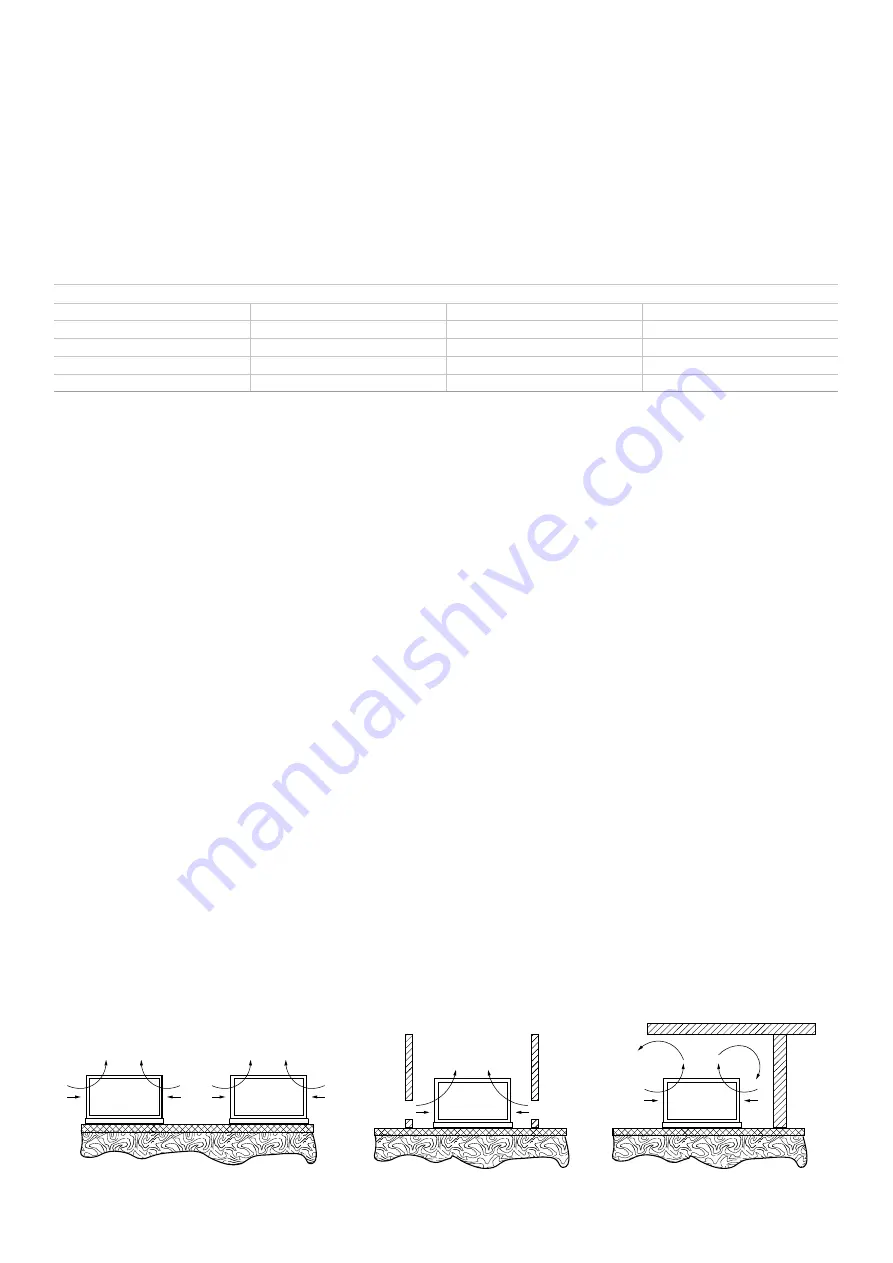
9
STORAGE
PLACEMENT AND INSTALLATION REQUIREMENTS
For unit installation it is important to perform the following preliminary
preparation tasks:
• When installing, make sure that the atmospheric or environmental agents
do not affect and corrode the cooling circuit components, causing the
refrigerant to leak in the environment and, if so, make the appropriate
adjustments.
