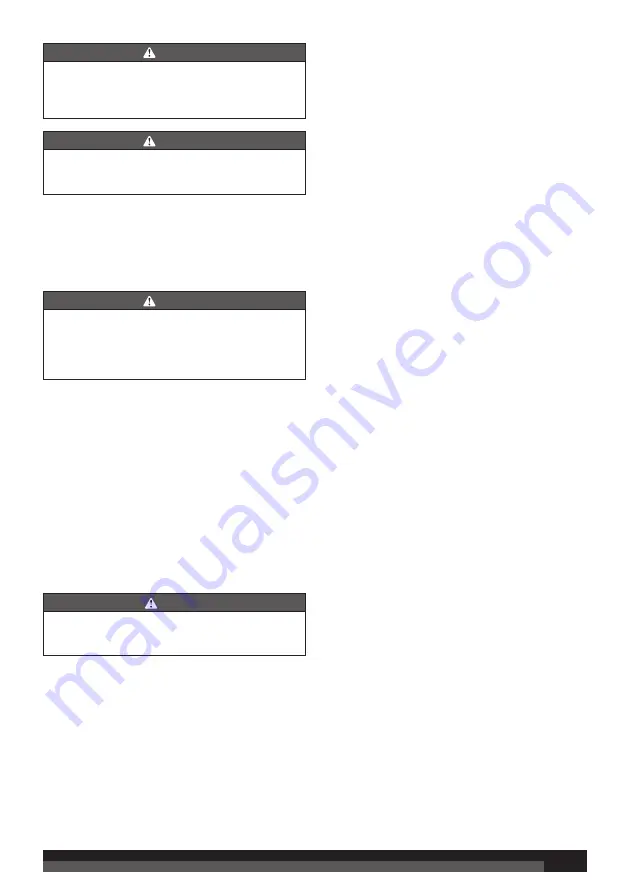
8
WARNING
Always wear eye protection with side shields marked
to comply with ANSI Z87.1. Failure to do so could
result in objects being thrown into your eyes resulting
in possible serious injury.
WARNING
Disconnect the tool from the air supply before
performing maintenance. Failure to do so could result
in serious personal injury.
GENERAL MAINTENANCE
Avoid using solvents when cleaning plastic parts. Most
plastics are susceptible to damage from various types of
commercial solvents and may be damaged by their use.
Use clean cloths to remove dirt, dust, oil, grease, etc.
WARNING
Do not at any time let brake fluids, gasoline, petroleum-
based products, penetrating oils, etc., come in contact
with plastic parts. Chemicals can damage, weaken or
destroy plastic which may result in serious personal
injury.
LUBRICATION
Frequent, but not excessive, lubrication is required for
best performance. Oil for pneumatic fastening tools
added through the air line connection will lubricate the
internal parts. Do not use detergent oil or additives as
these lubricants will cause accelerated wear to the
seals and bumpers in the tool, resulting in poor tool
performance and frequent tool maintenance.
COLD WEATHER OPERATION
For cold weather operation, near and below freezing,
the moisture in the air line may freeze and prevent tool
operation. We recommend the use of air tool lubricant or
permanent antifreeze (ethylene glycol) as a cold weather
lubricant.
CAUTION
Do not store tools in a cold weather environment to
prevent frost or ice formation on the tools’ operating
valves and mechanisms that could cause tool failure.
NOTE:
Some commercial air line drying liquids are
harmful to “O” rings and seals. Do not use these low
temperature air dryers without checking compatibility.
AIR SUPPLY PRESSURE AND VOLUME
Air volume is as important as air pressure. The air
volume supplied to the tool may be inadequate because
of undersize fittings and hoses, or from the effects of dirt
and water in the system. Restricted air flow will prevent
the tool from receiving an adequate volume of air, even
though the pressure reading is high. The results will be
a slow operation, misfeeds or reduced driving power.
Before evaluating tool problems for these symptoms,
trace the air supply from the tool to the supply source
for restrictive connectors, low points containing water and
anything else that would prevent full volume flow of air
to the tool.
REQUIRED DAILY CHECKLIST
See figure 18 - 19.
1. Disconnect the air supply from the tool and remove
all fasteners.
2. Check all screws, nuts, bolts, and pins on the tool. If
any of these are loose, they must be tightened with
the appropriate size wrench.
3. Press the workpiece contact against a workpiece to
ensure that it moves smoothly.
4. With the workpiece contact depressed, pull the
trigger. The trigger should move smoothly, without
binding.
5. While the tool is not loaded, connect the appropriate
air supply 4.8 bar (70 psi) to the tool.
6. Rotate the selectable trigger knob on the trigger to
single sequential actuation operation, position A
(See
figure 18)
. No air should leak from the tool.
●
Without pulling the trigger, press the workpiece
contact against a workpiece several times. The
tool must not operate.
●
With the workpiece contact not engaged on the
workpiece, point the tool down and away and pull
the trigger several times. Hold the trigger in this
position for a minimum of 5 seconds. The tool
must not operate.
●
Press the workpiece contact firmly against the
workpiece. Pull the trigger. The tool must operate.
●
With the workpiece contact still depressed,
release the trigger. The driver must return to its
up position.
7. Rotate the selectable trigger knob on the trigger to
contact actuation operation, position b
(See figure 19)
.
●
With the workpiece contact not engaged on the
workpiece, point the tool down and away. Pull the
trigger. The tool must not operate.
●
Keeping the trigger fully depressed, push the
workpiece contact against a workpiece. The tool
must operate.
8. If the tool successfully meets all the requirements in
this checklist, it is ready for use. Set the trigger on
the tool to operate in the manner that best fits your
application. Load the proper fasteners for the desired
application.
Note:
Do not use this tool in the contact actuation
mode unless you have had training in the use of
this mode of operation. Untrained or inexperienced
operators should not use the contact actuation mode.
9. Set the depth of drive according to the
drive depth
adjustment
section in this manual. Repeat this
checklist before using the tool each day, or if the tool
is dropped or damaged in any way.
REPLACING THE WIRE DEFLECTOR
See figure 20 - 21.
Over time, the wire deflector will wear and should be
replaced.