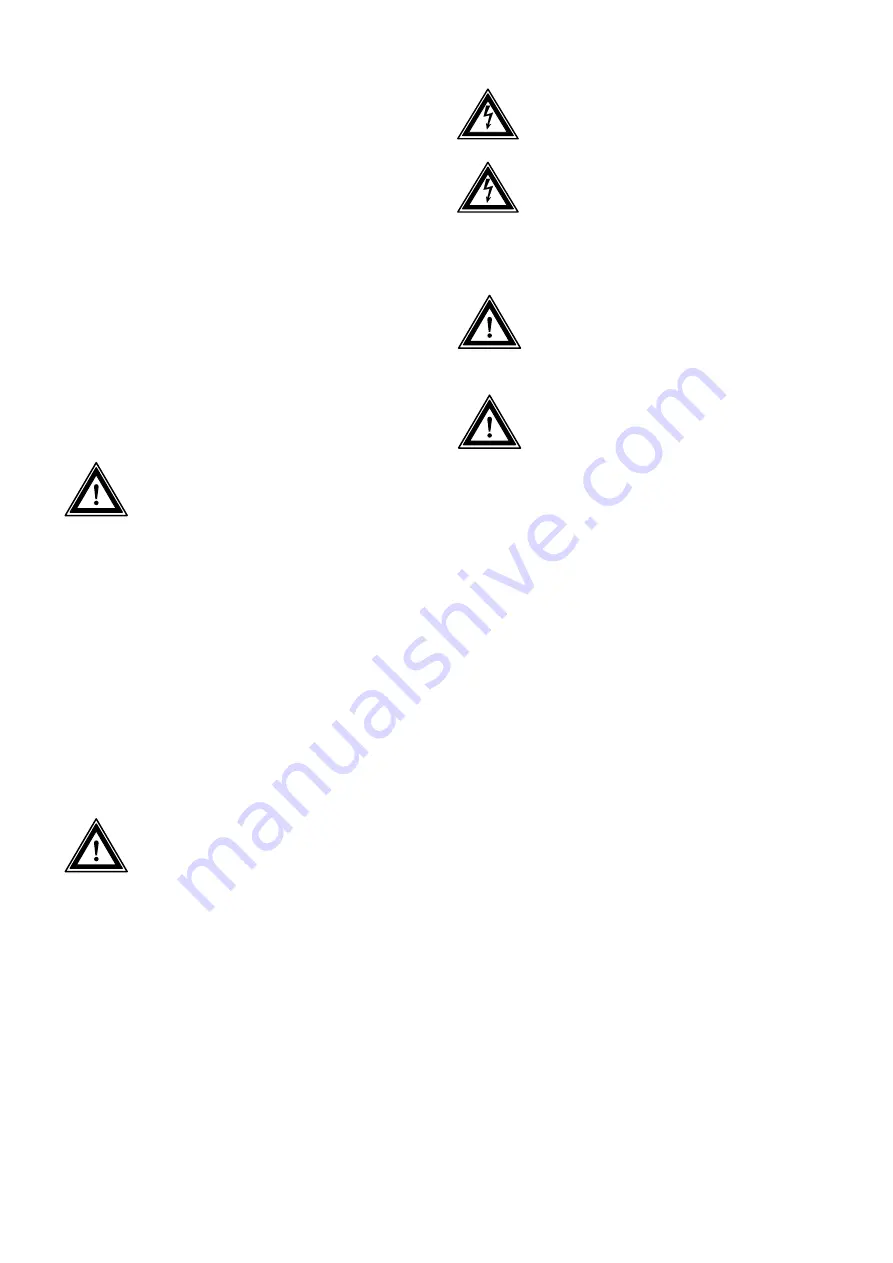
46
WATER COIL CONNECTION
All the water coil collectors are provided with male threaded connections for
water inlet and outlet.