• The air-cooled units with fans are designed for outdoor installation.
Contact Aermec before making any type of installation.
• The water-cooled units are designed for indoor installation. Contact
Aermec before making any type of installation.
• For the positioning of the air-cooled units for outdoor use, choose a place
that is not exposed to excessive wind (install windbreaks if the wind speed
exceeds 86.6in/s).
• The soil under the unit must be flat, smooth and sufficiently strong to
withstand the weight of the unit with a full refrigerant load, as well as the
occasional presence of the normal maintenance equipment.
• In locations exposed to frost, if the unit is installed on soil, the support
base must rest on concrete columns with a depth greater than the normal
depth of frost of the soil. It is always advisable to build a support base
separate from the main building to avoid the transmission of vibrations.
• If the machine is installed in a place potentially subject to snow accumu-
lation or ice formations in the base, it is recommended to install the unit
with at least 11.8 in above the ground.
• For normal applications, the rigidity of the unit and the positioning of
point loads allow for an installation that minimises vibrations. In the case
of installations requiring particularly low vibration levels, you can use the
anti-vibration supports.
ATTENTION: The use of anti-vibration supports MUST be combined with
the installation in the unit water piping of flexible couplings. The anti-
vibration supports must be fixed to the unit BEFORE it is earthed. AERMEC
is not responsible for the choice of capacity of the anti-vibration supports.
•
For installation on vibration dampers:
The unit must be fixed to the anti-vibration supports and these firmly
fixed to the concrete base, see chapter weight distribution and minimum
technical spaces
• For installation without vibration dampers:
fix the unit to the base using
screws with the necessary resistance
• Check that the contact surfaces of the anti-vibration supports are levelled
to the base. If necessary, use spacers or level the base but, in any case,
make sure that the anti-vibration supports rest flat on the base surface.
• It is essential that the units are installed leaving sufficient space around
them to allow easy access to the components for maintenance and repair
purposes. Only for air-cooled devices: if the air output by the condensers
encounters any obstacle, it tends to return to the fans. This leads to an
increase in the temperature of the air used to cool the condensers. The
obstructions at the air outlet also negatively impact the distribution of
the air over the entire surface of the condenser’s thermal exchange. Both
of these conditions, which reduce the thermal exchange capacity of the
coils, cause an increase in the condensation pressure. This leads to a loss of
power and an increase in the compressor absorption.
• Only for air-cooled chillers: to prevent the air flow from inverting due to
dominating winds, the units must not be completely covered by a high
and continuous windbreak. If it is not possible to avoid this configuration,
an air exhaust duct can be installed at the same height of the surround-
ing shield, upon written approval of an AERMEC representative.
• Unit for installation at max. 2000m a.s.l.
ATTENTION: It is important that the units are installed flat. The improper
installation of the unit invalidates the warranty.
Recommended Installation
Windbreak
recommended with wind above 86.6 in/s
Installation not allowed
Recommended 90.6in
Maximum storage temperature
Refrigerant
Type
Class
Max. Temp. (°F)
R134a
HFC
A1
<122 °F
R410A
HFC
A1
<122 °F
R1234ze
HFO
A2L
<122 °F
R513A
HFO
A1
<122 °F
It may happen that, after receipt, the units are not to be immediately installed
and are kept in storage. In case of medium-long term storage, we recommend
applying the following procedures:
• Make sure there is no water inside the hydraulic systems.
• Do not remove the protections from the heat exchanger.
• Do not remove the plastic protective films.
• Make sure that the electrical panels are closed.
• Before using the equipment, store all items provided in a dry and clean
place so that they can be used in the future. We recommend storing the
unit in a dry and sheltered place (especially for units intended for indoors).
NOTE The maximum storage temperature of the units depends on the
type of refrigerant contained, see table. Beyond this limit, there is a risk of
refrigerant leaking through the safety valves.
STORAGE
Summary of Contents for ANKI 020
Page 2: ......
Page 5: ...5 CERTIFICATIONS COMPANY CERTIFICATIONS SAFETY CERTIFICATIONS ...
Page 27: ......