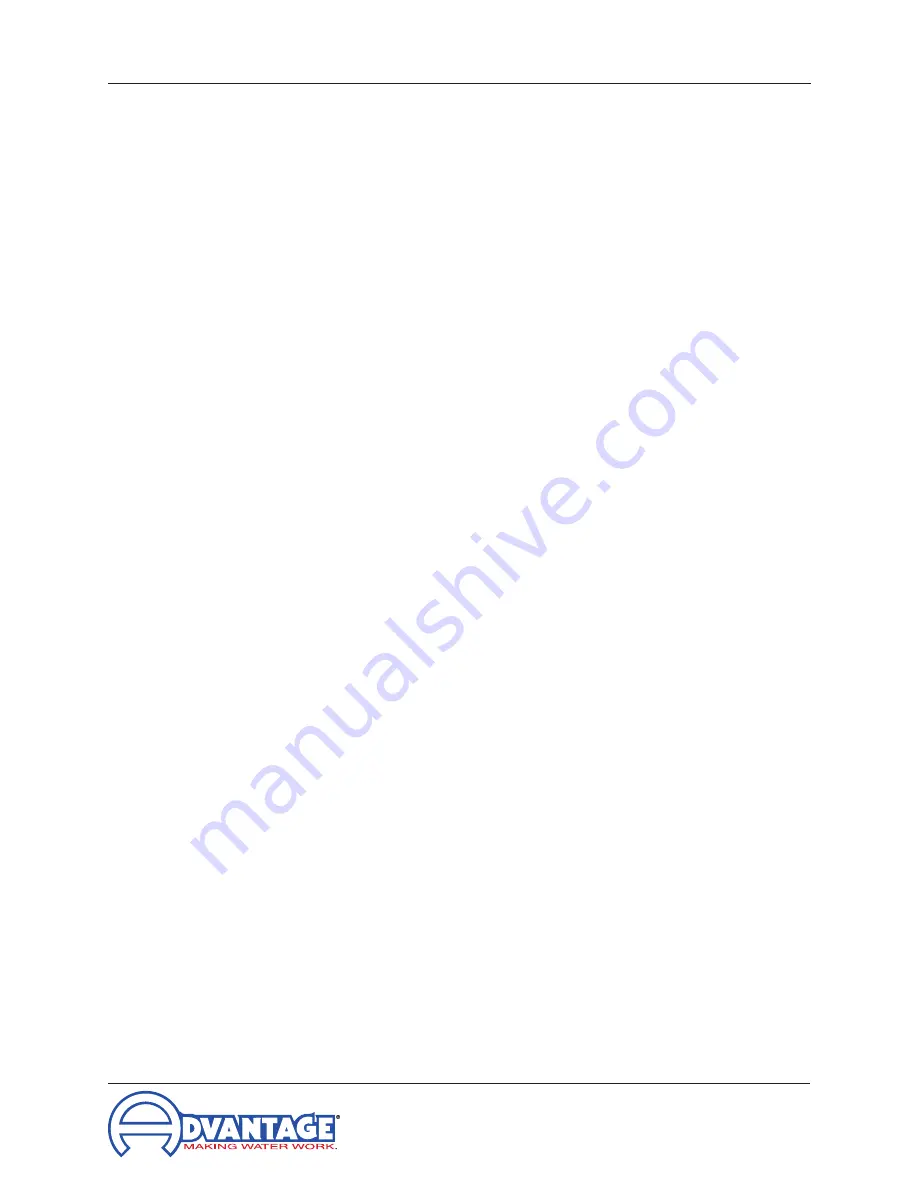
Temperature Control Units : Sentra with T300 Control Instrument
Page: 21
Advantage Engineering, Inc.
525 East Stop 18 Road Greenwood, Indiana 46142
317-887-0729 Fax: 317-881-1277
Service Department Fax: 317-885-8683 www.AdvantageEngineering.com
3.0 OPERATIONS
3.1 General
3.2
Machine Start Up and Operation
3.3
Instrument Operation : Basic Use
3.4
Instrument Operation : Basic Setup
3.5
Instrument Operation : Remote Setup
3.6
Instrument Operation : Features Setup
3.7
Instrument Operation : Machine Setup
3.8
Instrument Operation : Tools and Status
3.9
Shut Down Sequence
Summary of Contents for SENTRA SRT-1045-300
Page 2: ......
Page 6: ...Page 6 THIS PAGE INTENTIONALLY BLANK ...
Page 12: ...Page 12 THIS PAGE INTENTIONALLY BLANK ...
Page 44: ...Page 44 THIS PAGE INTENTIONALLY BLANK ...
Page 50: ...Page 50 THIS PAGE INTENTIONALLY BLANK ...
Page 64: ...Page 64 THIS PAGE INTENTIONALLY BLANK ...
Page 68: ...Page 68 THIS PAGE INTENTIONALLY BLANK ...
Page 76: ...Page 76 THIS PAGE INTENTIONALLY BLANK ...
Page 89: ...END 2023 Advantage Engineering Inc RE 20230329 ...
Page 90: ......