For correct installation, abide by the following simple
indications:
• in the event of bad weather conditions, it is recommended to provide anti-
freeze devices;
• the pipe path must be studied in order not to create obstacles when the
coil is extracted and to not make inspection and maintenance of the unit
and other accessories impossible;
• while screwing the collectors and hydraulic circuit, do not generate strains
which could damage the coil collectors;
• provide shut-off valves to isolate the coil from the rest of the circuit should
it need to be disconnected from the hydraulic circuit;
• clamp the pipes adequately to the outside of the unit to prevent the weight
being unloaded onto the coil;
• to connect the water supply pipes, respect the indications on the plates
reading “WATER INLET” and “WATER OUTLET” on the outside panelling;
• mount an air bleed valve at the highest part of the circuit and a water drain
valve at the lowest part;
• when connection has been made, place the external rubber gasket flush
with the panel to prevent seepage of air.
ATTENTION!
In case of heating functioning, in order to prevent burns the
pipes must be isolated effectively with suitable material flush
with the panelling.
DIRECT EXPANSION COILS CONNECTION
The coils are supplied with hermetically sealed connections and
pressurised with inert gas.
For correct installation, abide by the following simple
indications:
• the pipe path must be studied in order not to create obstacles when the
coil is extracted and to not make inspection and maintenance of the
unit and other accessories impossible;
• provide adequate clamping units to support the pipes so that their
weight is not supported by the recovery unit;
• when connection has been made, place the external rubber gasket flush
with the panel to prevent seepage of air;
•
the coil performance stated in this manual may be subject to
variations if its connection piping to a motocondensing causes excessive
refrigerant pressure drops.
ATTENTION!
In order to prevent burns the pipes must be isolated
effectively with suitable material flush with the
panelling.
ELECTRICAL CONNECTIONS: EARTH
ATTENTION
!
The electrical connections and wiring must be carried
out by personnel with the necessary requisites in
accordance with current regulations.
ATTENTION!
Every electrical utility must be connected to the system
earth plant. Use the connectors marked with the earth
symbol to perform the earth connection of the unit
and of other accessories to the building.
CONNECTION TO THE ELECTRIC NETWORK
ATTENTION!
Make sure that the network features are compatible
with the electrical features indicated on the machine
plate.
Electrical connections: electric coils
ATTENTION!
Make sure that the network features are compatible
with the electrical features indicated on the
component plates.
Follow the indications given below for correct electric battery
connection:
• provide adequate protection upstream the unit with residual circuit
breaker switches;
• always connect the safety thermostats to ensure power shut-off of
the electric battery in case of overtemperature;
• the safety thermostats must be in series with the control
thermostat (not supplied);
• the battery power supply must be interlocked with the fans;
• always connect the earth cable of the electric battery to the proper
terminal in the electric box.
The connection wiring diagrams are supplied with the machine.
ELECTRICAL CONNECTIONS: ELECTRIC MOTORS
The electric motors are connected on the terminal boards mounted
inside the unit for TA 09-11-15 and on the screw feeder of one of the
fans for TA 19-24-33-40-50 units.
For units equipped with two motors, the power and earth cables are
provided on a terminal board for each fan.
Summary of Contents for TA 09
Page 2: ......
Page 51: ...51 WIRING DIAGRAMS TA09 E WMT05 PE L N 230V 50Hz IG MAX MED MIN ...
Page 52: ...52 TA09 E WMT06 PE L N 230V 50Hz IG VF VC MAX MED MIN ...
Page 53: ...53 TA09 E WMT10 PE L N 230V 50Hz IG VF VC MAX MED MIN ...
Page 56: ...56 TA19 24 CON WMT05 E MOTORE CMC PE L N 230V 50Hz IG KA1 KA2 KA3 MAX MED MIN ...
Page 57: ...57 TA19 24 CON WMT06 E MOTORE CMC PE L N 230V 50Hz IG KA1 KA2 KA3 VC VF MAX MED MIN ...
Page 58: ...58 TA19 24 CON WMT10 E MOTORE CMC PE L N 230V 50Hz IG KA1 KA2 KA3 VC VF MAX MED MIN ...
Page 59: ...59 TA33 50 CON WMT05 E MOTORE CMC PE L N 230V 50Hz IG KA1 KA2 KA3 MAX MED MIN MAX MED MIN ...
Page 69: ...69 STO MAX MED MIN 82 82 38 PX mm PX mm ...
Page 70: ......
Page 71: ......